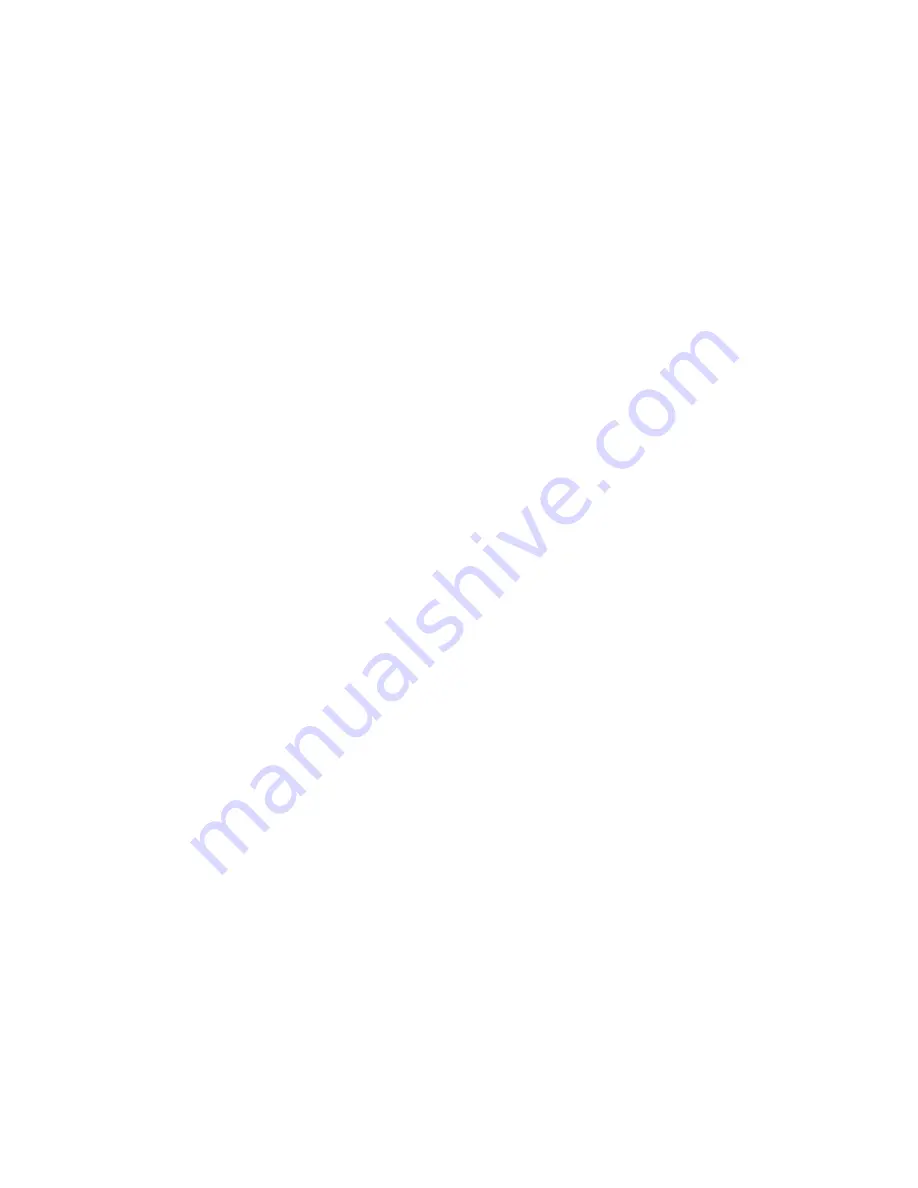
2
INSTALLATION INSTRUCTIONS
Operation and Maintenance
Check oil level prior to starting and ensure
trouble-free water supply.
Important!
If there is a danger of frost, the wa-
ter in the pump and in the pump fittings (particu
-
larly the unloader valve) must be emptied. The
second discharge port can also be used and the
pump run “dry” for 1-2 minutes for this purpose.
Oil: Use only 1.2 gal. (4.6 L) SAE 80W-90 In
-
dustrial Gear Lube Oil.
Before putting the pump into operation for
the first time, and every time the suction line
is emptied, the plugs (37) must be removed
and the pump cranked manually or started
briefly until water emerges out of the plug
bores. This procedure serves to vent the
drip-return so that the low-pressure seals
(32) do not run dry.
Thereafter the plugs (34) must be screwed back
on and tightened.
Initial oil changed after 50 operating hourse and
then every 1000 operating hours, or after 1 year
if used less.
Caution when operating in damp places or with
high temperature fluctuations. Oil must be
changed immediately should condensate (frothy
oil) occur in the gear box.
NPSH values must be respected.
Max. input pressure 145 PSI (10 bar), max.
suction head -4.35 PSI (-0.3) bar. Make sure
that suction pulsation is sufficiently dampened -
water column resonance must be avoided.
Safety Rules
A safety valve is to be installed in accordance
with the guidelines for liquid spraying units so
that the admissible operating pressure cannot
be exceeded by more than 10%.
Pump operation without a safety valve as well
as any excess in temperature or speed limits
automatically voids the warranty.
When the pump is in operation, the shaft end
must be covered by shaft protector (21) and the
driven shaft side and coupling by a protective
cover.
Pressure in the discharge line and in the pump
must be at zero before any maintenance to the
pump takes place. Close off suction line.
Take necessary precautions to ensure that the
driving motor cannot get switched on accidently
(by disconnecting the fuses, for example).
Make sure that the pump and all parts on the
pressure side of the unit are vented and refilled,
with pressure at zero, before starting the pump.
In order to prevent air, or an air/water mixture
being absorbed and to prevent cavitation oc-
curring, the pump positive suction head (npshr)
and water temperature must be respected.
Cavitation and/or compression of gases lead
to uncontrollable pressure spikes which can
ruin pump and unit parts and also be dan-
gerous to the operator and anyone standing
nearby.
Giant plunger pumps are suitable for pump-
ing clean water and other non-aggressive or
abrasive media with a specific weight simi
-
lar to water. Before pumping other liquids
- especially flammable, explosive and toxic
media - Giant must be consulted with regard
to the resistance of the pump material. It is
the reposnsibility of the equimpment manu
-
facturer and/or operator to ensure that all
pertinent safety regualtions are adhered to.
Содержание GP5122
Страница 4: ...4 EXPLODED VIEW GP5120 GP5122 GP5124 PUMPS...