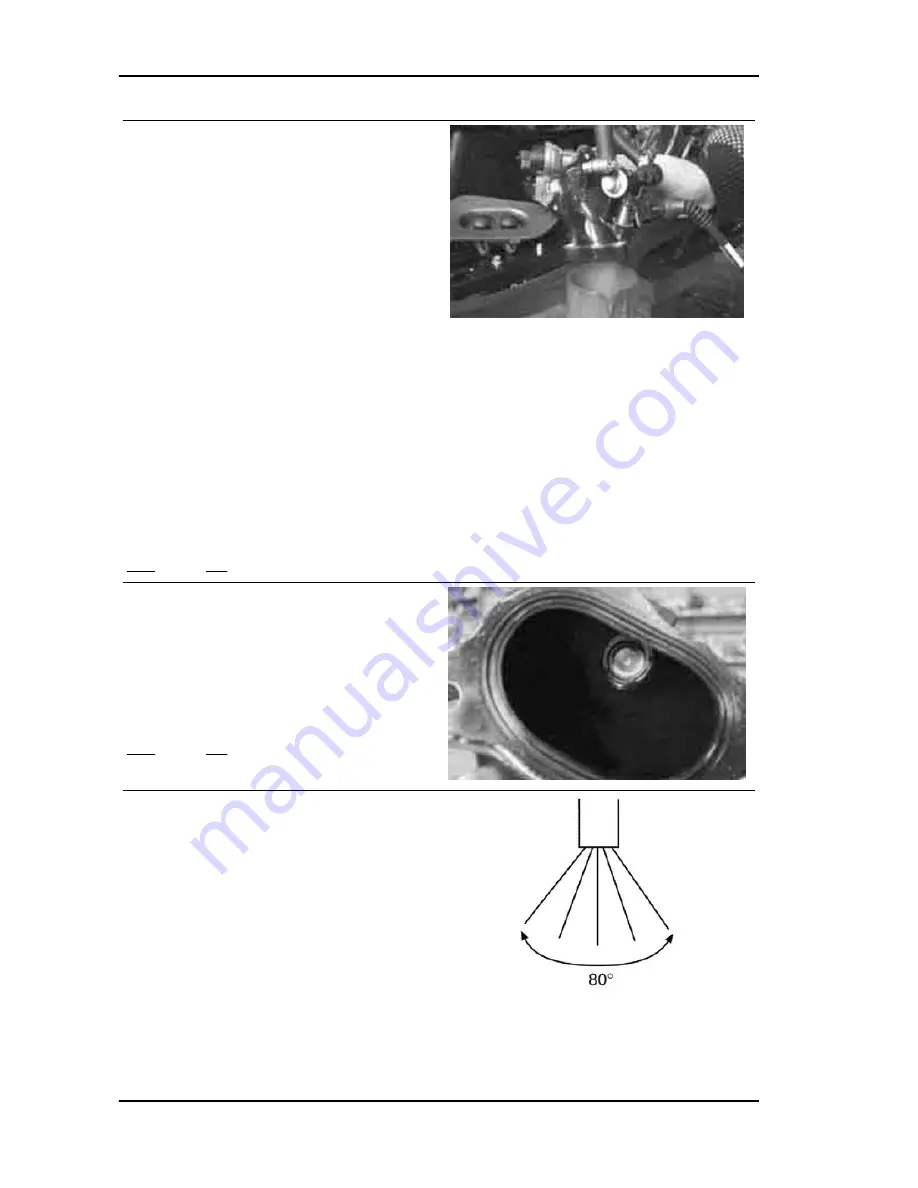
2
- Prepare a graduated container with minimum
capacity of 100 cm3 and a resolution of 10-20 cm3
Connect the injector to the wire supplied with the
injection tester. The wire is provided with alligator
clips for direct connection to the battery.
Prepare an auxiliary battery.
Set the switch to "
ON
" with switch to "
RUN
" and
stand raised.
Select the "active diagnosis" function.
Start the pump diagnosis.
During the first 30 seconds of pump diagnosis,
power the injector by the wire and the auxiliary
battery for 15 seconds.
Collect the fuel delivered by the injector into the
graduated container.
Power supply pressure = 300 kPa (3 BAR)
Quantity delivered = approx. 40 cm3
YES go to 3 NO go to 4
3
- Perform the injector sealing test.
Dry the injector outlet with a blast of compressed
air. Activate the fuel pump. Wait for one minute,
making sure there are no leaks coming from the
injector. Slight oozing is normal.
Value limit = 1 drop per minute
YES go to 5 NO go to 6
4
- Higher quantities are not expected.
For lower quantities, replace the injector (THER-
MAL GROUP AND TIMING SYSTEM).
5
- The injector is conforming.
6
- Repeat the test. If the fault continues, replace
the injector (THERMAL GROUP AND TIMING
SYSTEM)
The injector atomisation cannot be checked by
simple methods. The injector is provided with 5
holes whose angulation forms a jet with a taper of
Injection
Nexus 500 euro 3
INJEC - 238
Содержание 633721
Страница 1: ...WORKSHOP MANUAL 633721 633728 Nexus 500 euro 3 ...
Страница 4: ......
Страница 6: ...INDEX OF TOPICS CHARACTERISTICS CHAR ...
Страница 18: ...INDEX OF TOPICS TOOLING TOOL ...
Страница 30: ...INDEX OF TOPICS MAINTENANCE MAIN ...
Страница 43: ...INDEX OF TOPICS ELECTRICAL SYSTEM ELE SYS ...
Страница 78: ...INDEX OF TOPICS ENGINE FROM VEHICLE ENG VE ...
Страница 82: ...INDEX OF TOPICS ENGINE ENG ...
Страница 190: ...Oil pump cover screws 0 7 0 9 Engine Nexus 500 euro 3 ENG 190 ...
Страница 191: ...INDEX OF TOPICS INJECTION INJEC ...
Страница 289: ...INDEX OF TOPICS SUSPENSIONS SUSP ...
Страница 308: ...INDEX OF TOPICS BRAKING SYSTEM BRAK SYS ...
Страница 327: ...INDEX OF TOPICS COOLING SYSTEM COOL SYS ...
Страница 337: ...INDEX OF TOPICS CHASSIS CHAS ...
Страница 358: ...INDEX OF TOPICS PRE DELIVERY PRE DE ...
Страница 362: ...INDEX OF TOPICS TIME TIME ...
Страница 407: ...Technical Data Transmission 9 83 99 375 Turn indicators 54 Tyres 10 ...