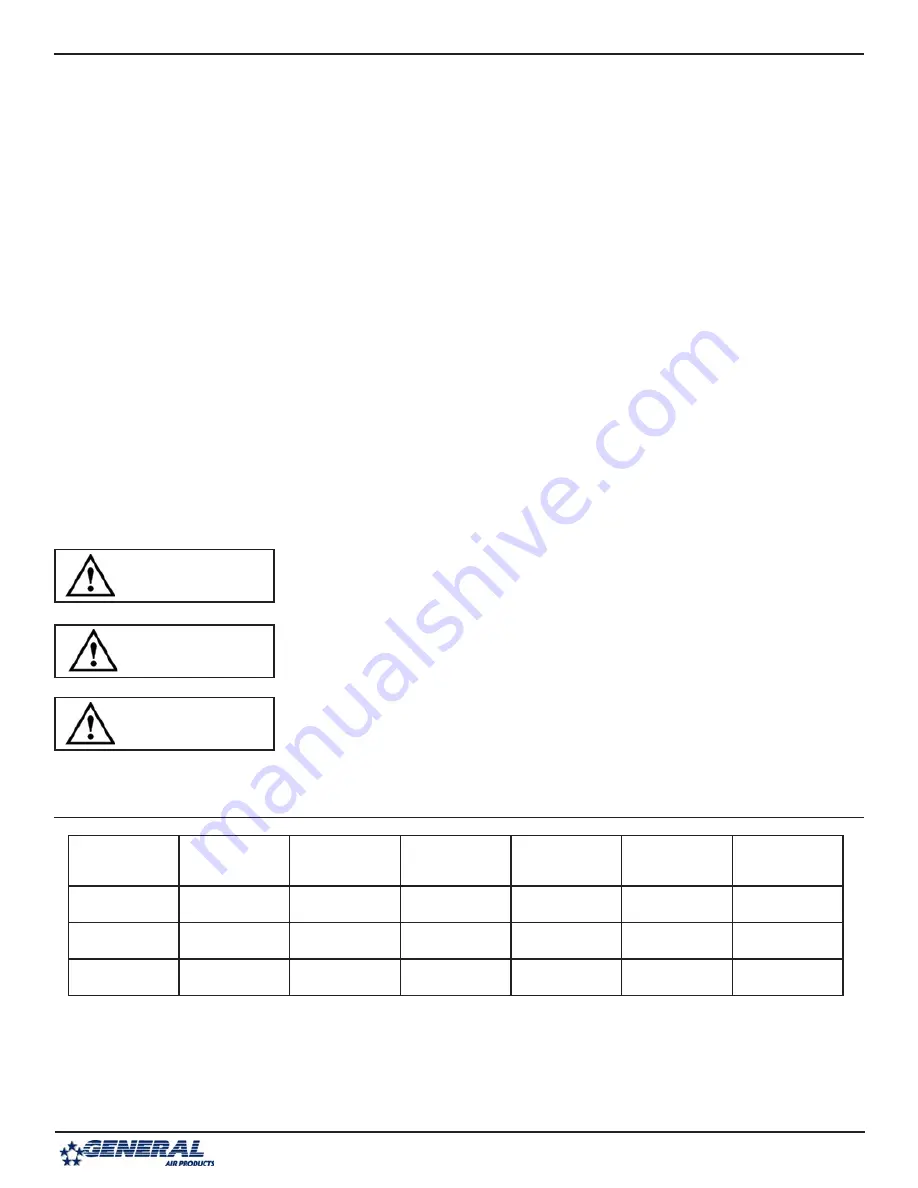
Section 3 - Operation (cont’d)
3.4 Dryer Operating Sequence
The dryer operates on a 4-minute total cycle. There are four valves on the inlet manifold, and four on the outlet
manifold. The outlet valves are check valves, which sequence automatically with the operation of the inlet valves. SV1 and
SV2 are the inlet valves to the towers, SV3 and SV4 are the opposite purge valves such that when the left tower is drying
and its inlet valve is open, the purge valve on that tower is closed.
With the unit turned on and the tank pressurized, air is ready to be used from the unit. As air is withdrawn from the
unit into the sprinkler system, the receiver pressure will drop and the pressure switch will start the compressor. As the
compressor runs, the dryer timer is energized. The drying tower is indicated by a light on the front of the panel and on the
screen of the controller. The drying tower will show receiver pressure and the opposite tank, when purging, will show no
pressure. When repressurizing prior to switch over, it will rise to receiver pressure. The purge valve can only be adjusted
during the time the off line tower is purging and is showing no pressure. At this time, if necessary, adjust the purge pres-
sure to the value in the above table when the on-stream tower pressure is 80 psig and purge tower pressure is 0 psig. The
dryer cycle timer runs only when the compressor is running and accumulates time so that the length of the cycle on each
tower does not get out of line with normal operation and does not saturate one desiccant bed. Purge valves are only open
when the compressor runs. This minimizes compressor run time.
The frequency of change for the oil, filter elements and desiccant is highly dependent upon the following:
- Number of times the unit has to operate to satisfy the system air requirement. The tighter the system,
the less the unit will have to run.
- Cleanliness of the environment in which the compressor is located.
- Maintenance schedule for the equipment.
As the desiccant will degrade (age) slightly over time, it is recommended that the desiccant
be inspected once every year. This can be done by briefly removing the lower tower plugs
to let a few beads out of each tower. Desiccant beads should be firm and white with very
little dust. Replace desiccant if any yellowing or powdery conditions exist.
Turn off and depressurize the Dry Air Pac before removing tower plugs.
When the desiccant is replaced, all filter elements and oil should also be changed at that
time if they have not been already. At a minimum the oil and filters should be changed every
750 run hours.
Section 4 - Additional Specifications
Model
Compressor
HP
Dryer Rating
CFM
Current Load
460V
Current Load
230V
Wire Size 460V
Wire Size 230V
DAP500
2
10
2.9 Amps
5.8 Amps
12 GA
12 GA
DAP1000
5
20
6.
3
Amps
12.
6
Amps
12 GA
10 GA*
DAP2000
5
27
6.
3
Amps
12.
6
Amps
12 GA
10 GA*
*IF UNDER 50' RUN 12 GA CAN BE USED HOWEVER, CHECK VOLTAGE WHILE RUNNING TO ENSURE NO UNDERVOLTAGE CONDITION
EXISTS. FOR RUNS OVER 100' INCREASE WIRE SIZE TO CORRECT FOR VOLT DROPS.
1-800-345-8207
NOTICE
NOTICE
DANGER
Содержание Dry Air Pac DAP1000
Страница 14: ...Section 8 Dry Air Pac General Arrangement cont 8 2 General Arrangement for Models DAP 500...
Страница 15: ...Section 9 Dry Air Pac Electrical Schematics 9 1 Electrical Schematic Wiring Diagram DAP With PLC Option...
Страница 16: ...Section 9 Dry Air Pac Electrical Schematics 9 2 Electrical Schematic Single Phase 115v 60hz or 110v 50hz...
Страница 17: ...Section 9 Dry Air Pac Electrical Schematics 9 3 Electrical Schematic Single Phase 208 230v 60hz or 220v 50hz...
Страница 18: ...Section 10 Dry Air Pac P ID Diagram...