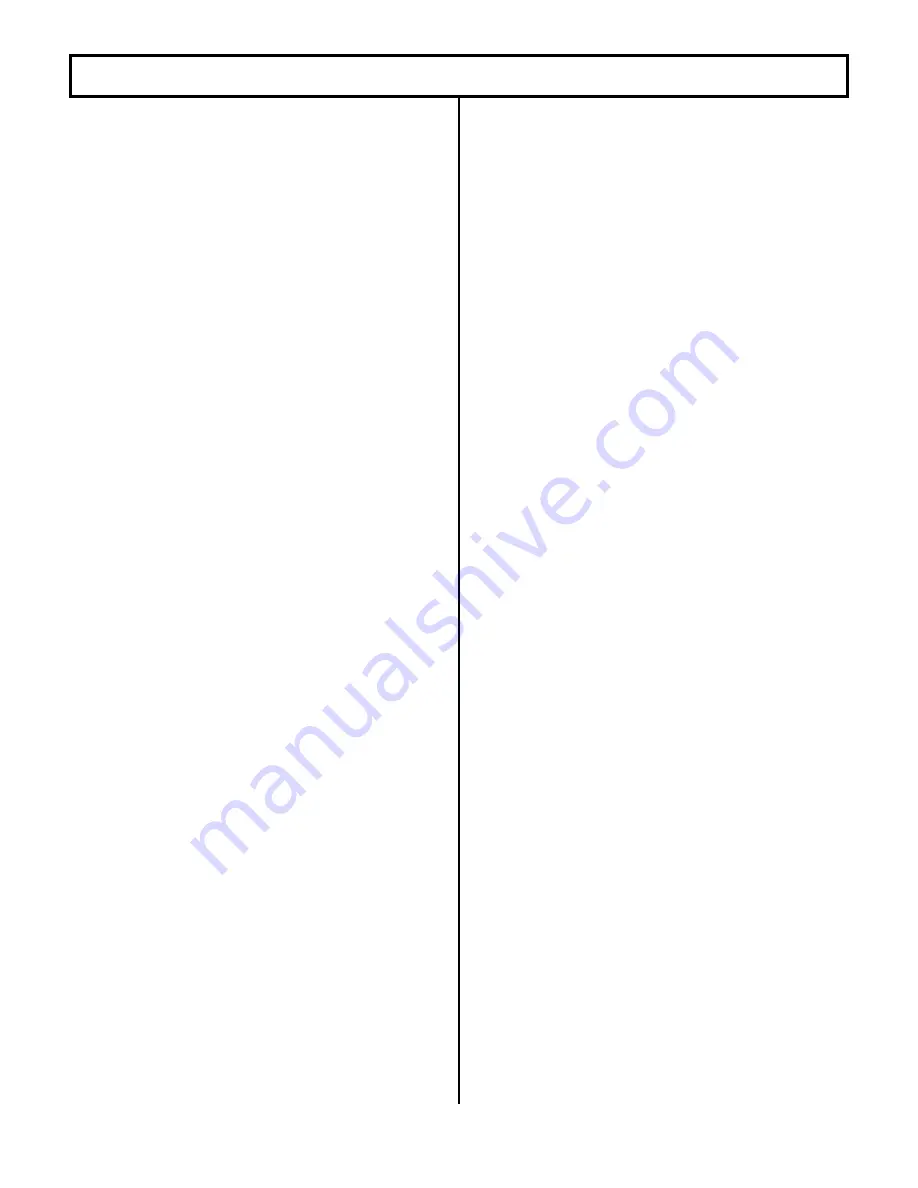
DIAGNOSTIC STATUS CODES
SX TRANSISTOR CONTROL
Page
17
November 2002
Section 4.4 Controller Mounting Guidelines
In the design of the GE family of motor controls,
performance assumptions were made based on heat
transfer between the control and the ambient environment.
