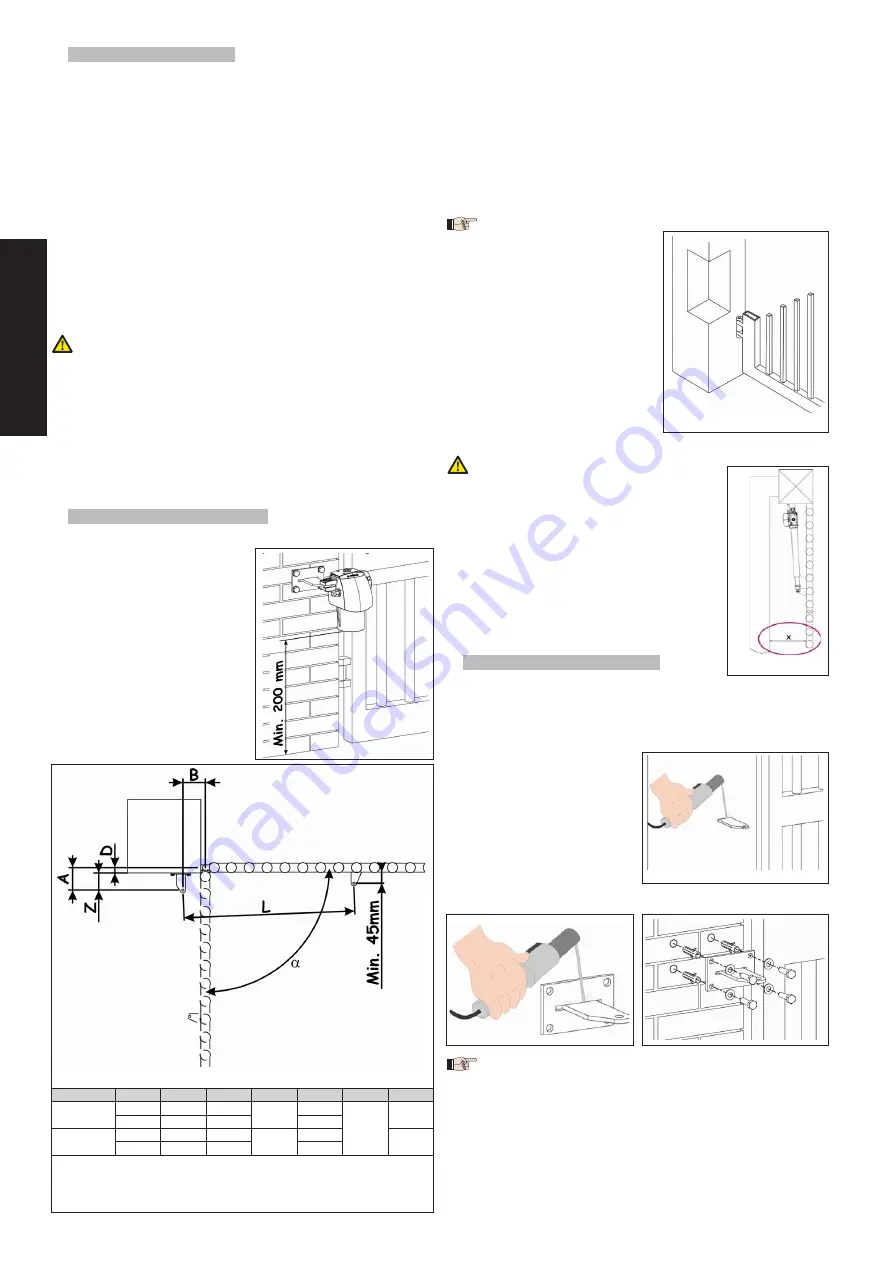
8
ENGLISH
2.2. PRELIMINARY CHECKS
To ensure a correctly operating automated system, the structure
of the existing gate or gate to be built must satisfy the following
requirements:
The construction elements of the gate must comply with the
provisions of the EN12604 and EN 12605 standards.
Leaf dimensions must not exceed the values indicated in pa-
ragraph 1.1.
