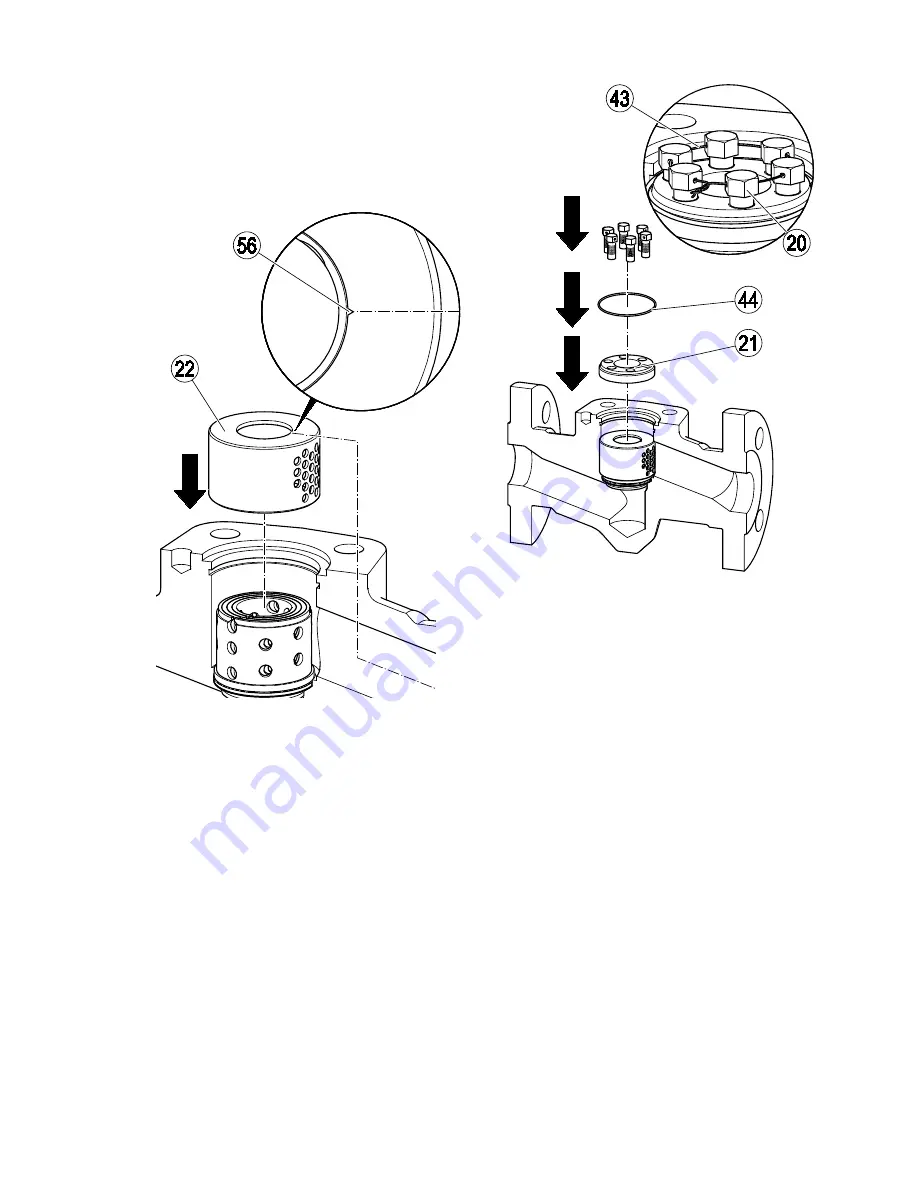
43
Mounting internals of equipment size DN 50
Put the protective sleeve against wear (22) onto
the sleeve insert and make sure that the
marking notch (56) is centrally aligned and
points towards the outlet.
Put the thrust ring (21) into the body.
Insert the retaining ring (44) into the body.
Apply lubricant to the hexagon-head cap screws
(20).
Screw the hexagon-head cap screws into the
thrust ring.
Tighten the hexagon-head cap screws with a
torque of 40 Nm.
Secure the hexagon-head cap screws with the
locking wire (43).
Содержание ZK 29
Страница 1: ...Control Valve ZK 29 Original Installation Instructions 810685 05 ...
Страница 10: ...10 The yoke is fitted with the following items No Designation 8 Spindle 9 Scale marking indicator 10 Scale ...
Страница 58: ...58 ...
Страница 59: ...59 ...