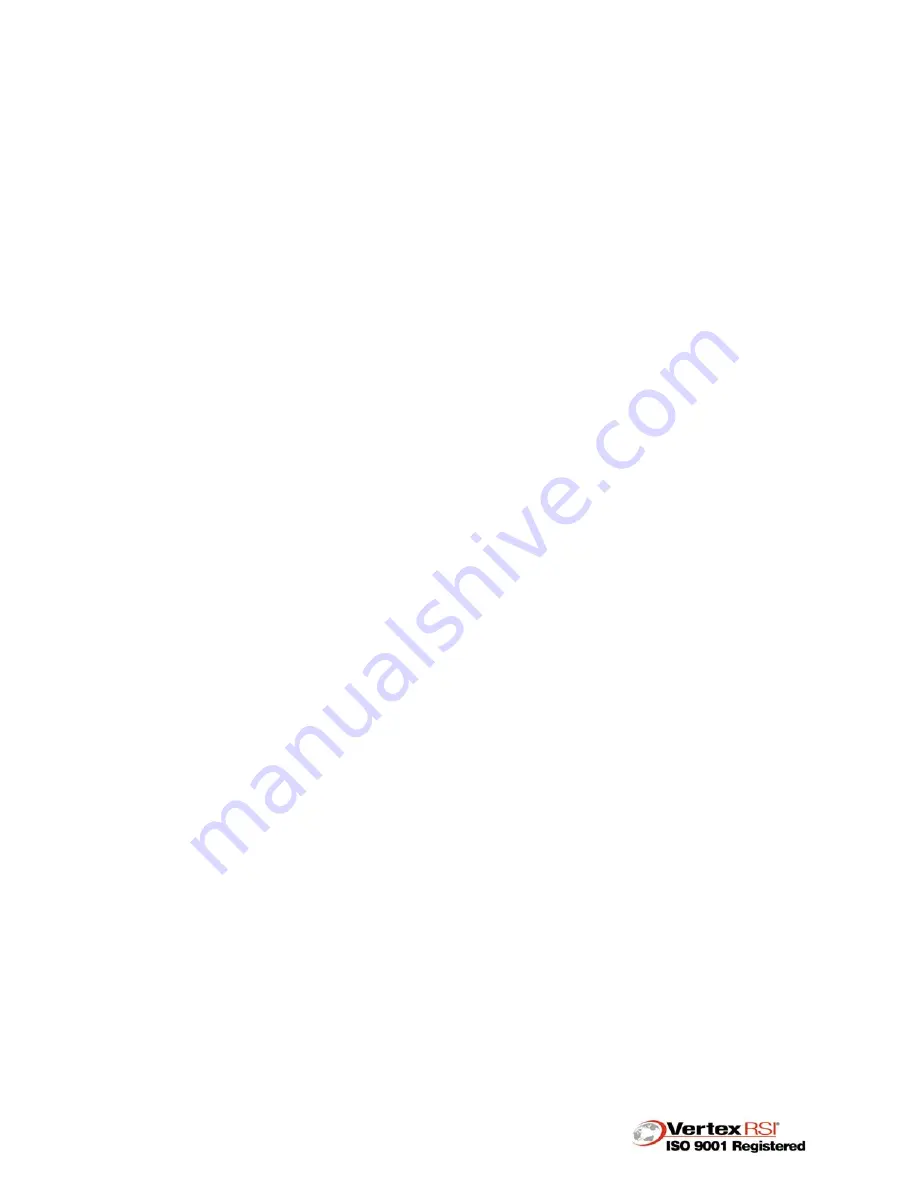
500-0646A 40
3.0 MAINTENANCE
3.1 General
Proper maintenance will keep the antenna in good working condition and ensure the
antenna meets or exceeds the designed life expectancy. Follow a protective
maintenance program that routinely cleans, inspects, lubricates and implements
corrective measurement as required on all mechanical, structural, electrical and
electronic components on the antenna. If there are any discrepancies beyond your ability
to remedy, please contact SATCOM Technologies to acquire the information of how to
deal with them before you proceed.
3.1.1 Antenna Surface Cleaning
A periodic surface cleaning is recommended to remove the excessive accumulation of
dust, dirt and contaminants. A mild detergent solution, soft cloth and soft brushes can
be used to clean the exterior of the antenna.
3.1.2 Electrical Device Cleaning
For electrical and electronic parts, visual inspection of the wires, cables, waveguides,
switches, relays, etc. is required to prevent any bad insulation or loose connections. To
remove dust or loosen foreign particles on the electrical and electronic equipment, use of
a vacuum and soft brush or cloth is recommended. Some electrical and electronic parts
require cleaning using special cleaning solvents. In this case, the parts cleaned need to
be dried for 10-15 minutes before placing them back into operation. Always disconnect
power and use lock-out tags to prevent shock hazards to personnel when servicing any
electrical component.
3.1.3 Mechanical
Maintenance
The antenna mechanical and structural parts such as reflector, pedestal, drive system,
anti-icing system (if installed) and hardware need to be periodically inspected in order to
ensure proper operation. Where there are no established wear limits, perform a visual
inspection to identify worn or damaged parts to avoid the improper functioning of the
earth station. Periodically, check all hardware to make sure it is properly tightened.
Motorized antenna lubricants need to be checked every six months at each jack and
bearing location.
3.1.4 Pedestal Turning Head And Bearing Plates
Lubricate with medium-grade white lithium grease by inserting the nozzle in the space
between the pedestal turning-head’s front and rear sections then between the clamping
bolts of the pedestal turning head (see Figure 2).
3.1.5 Feed
Window
Inspection
A visual inspection of the feed window should be performed periodically to prevent
contaminates from entering the feed. Look to make sure the feed window is tight on the
feed horn and has no cracks or splits.
Содержание 500-0646
Страница 8: ...500 0646A vi LIST OF TABLES Table 1 Tool List 3...
Страница 13: ...500 0646A 4 Awl 1 8 Diameter 1 Pliers 2 Flat File Machinist 10 1 Adjustable Spud Wrench 1 Striking Wrench 1...
Страница 23: ...500 0646A 14 Figure 11 Radial Beam Installation...
Страница 24: ...500 0646A 15 Figure 12 Reflector Lacing Assembly...
Страница 26: ...500 0646A 17 Figure 13 Reflector Panel Assembly...
Страница 28: ...500 0646A 19 Figure 14 Reflector Panel Assembly Order...
Страница 31: ...500 0646A 22 Figure 16 Feed Boom Assembly...
Страница 33: ...500 0646A 24 Figure 17 Feed Boom Assembly Supports...
Страница 37: ...500 0646A 28 Figure 20 Feed Assembly Figure 21 Feed Alignment...
Страница 44: ...500 0646A 35 Figure 29 Azimuth Resolver with Bracket Figure 30 Azimuth Resolver side view...
Страница 52: ...500 0646A A 1 APPENDIX A HARDWARE CHARTS Figures of hardware are shown actual size for convenient reference...
Страница 54: ...500 0646A A 3...