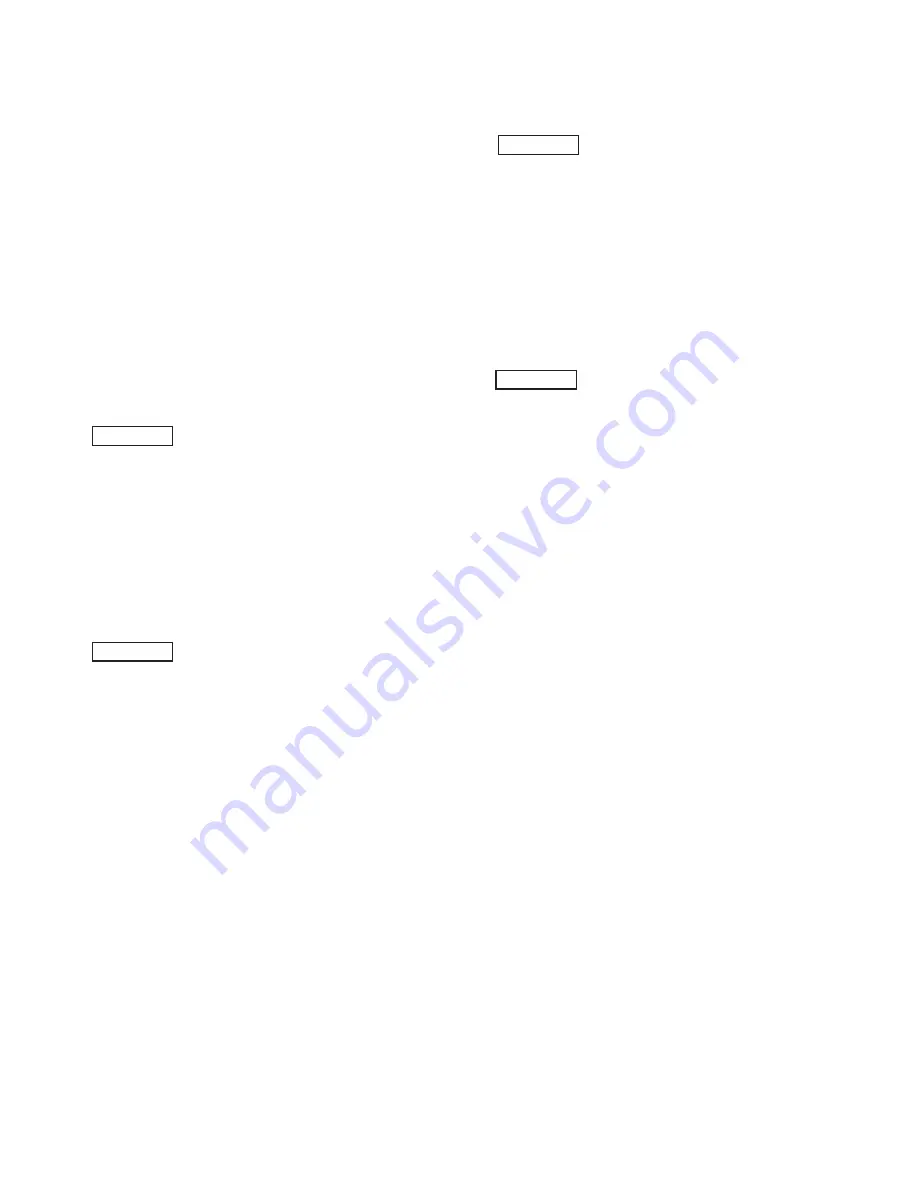
2
INSTALLATION INSTRUCTIONS
Cooling the Gear Oil
Important!
The water input pressure must not
exceed 2 bar when using the integrated system for
cooling the gear oil (standard version).
If a separate cooling circuit (maximum 29 PSI [2
bar]) is installed, it is then possible to have an input
pressure of up to maximum 145 PSI (10 bar) on the
suction side.
Make sure that suction pulsation is sufficiently
dampened - water column resonance must be
avoided.
Important!
The pumps can be run without gear
oil cooling in continuous operation
up to
a power
rating of
107 hp (80 kW)
or with major intermittent
operation).
If operation power
exceeds 107 hp (80 kW)
or if
continuous operation is the case, the pump must
be run with the integrated oil cooling system. The
maximum temperature of the water being pumped
and which is also fed through the cooling system
must not exceed 86 °F (30°C). The amount which
is fed into the cooling system depends on the pump
speed and is approximately 1.85 GPM (7.0 L/min) at
580 RPM. The cooling water is sucked in by one of
the pumping chambers and pumped away.
The stated figures are for maximum pressure and
maximum speed (RPM) and apply for interval
operation with cold water.
Required NPSH refers to water (specific weight 1kg/
dm
3
, viscosity 1°E) at maximum permissible pump
revolutions.
Fluid medium: Clean water filter with 50µm.
Operation and Maintenance
Check oil level prior to starting and ensure trouble-
free water supply.
Important!
If there is a
danger of frost
, the water
in the pump and in the pump fittings (particularly
the unloader valve) must be emptied. The second
discharge port can also be used and the pump run
“dry” for 1-2 minutes for this purpose.
Oil: Use only 3.3 Gallons (12.5 liters) of ISO VG 220
GL4 (e.g. Aral Degol BG220) or SAE 90 GL4 gear oil
(Giant p/n 01154). Initial change after 50 operating
hours and then every 1000 operating hours after one
year at the latest.
Important!
When operating in damp places or with
high temperature fluctuations, oil must be changed
immediately should condensate (frothy oil) occur in
the gear box.
NPSH values must be observed.
Содержание GP8055-Brine
Страница 6: ...6 Exploded View GP8055 GP8060 GP8065 Brine...