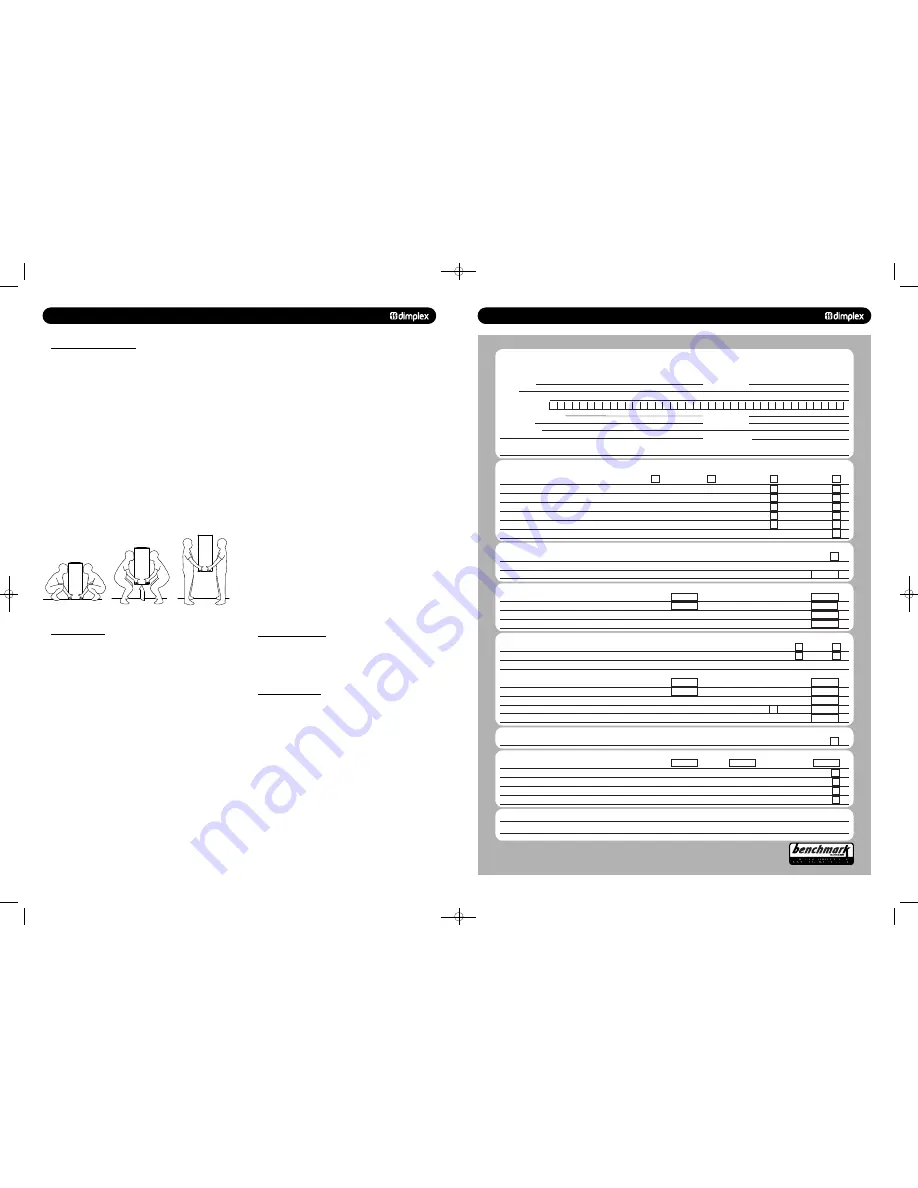
1.0
INTRODUCTION
1. The appliances incorporate a microprocessor based, fully
modulating air/gas ratio control system with direct burner
ignition. This provides a modulated heat output to either
central heating (CH) or domestic hot water (DHW) demands,
with internal frost protection provided as standard. The heat
exchanger is constructed from stainless steel encased in high
temperature polymer.
A combined circulating pump, diverter valve and automatic air
vent assembly, pressure gauge, safety valve and system
expansion vessel are included.
Isolation valves are fitted to the service connections. The
appliances have a DHW flow detection device, which gives
priority to DHW demand and proportions the required heating
load to the DHW flow rate. An electro-mechanical 24 hour
time clock is also fitted as standard.
The boiler has a pump over run feature therefore the central
heating system must include either a proprietary automatic
bypass valve or a radiator must be fitted with lock shield
valves. A separate CH expansion vessel is not required if the
total CH system content is less than 84 litres. However one is
required for systems with volumes greater than 84 litres; refer
to section 6.5. A separate DHW expansion vessel is not
required. It is recommended that a drain cock is fitted at the
lowest point in the system.
6
© Dimplex Boilers 2008
1.5
DESCRIPTION
RF room thermostats etc, are available as optional extras.
The integral clock may be removed, however the hole in the
fascia must be covered using a fascia blanking panel
(part no. 300635).
2. The boiler is set to give a maximum output of:-
24kW Model
- 24kW DHW
19.7kW CH (condensing)
30kW Model
- 30kW DHW
25.4kW CH (condensing)
38kW Model
- 38kW DHW
32kW CH (condensing)
3. It is designed for use on Natural Gas (G20). A natural gas to
propane conversion kit is available for each Dimplex Combi.
