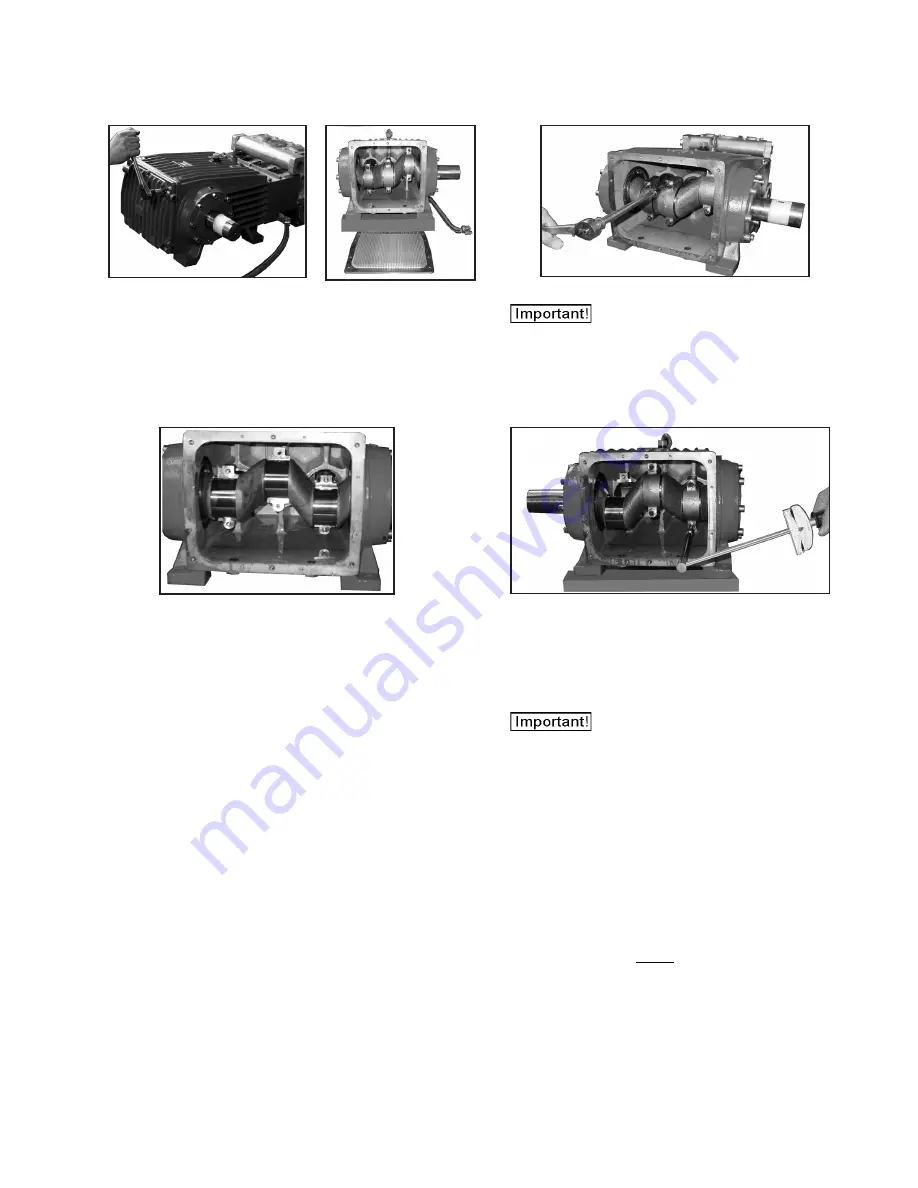
Pump Repair Instructions - GP8055/GP8060/GP8065 - Brine
12) Remove the connecting rod screws (24).
Connecting rods are marked 1 to
3 for identification. Do not twist connecting rod
halves or interchange them. When reassembling,
the connecting rod must be fitted in their exact
original position on the crankshaft journals.
13) Push connecting rod halves together with the
crosshead as far as possible into the crosshead guide.
Take out bearing cover (14/14A) and push out crank-
shaft taking particular care that the con rod doesn’t
get bent. Check surfaces on the connecting rods (24),
crankshaft (22) and crossheads (25). Check the sur-
faces of the crosshead guides in the crankcase for any
unevenness.
15) Mount bearing cover (14A) and tighten screws (17) to 64 Ft-lbs. Adjust axial play (clearance) on the
crankshaft to minimum 0.1 mm / max. 0.15 mm using shims (21A/21B). The shaft should turn easily with little
clearance. Connecting rod must sit exactly in the middle of each crank pin. Fit the bearing cover (14) and
tighten the screws (17) at 64 Ft-lbs. Seal (32A) must always be installed so that the seal lip on the inside
diameter faces the oil. Possible axial float of the seal adaptor (33) to be compensated with shims (33C).
Mount cooling plate (K1) and gear cover (K3) with their respective seals (K2). When assembling the cooling
circuit line, make sure that the oil cooler connection (K7) is always joined to the
upper
connection (K3) of the
gear cover.
14) Reassemble in reverse order. Thread the
long end of the crankshaft together with the inner
bearing rings into the crankcase; then mount
outer bearing ring (20) and spacer ring (22A).
Mount connecting rod halves in their exact origi
-
nal position and tighten at 37 Ft-lbs.
Connecting rods must be able to
move slightly sideways on the stroke journals.
To Dismantle Crankcase Gear
11)
Take out plungers and seal sleeves as described
above. Drain the oil by taking off the plug (12). After
removing the clip ring (33B), lever out the seal retainer
(33) with a screwdriver. Open hose adaptor (K11) and
remove gear cover (K3).
Remove the cooling vane
plate (K1) by removing the screws (K4)
11
Содержание GP8055-Brine
Страница 6: ...6 Exploded View GP8055 GP8060 GP8065 Brine...