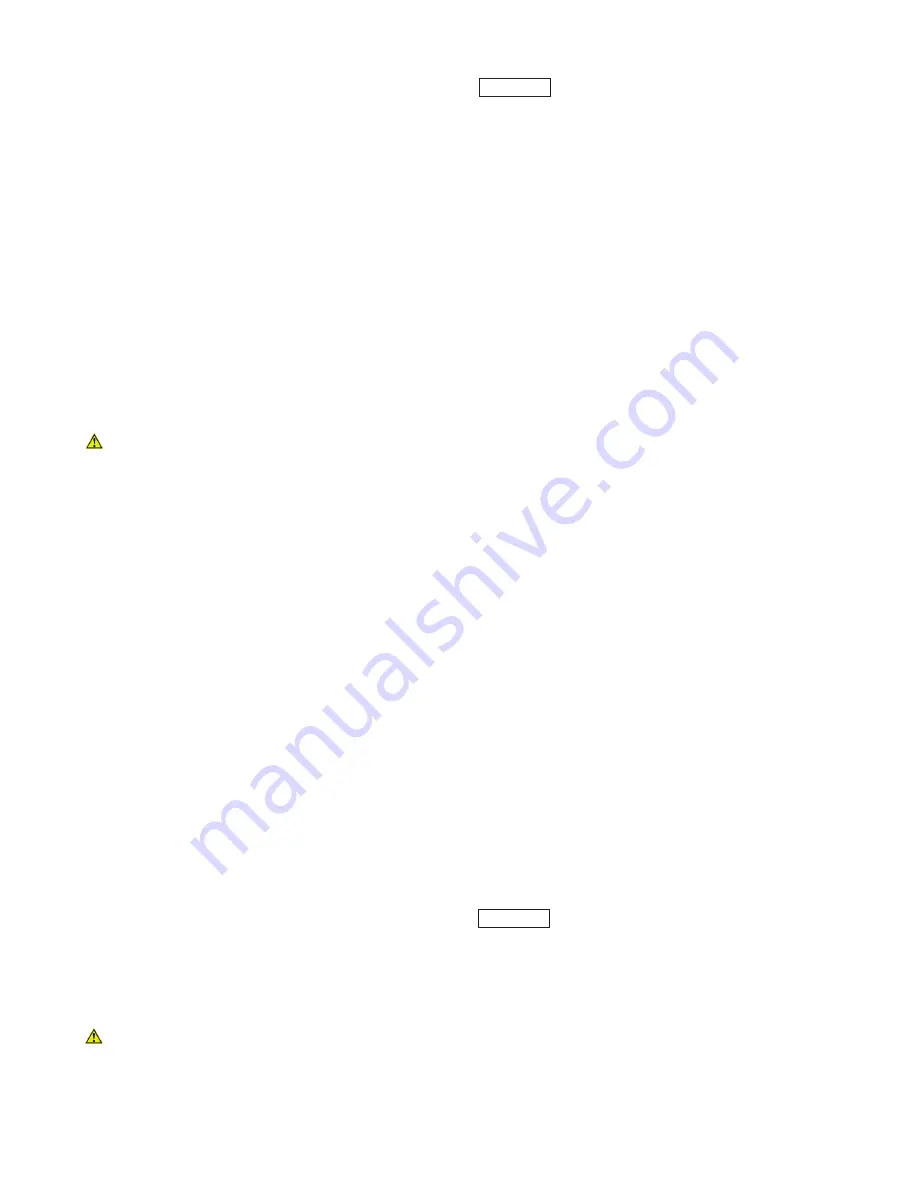
2
INSTALLATION INSTRUCTIONS
Required NPSH refers to water: Specific weight 62.4 lb/
ft
3
(1kg/dm
3
) at maximum permissible revolutions.
Operation and Maintenance
Check oil level prior to starting and ensure trouble-free wa-
ter supply. Oil: Use only 23.7 ounces (0.7 litres) of Giant Oil
(p/n 01154) or ISO VG 220 GL4 (e.g. Aral Degol BG220) or
SAE 90 GL4 gear oil.
