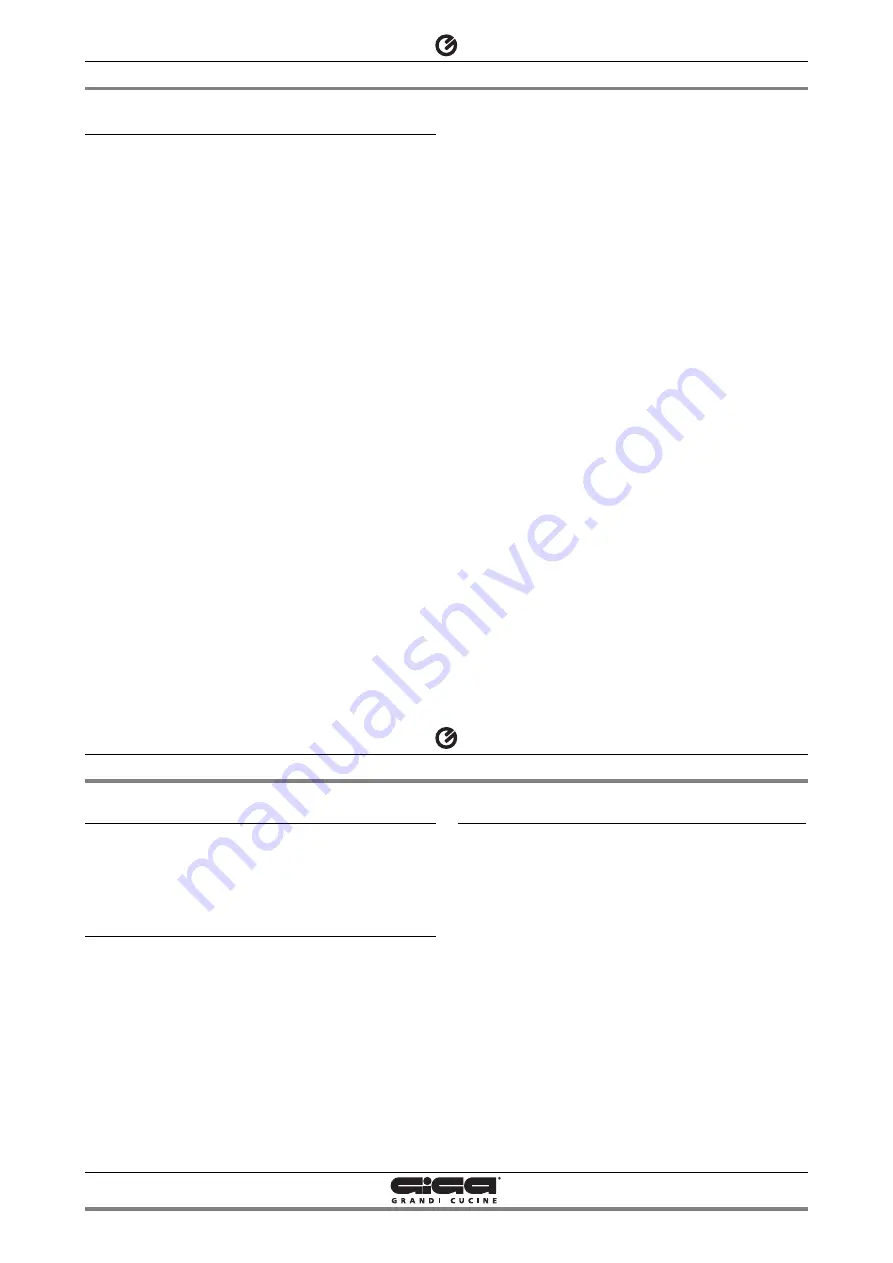
5.1 Preparation and Start-up
Before starting up the appliance, remove the protective wrapping.
Then carefully clean the working surface and the external parts with
lukewarm water and detergent, using a damp rag to remove all traces
of anti-rust material applied in the factory, then dry with a clean cloth.