The vehicle mounting surface acts as a heat sink, which
increases the effective surface area for heat dissipation. If
this assumed heat transfer is not achieved during control
installation and operation, GE controllers will fall short of
their anticipated performance. It should be noted that the
condition of the mounting surface, and the quality of the
resulting interface between the control and the vehicle, can
significantly hinder heat transfer from the control. The
presence of contaminants, or of air voids created by
surface inconsistencies in either the vehicle or the control,
degrade the control’s capacity for heat transfer. The
control’s performance is de-rated proportionally as its own
thermal sensors reduce its operation to protect it from
damage due to excessive heating.
Contained within the software of the GE controls are
several diagnostic status codes related to controller
thermal performance. Failure to follow these mounting
recommendations increases the likelihood of encountering
these status codes, through no fault of the control itself,
thus voiding controller warranty for units returned solely
due to the presence of these status codes.
Careful surface preparation, including adequate
application of thermal compound, as detailed in the
following paragraphs, must be completed during the
installation of GE controls. There are many techniques for
applying thermal compound, and we have outlined one
approach below that has shown to apply a consistent
thickness of material.
Section 4.4.1 Necessary Tools
GE recommends the use of the following components, or
equivalent substitutions, during the control installation
process:
a) Thermal compound, (Dow Corning #340),
maintained per the manufacturer’s
recommendations and free of contaminants
b) 3/32” notched trowel, such as a Krusin
adhesive spreader, model 00031
c) Calibrated torque wrench (0 – 15 ft-lbs)
Section 4.4.2 The GE Control Mounting Surface
During the manufacture of the GE control, the surface
flatness is maintained at 0.005” per linear inch (not to
exceed 0.025” per 10.0 inches). The surface finish of the GE
control has an R
a
(average roughness) of 64 (microinches),
or better. This finish is consistent with cold rolled or
extruded aluminum.
Care should always be taken in the handling and storage of
controllers. The base of the control should be free from
nicks, bumps, protrusions or any other foreign object that
would prevent the control from sitting flush with the vehicle
mounting surface. Examine the base of the control to verify
that it is in good condition and free from damage or
contamination.
Section 4.4.3
Vehicle Mounting Surface
The quality of the vehicle mounting surface is critical for
the optimum heat transfer between the control and the
ambient environment. Conduction through the base of the
control is the control’s only means of heat rejection. While
GE controls are highly efficient, a few percent of the
electrical energy will be converted into heat. As previously
mentioned, if this energy is not dissipated through the base
of the control, a thermal protector will reduce the
performance of the control until the temperature stabilizes.
For optimal heat transfer from control to vehicle, the
flatness of the vehicle mounting surface should be
equivalent to the flatness of the control surface (0.005” per
linear inch). Use a straight edge or dial indicator to verify
the mounting surface.
The biggest hindrance to heat transfer is the presence of
rust, scale, weld splatter or paint on the vehicle mounting
surface. If any of these items are noted, prepare the
surface per the following guidelines:
a) Clean the mounting surface with a rotary wire
brush until the metal surface is exposed.
b) Using 80-100 grit emery paper, sand the
surface until the metal shines.
c) Flush the surface clean with an appropriate
liquid de-greaser or parts cleaner.
Section 4.4.4 Application of Thermal Compound
Due to the minute differences in the control mounting
surface and the vehicle mounting surface, small pockets of
air will be created. These air pockets will add to the overall
thermal resistance of the interface.
To avoid these air pockets and improve thermal
conductivity, thermal compound must be applied between
the GE control base plate and the vehicle mounting surface.
The function of this compound is to conform to surface
discrepancies, filling gaps and optimizing the metal-to-
metal contact of the control and the vehicle.
a) Prepare the two mounting surfaces (control
and vehicle) as indicated above.
b) Using a triangular notched trowel of 3/32”
(.09” +/- .01), apply the grease to the vehicle
mounting surface.
c) Use straight, non-crossing strokes of the
trowel to apply the compound.