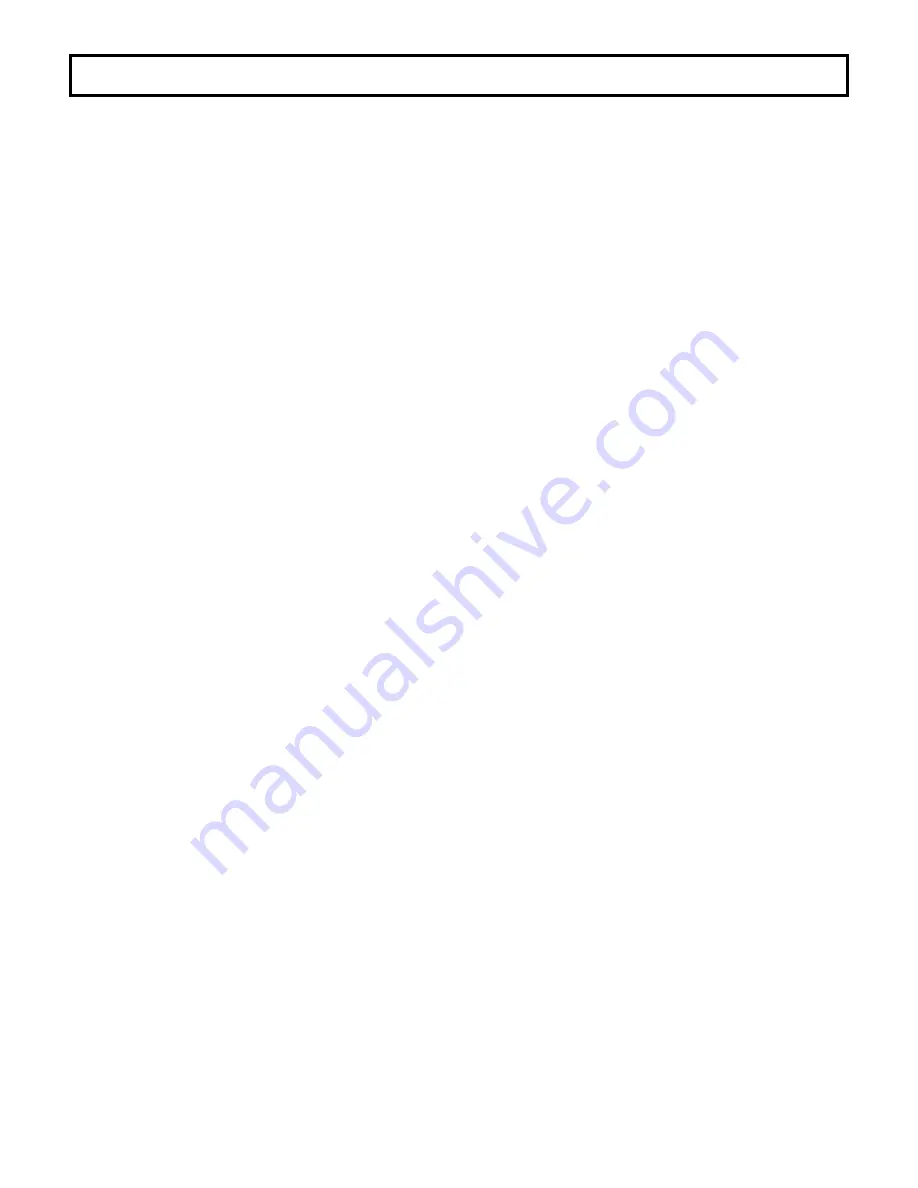
BASIC OPERATION AND FEATURES
SX TRANSISTOR CONTROL
Page
12
November 2002
This serial communication port can be used with Interactive Custom Dash Displays to allow changes to vehicle operating
parameters by the operator. Or, it can be used by service personnel to dump control operating information and settings into a
personal computer program.
Section 2.3.6.a Interactive Dash Display
Modes
The Interactive Custom Dash Display allows the operator to select the best vehicle performance for changing factory (task)
conditions. There are four (4) "operator interaction modes" that can be selected by depressing a push button on the dash display.
From the Dash Display, the operator may select any of four pre-set interactive modes consisting of (4) Controlled Acceleration
levels, (4) Field Weakening levels and (4) Speed Limits.
These interactive modes are "pre-set" using the Handset (Functions 48-62) or a personal computer (Functions 97- 112). This
feature allows the operator to select the best vehicle performance for changing factory (task) conditions.
Section 2.3.7 Circuit Board Coil Driver Modules
Coil drivers are internal to the control card, and are the power devices that operate the Line and 1A contactor coils. On
command from the control card, these drivers initiate opening and closing the contactor coils. All driver modules are equipped
with reverse battery protection, such that, if the battery is connected incorrectly, the contactors can not be closed electrically.
Section 2.3.8 Truck Management Module (TMM)
The Truck Management Module is a multifunction accessory card, or an integral function of the GE Pump controls when used
with the SX Traction control. The Module provides the OEM the ability to initiate status codes or operator warning codes to be
displayed on the Dash Display, whenever a normally open switch or sensor wire provides a signal to the Module.
The TMM Module can be used to display a separate status code indicating over-temperature of traction motors, hydraulic
motors, or any other device or system that can activate a switch that closes.
The TMM Module can also be used as a Brush Wear Indicator (BWI). The Brush Wear Indicator is designed to detect a "worn
out brush" and display a fault code on the Dash Display to warn maintenance personnel that the motor brushes need to be
replaced before they wear to the point of causing destructive damage to the motor commutator surface.
Section 2.4 Hydraulic Pump Control
This hydraulic motor controller consists of the following features:
•
Three speeds, adjustable from O to 100% motor volts. Fixed speeds actuated by switch closure to negative.
•
Current limit and controlled acceleration adjustable.
•
Battery Discharge Indicator interrupt compatible.
•
Coil driver module designed to operate the line contactor (see Section 2.3.7).
Operation of voltage regulator card: This card provides the basic functions required for controlling the pump control, optional
contactors, and PMT functions. Battery positive is applied through a main control fuse to the key switch, energizing the control
card power supply input to P1.
When a pump contactor is used, PMT operation is the same as outlined for the traction controllers.
The three speed (motor volts) reference points P12, P19, and P20 are selected by connecting these points independently to
battery negative.
The first speed is obtained by closing Speed Limit I (P12) to control negative. SLl is adjustable by Function 11 using the Handset
to adjust motor voltage from O to 100%. The specified motor volts will be regulated, however, the magnitude of motor current will
vary depending on the loading of the vehicle.
The second speed is obtained by closing SL2 (P19) to control negative. SL2 is adjusted using the Handset and Function 12 similar
to SL1.