5.1.1 Start-up
Before starting up the appliance, check that its specifications (cate-
gory and type of gas used) match those of the family and group of
the gas available locally.
If not, it is necessary to adapt the appliance to the gas family or
group required (see paragraph “Conversion and adjustment”).
To start up the appliance, see the instructions for regular use.
5.1.2 Check of power
The appliances must be used with the specific nozzles for the nomi-
nal power.
The power may be:
• the nominal power indicated on the data plate of the appliance;
• the reduced capacity power.
These nozzles are shown in table 1 “Technical data”.
Nominal power is also obtained in respect of the supply pressure:
• from 15 to 22.5 mbar for gases of the second family (G20/methane)
• from 25 to 45 mbar for gases of the 3rd family
(G30/butane, G31/propane)
The appliance shall not be operated outside the above-mentioned
pressure ranges.
To adjust power with reduced capacity, use the data in table 1.
If you wish to further check the nominal power, you may do so by
using a gas meter according to the so-called "volumetric method".
A simple inspection is usually enough to check if nozzles are func-
tioning correctly.
4 - INSTALLATION INSTRUCTIONS
5 - SET-UP FOR OPERATION
502_03
- GAS KITCHENS
7
· 16
4.4 Preparing for installation
The gas kitchens type INCASSO must be set on a regular worktable,
made of fireproof material and in compliance with the current
hygiene and safety standards.
It is of vital importance to observe the following instructions.
Kitchens units can go near other appliances such as a fryer, as long
as the required distance of 50 mm (min.) is kept.
In order to install the unit properly on the worktable, proceed as fol-
lows:
A: fig. 2)
Base: With a drill, make an opening in the worktable as
described in fig. 2.
The worktable and appliance are clamped with six M5 screws; first
drill the relevant holes in the worktable as described in fig. 2. In
order to prevent liquids from leaking in between the lining and the
appliance, it is necessary to waterproof the leaks with sanitary silico-
ne, anti-mould and heat resistant to at least 100°C (i.e. Pactan 6076).
The knob position is fixed; therefore, in the design of the parts
where the appliance will be fit into, the relevant panel will have to
be provided with a special hole (fig. 1).
B: fig. 3)
Housing: Make an opening in the worktable in order to fit
in the appliance as described in fig. 3 (the rise can be performed per-
fectly by means of a bent L-shaped metal support). The appliance is
clamped to the worktable with six M5 screws fit through holes pre-
viously drilled (fig. 3). Fit the appliance and fasten it to the workta-
ble with the screws. Fill the intermediate leak (about 3 mm wide)
with heat resistant (at least 100°C) anti-mould silicone (i.e. Pactan
6067) according to the current hygiene standards. The knob position
is fixed, hence the furniture structure where the appliance has to be
housed will have to be provided with matching holes (fig. 1).
C: fig. 4)
Base with anti-seepage edge: Make a frame on the stain-
less steel worktable as described in fig. 4. Fit the appliance and
fasten it with the parts supplied with it. The knob position is fixed;
hence the worktable structure will have to be provided with mat-
ching holes (fig. 1).
In order to prevent overheating of the furniture, it is important to
have air circulate inside the space near the machines. If the space
under the machine housing is accessible, a closing panel must be
put in to prevent accidental contact with hot walls and electric
wires. To this end, it is necessary to make holes at the back and pos-
sibly at the front as well, for a total of at least 40 cm² for the
models 400, 80 cm² for the models 800 and 120 cm² for the models
1200.
This panel must be made of fireproof material and applied at a
distance between 50 mm (min.) and 90 mm (max) from the bottom
of the machine, further, to ensure internal air circulation must be
provided with a hole 40 cm² / 80 cm² / 120 cm². Preferably at the
front (fig. 2/3/4).
Panels and/or inflammable parts must be at a distance of at least
300 mm from the hot walls of the machine.