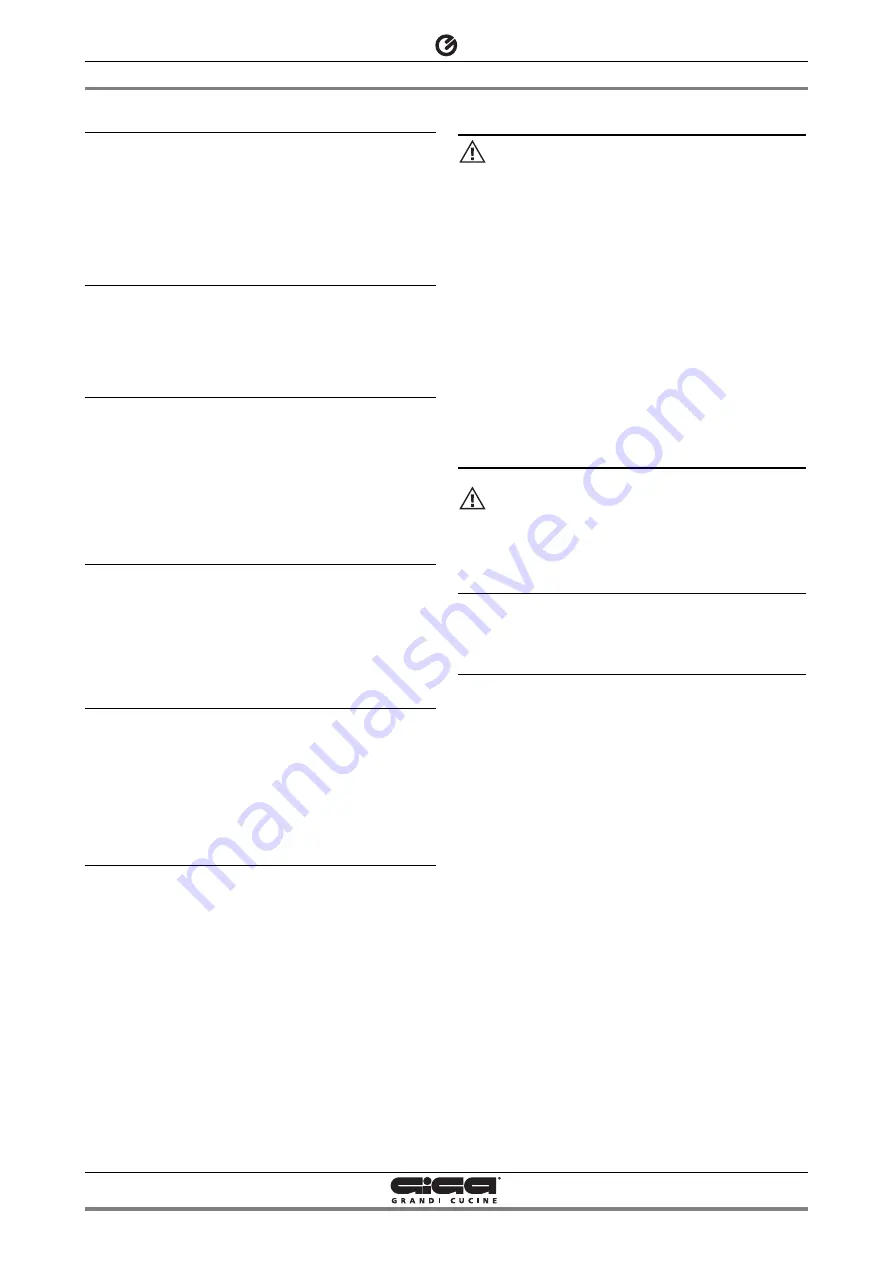
5 - SET-UP FOR OPERATION
502_03
- GAS KITCHENS
12
· 16
5.1.8 Operation Control
• Start the appliance in accordance with the instructions;
• Check that the appliance does not have any leaks by using a leak-
detecting spray.
• Check ignition and that flame on the main burner lights properly
and is correctly formed, even on low.
• Check that the pilot flames work properly.
• A servicing and maintenance contract is recommended.
5.1.9 Operator training
• Explain and show the user how the machine works according to
the instructions, and hand him this manual.
• Remind the user that any structural alterations or any building
modification or renovation may affect the combustion air supply,
thus requiring a second operation check.
5.1.10 Conversion and adjustment
To change over form one kind of gas to another, for example from
methane to liquid gas, or to another type of gas, the use of suitable
nozzles for the main burner is required, in accordance with the table
"TECHNICAL DATA".
The nozzles of the main burners and pilot for different types of gas,
marked with the relative diameter in hundredths of mm, are in an
envelope which is provided with the appliance. After transforma-
tion or adaptation, carry out operating checks as described in para-
graph 5.1.8, "Operation control."
5.1.11 Replacing burner nozzles (fig. 5)
To replace the nozzle (1): remove the grill, the burner cover, the
burner body and the tray of the top.
Then unscrew the screws (2) which fasten the primary air bushing
and replace the nozzle (1). See the table "TECHNICAL DATA".
Once the suitable nozzle has been installed, adjust the distance of
the primary air and fasten the bushing with the appropriate screw.
See the table "TECHNICAL DATA".
5.1.12 Setting reduced capacity power (fig. 5)
The minimum setting screw (5) should be adjusted as follows:
• for operation with LPG it should be screwed all the way down;
• for operation with methane, use the gas flow table to check the
value in l/min with respect to the operating alorific value (meas-
urement in accordance with the volumetric method). Start the
appliance in accordance with the instructions. Turn the knob to
the minimum position and use screw (5) to adjust the flow (clock-
wise = flow reduction; conter-clockwise = flow increase).
5.1.13 Replacement of pilot nozzle, open flames (fig. 5)
Remove the grill, the flame separator and the pilot body. Loosen the
screw that holds the pilot to the burner and lift it to a more conven-
ient position. Loosen the nut (11) and extract the bicone (13) and
the injector (12). Replace the injector. See the table "TECHNICAL
DATA" and re-assemble, performing the steps in reverse order.
5.2 Maintenance
Attention! Before doing any repair or maintenance
work, unplug the appliance.
The following maintenance program should be carried out at least
once a year:
• Check that all the safety and adjustment devices are working
properly;
• Check that the burners are working properly with regard to:
- ignition
- combustion safety;
Check functioning of the appliance as described in paragraph
"Operation Control";
If it should be necessary to clean the open flame burners, proceed
as follows:
• Clean the grills, covers and bodies of the burners;
• Clean the parts with water and detergent and an appropriate
tool. Rinse and dry.
When reassembling the parts, make sure you place them back in the
right position.
5.3 Replacing parts
All parts must be replaced by authorized technicians
only!
To replace the following parts first remove all the control knobs and
control panel (after loosening the fixing screws), then extract the
ignition wire.
5.3.1 Open flame gas valve (fig. 5 - pos. 4)
Loosen the fitting of the pipes (6) and (9) of the gas and of the
thermocouple (8), loosen the fitting (7) for the fastening of the
valve on the ramp and replace the piece.
5.3.2 Open flame thermocouple (fig. 5 - pos. 14)
Loosen the nut (8) for fastening the thermocouple on the valve and
on the burner (17) and replace the piece (14).