The travel limit mechanical stops, for both opening and closing,
must be installed.
The structure of the leaves must be sufficiently rigid and sturdy,
suitable for the automated system.
Leaf movement must be smooth and free of any jamming during
the entire travel.
Adequately sturdy hinges, in good condition
Check the possibility of fastening the operator, respecting the
installation dimensions – see paragraph 2.3.
Check if an efficient earth plate is present for electrical connec-
tion to the operator.
Do not use the operator to move safety exits or gates installed
on emergency routes (see escape routes).
If a pedestrians door is built into the leaf due to be motorised,
you must add a safety switch on the door, connected to
the stop input, in order to prevent the automated system
working while the door is open.
The condition of the gate structure directly influences the safety
and reliability of the automated system.
We advise you to carry out the metalwork jobs if any, before
installing the operator.
2.3. INSTALLATION DIMENSIONS
Determine the installation position of the operator by referring to
figure 4, where the minimum off-
ground height is specified.
To determine the operator instal-
lation dimensions, consult figure 5
and the relevant table.
Fig. 5
Version
a
A
B
C
a
D
b
Z
c
L
300
90°
145
145
300
100
45
930
110°
125
125
80
400
90°
195
195
400
150
1110
110°
165
165
120
a
Useful rod stroke
b
maximum dimension
c
minimum dimension
•
•
•
•
•
•
•
•
2.3.1. g
eneRal
Rules
foR
deteRmining
the
installation
dimensions
.
To obtain
90°
opening of the leaf:
A+B=C
.
To obtain leaf opening
greater than 90°: A+B<C
.
Lower dimensions
A
and
B
cause greater leaf peripheral
speed.
Limit the difference between dimension
A
and dimension
B
within 4 centimetres; higher differences cause considerable
leaf peripheral speed variations during closing and opening
movements.
Maintain a
Z
dimension ensuring that the operator does not
impact the pilaster, while the leaf is closed.
If the dimensions of the pilaster or the position of the hinge
do not allow the operator to
be installed, to respect the
determined dimension
A
, a
niche must be created on the
pilaster as shown in figure 6.
The dimensions of the niche
must allow smooth installation
of the motor, not limit motor
rotation and not obstruct mo-
tor release operations.
When the operator has been installed, check if dimension “X”
in Fig. 7 is at the minimum of 500 mm. If
dimension “X” is less than 500 mm, run an
impact test on the point indicated in Fig.7,
as described in standard UNI EN 2445,
and make sure that the measured values
conform to the specifications of standard
UNI EN 2453.
If the thrust values are not within the values
specified in standard UNI EN 2453, the
zone indicated in figure 7 MUST BE pro-
tected with a protective device confor-
ming to the UNI EN 2978 standard.
2.4. INSTALLING THE OPERATOR
Fit the rear bracket in the position you have
just determined. If necessary, the length of the rear bracket
can be modified in order to respect the installation dimensions
(Z dimension included).
For iron pilasters, weld the bracket directly on the pilaster (Fig.
8).
For masonry pilasters, an ap-
propriate plate (available
as a optional item) must be
used for scew fastening.
Weld the rear bracket to
the plate and screw it
on, inserting it in the slot
(Fig. 9).
Secure all the items on the
pilaster using adequate securing systems (Fig. 10).
Fig. 9
Fig. 10
During the operations to secure the rear bracket, use a level
to check if the bracket is perfectly horizontal.
1.
2.
3.
4.
5.
1.
a–
b–
i–
ii–
Fig. 4
Fig. 4
Fig. 6
Fig. 6
Fig. 7
Fig. 7
Fig. 8
Fig. 8
Содержание G-BAT
Страница 1: ...g bat ENV...
Страница 28: ...NOTE NOTES NOTE NOTAS ANMERKUNG OPMERKINGEN...
Страница 29: ...NOTE NOTES NOTE NOTAS ANMERKUNG OPMERKINGEN...
Страница 45: ...NOTE NOTES NOTE NOTAS ANMERKUNG OPMERKINGEN...
Страница 46: ...NOTE NOTES NOTE NOTAS ANMERKUNG OPMERKINGEN...