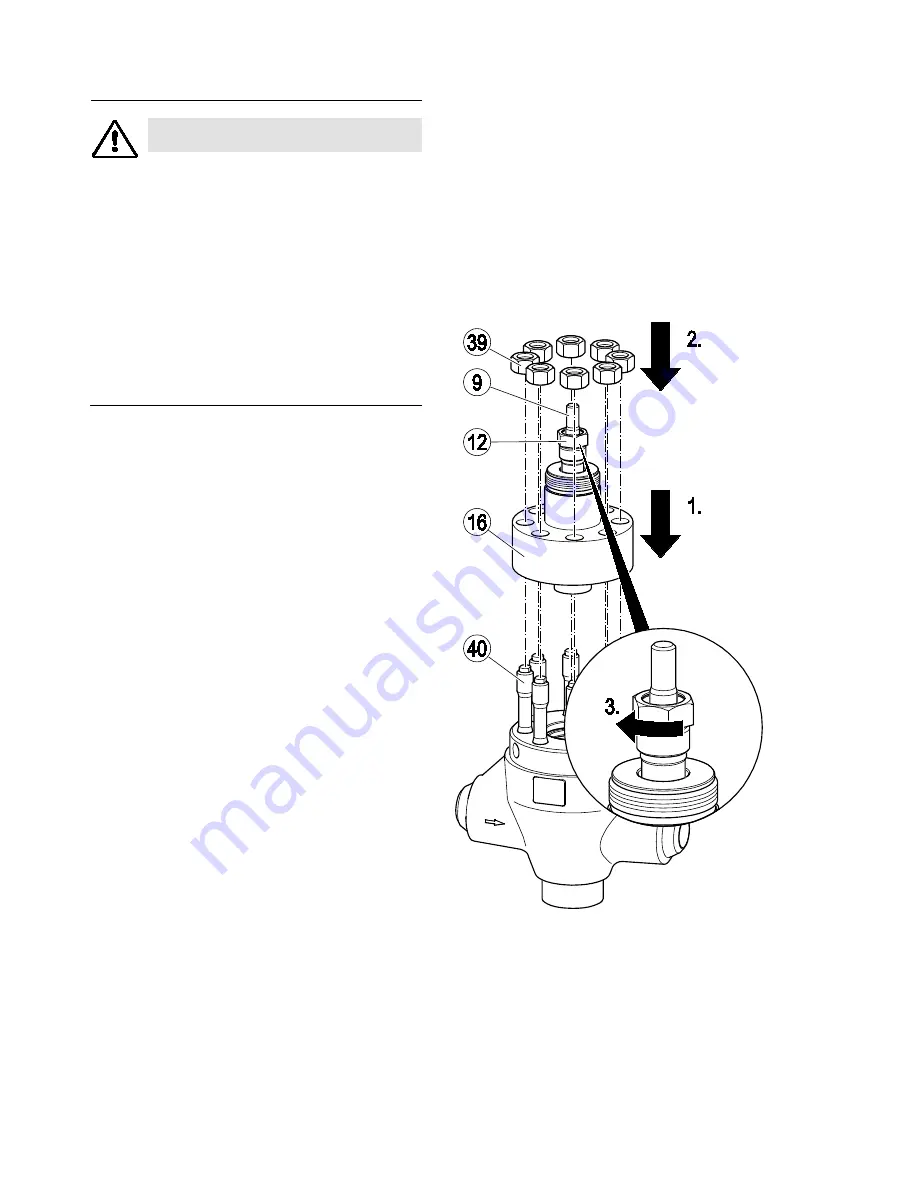
44
Fitting the upper part
DANGER
Risk of bruises if the equipment or
component parts fall down.
Use suitable lifting gear when moving
or lifting the equipment and/or
component parts.
Make sure that the equipment cannot
topple over.
Make sure that nobody is standing
below the lifted equipment.
Mount the stem and plug.
Mount the stuffing-box packing.
Make sure that the screwed union (12) is
slightly slackened.
Slowly pull the stem (9) upwards until it hits the
stop and hold the stem in this position.
Put the upper part (16) with the stem onto the
stud bolts (40) in the body (1.).
When inserting the stem with plug in the insert,
ensure that it is not canted and that it does not hit
any part.
Screw the hexagon nuts (39) on and tighten
them until they are handtight (2.).
Tighten the hexagon nuts in diagonally opposite
pairs to a torque of 300 Nm.
Tighten the screwed union (12) (3.).
The torque required for tightening the screwed
union depends on the condition of the stuffing-box
packing. Tighten the screwed union until the
following requirements are met:
The stuffing box must not leak.
The movement of the stem must not be
impaired by the stuffing box.
If it is not possible to meet both requirements
you have to replace the stuffing-box packing.
Содержание ZK 313
Страница 1: ...Control Valve ZK 313 Original Installation Instructions 818542 04 ...
Страница 55: ...55 Fluid flowrate and differential pressure Flowrates cold water A Differential pressure B Flowrate ...
Страница 56: ...56 KVS value CV value 1 1 1 2 2 1 5 1 7 3 2 3 2 7 4 3 6 4 2 5 5 5 6 4 6 8 9 4 7 11 12 7 8 13 15 0 9 20 23 1 ...
Страница 59: ...59 ...