4. The boiler is suitable for use only on fully pumped sealed
heating systems. Priority is given to domestic hot water.
5. The boiler data badge gives details of the model, serial
number and Gas Council number and is situated on the inner
door panel. It is visible when the case front panel is lowered.
(Fig. 1)
6. The boiler model name and serial number are also shown on
the information label on the inside of the fascia. This is for
user reference.
7. The boiler is intended to be installed in residential /
commercial / light industrial E.M.C. environments on a
governed meter supply only.
8. The boiler must be installed with one of the purpose
designed flues such as the standard horizontal telescopic flue
kit, part no. 956120.
9. A
All systems must be thoroughly flushed and treated with
inhibitor (see section 6.2).
1.6
OPTIONAL EXTRAS
• Boiler
• Wall fixing jig
• Templates & ‘Quick Fit’ Guide
• Literature Pack
• Filling Loop
• Plugs and screws
1.7
PACK CONTENTS
1.4
SAFE MANUAL HANDLING
1. The boiler should be handled and lifted by two people.
Wear appropriate Personal Protection Equipment e.g. protective
gloves, safety footwear etc.
Plan your route to minimise the number of turns needed to
handle/lift the boiler.
2. Where possible transport the boiler using a sack truck or
other suitable trolley. Try to avoid steps, wet or slippery
surfaces, unlit areas etc. and take special care on ladders/into
lofts.
3. When handling or lifting always use safe techniques - keep
your back straight, bend your knees. Don’t twist - move your
feet, avoid bending forwards and sideways and keep the load
as close to your body as possible.
4. Asses the risks associated with handling and lifting
according to the conditions on site. If in doubt seek advice
before proceeding. Health and Safety is the responsibility of
everyone.
17.0
BENCHMARK
© Dimplex Boilers 2008
43
GAS BOILER SYSTEM COMMISSIONING CHECKLIST
CONTROLS
Tick the appropriate boxes
Time and Temperature Control to Heating
Room Thermostat and
Programmable
Load/Weather
Optimum
Start
Programmer/Timer
Room Thermostat
Compensation
Control
Time and Temperature Control to Hot Water
Cylinder Thermostat and Programmer/Timer
Combination Boiler
Heating Zone Valves
Fitted
Not Required
Hot Water Zone Valves
Fitted
Not Required
Thermostatic Radiator Valves
Fitted
Not Required
Automatic Bypass to System
Fitted
Not Required
Boiler Interlock
Provided
ALL SYSTEMS
The system has been flushed and cleaned in accordance with BS7593 and boiler manufacturer’s instructions
Yes
What system cleaner was used?
What inhibitor was used?
Quantity
litres
CENTRAL HEATING MODE
Measure and Record:
Gas Rate
m
3
/hr
OR
ft
3
/hr
Burner Operating Pressure (if applicable)
mbar
OR
Gas Inlet Pressure
mbar
Central Heating Flow Temperature
°C
Central Heating Return Temperature
°C
COMBINATION BOILERS ONLY
Is the installation in a hard water area (above 200ppm)?
Yes No
If yes, has a water scale reducer been fitted?
Yes
No
What type of scale reducer has been fitted?
DOMESTIC HOT WATER MODE Measure and Record:
Gas Rate
m
3
/hr
OR
ft
3
/hr
Burner Operating Pressure (at maximum rate)
mbar
OR
Gas Inlet Pressure (at maximum rate)
mbar
Cold Water Inlet Temperature
°C
Hot water has been checked at all outlets
Yes
Temperature
°C
Water Flow Rate
l/min
CONDENSING BOILERS ONLY
The condensate drain has been installed in accordance with the manufacturer’s instructions and/or BS5546/BS6798
Yes
ALL INSTALLATIONS
If required by the manufacturer, record the following
CO
2
% OR CO
ppm
OR CO/CO
2
Ratio
The heating and hot water system complies with the appropriate Building Regulations
Yes
The boiler and associated products have been installed and commissioned in accordance with the manufacturer’s instructions
Yes
The operation of the boiler and system controls have been demonstrated to and understood by the customer
Yes
The manufacturer’s literature, including Benchmark Checklist and Service Record, has been explained and left with the customer
Yes
*
All installations in England and Wales must be notified to Local Authority Building Control (LABC) either directly or through a Competent Persons Scheme.
A Building Regulations Compliance Certificate will then be issued to the customer.
©Heating and Hotwater Industry Council (HHIC)
www.centralheating.co.uk
Commissioning Engineer’s Signature
Customer’s Signature
(To confirm satisfactory demonstration and receipt of manufacturer’s literature)
This Commissioning Checklist is to be completed in full by the competent person who commissioned the boiler as a means of demonstrating
compliance with the appropriate Building Regulations and then handed to the customer to keep for future reference.
Failure to install and commission this equipment to the manufacturer’s instructions may invalidate the warranty but does not affect statutory rights.
Customer Name
Telephone Number
Address
Boiler Make and Model
Boiler Serial Number
Commissioned by
(print name)
CORGI ID Number
Company Name
Telephone Number
Company Address
Commissioning Date
To be completed by the customer on receipt of a Building Regulations Compliance Certificate
*
:
Building Regulations Notification Number
(if applicable)
48pp MANUAL SPREADS 19/10/10 08:36 Page 6