Initial change after 50 operating hours and then every 500
operating hours. In either case change oil every 6 months
operation.
Caution!
When operating in damp places or with high
temperature fluctuations.
Oil must be changed immediately, should condensate
(frothy oil) occur in the gear box.
Keep NPSH under control.
Max. input pressure 145 PSI (10 bar), maximum suction
head -4.35 (-0.3 bar).
Safety Rules
Pump operation without safety valve as well as any ex-
cess in temperature or speed limits automatically voids the
warranty. The safety valve must be regulated in accor-
dance with the guidelines for liquid spraying units so that
the admissible operating pressure can not be exceeded by
more than 10%.
When the pump is in operation, the open shaft end must
be covered up by shaft protector (17), the driven shaft side
and coupling by a contact protector.
Pressure in discharge line and in pump must be at zero
before any maintenance to the pump takes place. Close
up suction line. Disconnect fuses to ensure that the driving
motor does not get switched on accidently.
Make sure that all parts on the pressure side of the unit are
vented and refilled, with pressure at zero, before starting
the pump.
In order to prevent air, or an air/water-mixture being
absorbed and to prevent cavitation occurring, the pump-
NPSHR, positive suction head and water temperature must
be kept under control.
Cavitation and/or compression of gases lead to uncon-
trollable pressure-kicks which can ruin pump and unit
parts and also be dangerous to the operator or anyone
standing nearby.
Giant Plunger Pumps are suitable for pumping clean water
and other non-agressive or abrasive media with a specific
weight similar to water.
Before pumping other liquids - especially inflammable,
explosive and toxic media - the pump manufacturer
must under all circumstances be consulted with
regard to the resistance of the pump material. It is the
responsibility of the equipment manufacture and/or
operator to ensure that all pertinent safety regulations
are adhered to.
Please read operating instructions carefully before
putting the pump into operation!
Important!
Do not use grease when renewing the high
pressure plunger seal (pos. 50).
Hot water causes grease to wash off the seal which in turn
can jam valves!
The new seals should only be oiled lightly before installa-
tion.
These operating instructions supplement the general oper-
ating instructions for the SP series pumps.
Plant Lay-Out
For perfect functioning of the pump, the following points
must be adhered to.
A) Pressure in Suction Side
The stipulated NPSHR is the minimum required pressure
above the vapor pressure of the medium and is never to
fall short of this figure. Temperature and vapor pressure of
the medium, the geodetical height of the location, the flow
rate and loss of friction in the suction line, must all be taken
into consideration.
B) Pulsation
Due to its construction, the plunger pump creates pulsa-
tion in the suction and discharge lines. Suction pulsation in
particular must be dampened in order to prevent resonance
in the suction line which in turn, causes cavitation. There-
fore, the pump is never to be connected by a rigid pipe but
rather by a flexible hose (not reinforced by steel), and if
possible 1.5 to 2 times wider than the suction connection. If
a booster pump is used attach a hose between the booster
pump and the high pressure pump.
If several pumps are used, each pump must have its own
suction line. If this can’t be done, a suction air chamber or
a suction flow stabilizer must be installed in front of each
pump. The bladder in the stabilizer is to be pre tensioned
on location.
Depending on the lay-out of the plant, a pressure accumu-
lator may be necessary on the discharge side. This pres-
sure accumulator must be installed right behind the dis-
charge outlet of the high pressure pump. We recommend
the use of only one pressure accumulator in the discharge
line in order to avoid irritation which could be caused by
different pre-tension levels in the accumulators.
Gas-tension in both the suction flow stabilizer and in the
pressure accumulator are to be checked regularly.
Maintenance
Important!
To lubricate the high pressure seals, the inter-
mediate casing (48) is filled with high-temperature resistant
grease at our works. This means the holes in the valve
casing have to be closed with thread plugs (29A) - to be
tightened with Loctite 572.
Содержание SP100HT
Страница 4: ...4 SP100HT EXPLODED VIEW ...