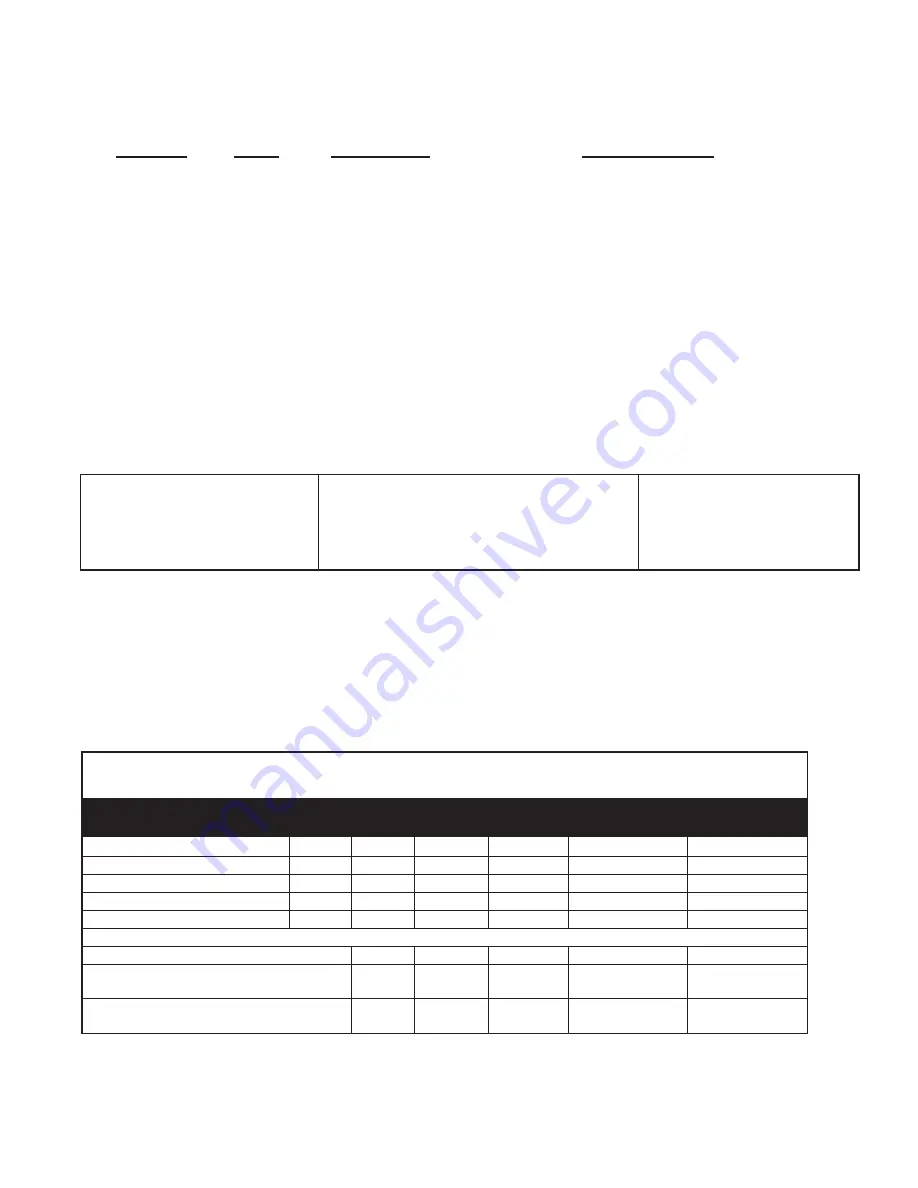
7
Preventative Maintenance Check-List & Recommended Spare Parts List
Check
Daily Weekly 50hrs
Every
Every
Every
500 hrs 1500 hrs
3000 hrs
Oil Level/Quality
X
Oil Leaks
X
Water Leaks
X
Belts, Pulley
X
Plumbing
X
Recommended Spare Parts
Oil Change p/n 1154
X
X
Plunger Packing Kits (1 kit/pump)
X
(See page 5 for kit list)
Valve Assembly Kit (1 kit/pump)
X
(See page 5 for kit list)
Position
Part#
Description
Torque Amount
7
07186
Oil Sight Glass
106 in.lbs. (12 Nm)
9
01010
Screw
221 in.-lbs. (25 Nm)
11
07109
Oil Drain Plug
29 ft.-lbs. (40 Nm)
16
07114
Inner Hexagon Screw
132 in.-lbs. (15 Nm)
20A
07311
Inner Hexagon Screw
22 ft.-lbs. (30 Nm)
24B
08399
Tension Screw
247 in.-lbs. (28 Nm)
41
07331
Plug, Inlet
51 ft.-lbs. (70 Nm)
43
07213
Plug, Discharge
51 ft.-lbs. (70 Nm)
46
07158
Nut, Stud Bolt
59 ft.-lbs. (80 Nm)
SP100HT/SP200HT TORQUE SPECIFICATIONS
Pump Mounting Selection Guide
Bushings
07175
- 28 mm Tapered H Bush
-
ing
Rails
07358
- Plated Steel Channel
Rails
(L=9.18” x W=1.88” x H=3.00”)
Pulley & Sheaves
01055
- 9.75” Cast Iron 2 gr. - AB Section
01062
- 7.75” Cast Iron - 2 gr. - AB Section
Содержание SP100HT
Страница 4: ...4 SP100HT EXPLODED VIEW ...