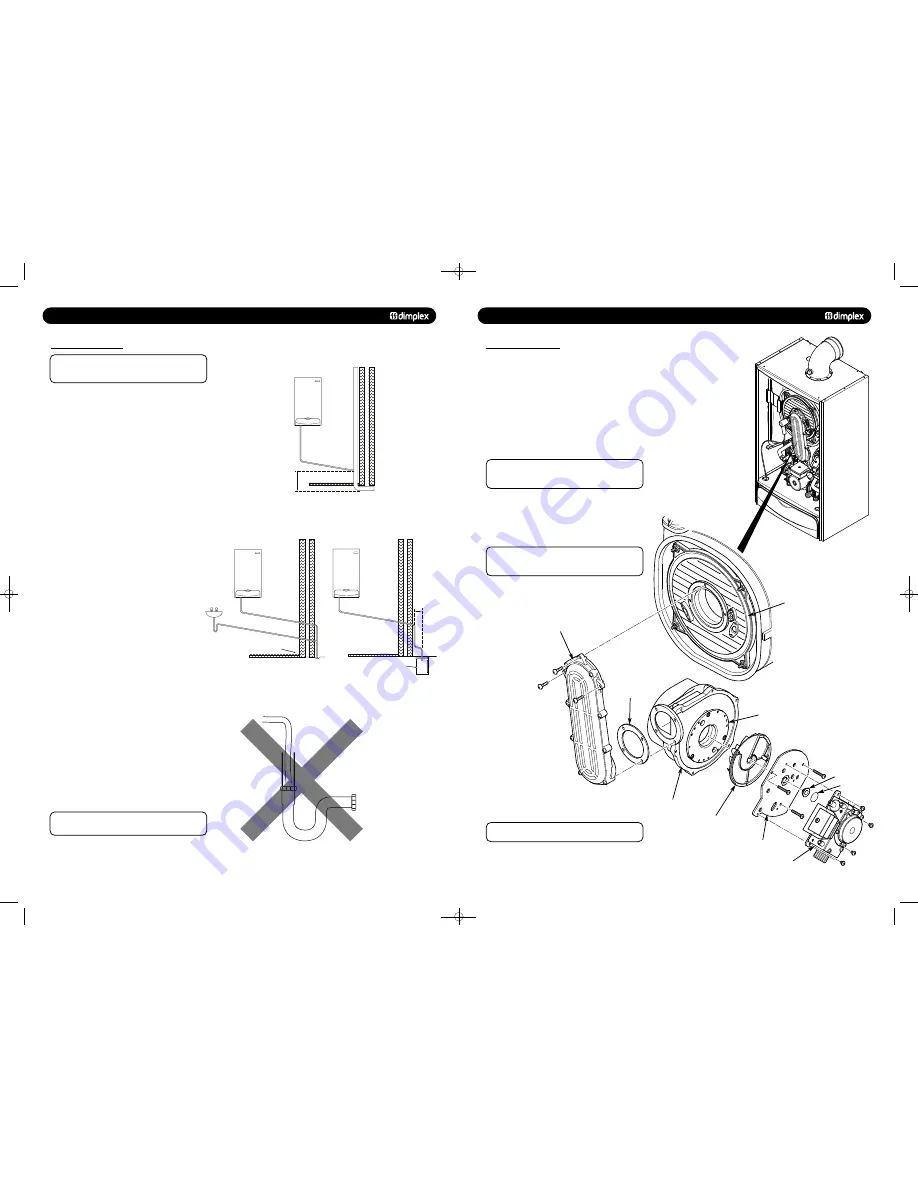
7.0
SITE REQUIREMENTS
7.6
CONDENSATE DRAIN
NOTE: The appliance is fitted with a trap the depth of
which is >= 75mm, therefore no other traps are required in
the condensate run.
The condensation discharge pipe must not rise at any point
along its length. There MUST be a fall of AT LEAST 2.5° (50mm
per metre) along the entire run.
1. The condensate outlet will accept 21.5mm (
3
/
4
in) plastic
overflow pipe which should discharge internally into the
household drainage system, downstream of all other traps. if
this is not possible, discharge into an outside drain is
acceptable.
2. Ensure the discharge of condensate complies with any
national or local regulations in force.
BS 6798:2000 & Part HI of the Building Regulations give
further guidance.
3. Metal pipework is NOT suitable for use in condensate
discharge systems.
4. The pipe should be a minimum of 21.5mm diameter and
must be supported properly.
5. IIt is advisable to keep the condensate pipe internal.
6. E
External runs greater than 3 metres or runs in cold areas
should use 32mm waste pipe.
7. If the boiler is fitted in an unheated location the entire
condensate discharge pipe should be treated as an external
run.
8. In all cases discharge pipe must be installed to aid disposal
of the condensate.
9. When discharging condensate into a soil stack or waste pipe
the effects of existing plumbing must be considered. If soil
pipes or waste pipes are subjected to internal pressure
fluctuations when WC’s are flushed or sinks emptied then
back-pressure may force water out of the boiler trap and
cause appliance lockout.
Examples are shown of the following methods of
terminations:-
i) to an internal soil & vent pipe
ii) via and internal discharge branch (e.g. sink waste)
iii) to a drain or gully
iv) to a purpose made soakaway
10. In exceptional circumstances, such as when a boiler is
installed in a basement without drainage, it may be necessary
to install a condensate pump to carry condensate up to ground/
drain level. Such products are available from most plumbing
merchants. For help with selecting a condensate pump contact
Dimplex Boilers - Tel: 0844 3711121.
WARNING: There must be no air breaks in the condensate
pipework or drainage system.
16
© Dimplex Boilers 2008
50mm per metre of pipe r
un
2.5° Minimum fall
450mm min
Termination to an internal soil and vent pipe
50mm per metre of pipe r
un
2.5° Minimum fall
External termination via internal discharge branch
e.g sink waste - downstream
Sink
Pipe must terminate
above water level but
below surrounding surface.
50mm per metre of pipe r
un
2.5° Minimum fall
Termination to a purpose made soak-away
Holes in the soak-away must
face away from the building
500mm min
NOT ALLOWED
There should be
no air gap
Fig. 14
Fig. 15
Fig. 17
Fig. 16
13.0
CHANGING COMPONENTS
13.3
GAS VALVE AND FAN
1. Disconnect the two leads to the fan and one lead to the gas
valve.
2. Undo the nut on the gas inlet pipe to the valve and retain
the sealing washer.
3. Remove the three securing screws holding the air/gas
Channel to the burner door plate and remove the valve and fan
assembly (Fig. 57).
4. Remove the three screws holding the valve and swirl plate
to the fan adaptor plate.
NOTE: Mark on the adaptor plate which holes are being
used by the screws. Using the wrong holes on
re-assembly will cause mis-alignment of the gas valve.
Fan Only
6. Remove the three screws holding the fan adaptor to the fan.
7. Remove the four screws securing the fan to the air/gas
channel. Reassemble in reverse order ensuring all seals are in
place.
NOTE: The gas valve throttle should be adjusted in
accordance with the instructions supplied in the spares kit
See Section 10.
© Dimplex Boilers 2008
33
NOTE: Dimplex Combi 38 will also be fitted with a black
plastic air cowl which encases the swirl plate.
Fig. 57
Swirl Plate
Fan
Fan Gasket
Burner Door
Air/Gas Channel
Fan Adaptor Plate
Injector Plate
Injector
Injector ‘O’ Ring
Gas Valve
48pp MANUAL SPREADS 19/10/10 08:36 Page 16