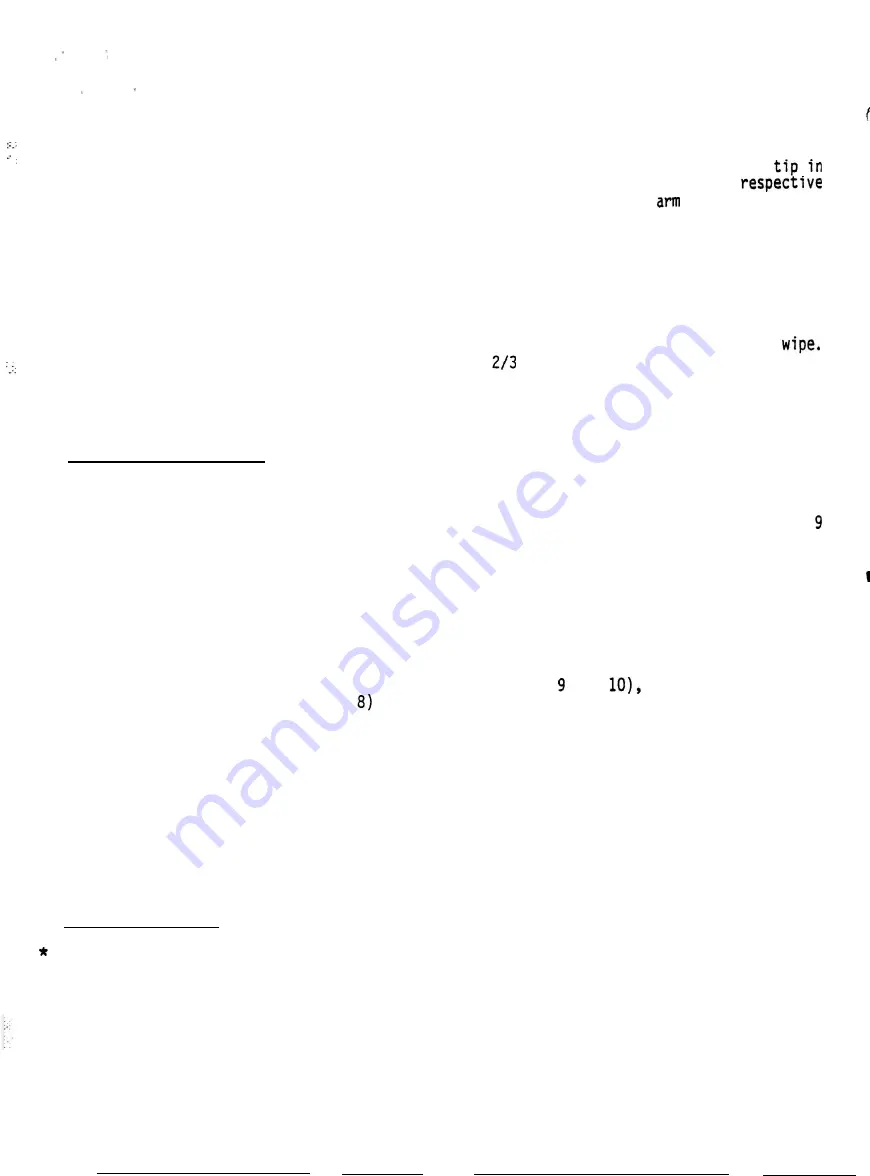
GEK-49822
Loosen the locknut which secures the backstop screw (located at the right hand
corner of the unit) to its support.
Unwind the backstop screw so that the moving
contact arm is permitted to swing freely.
Adjust the tension of each low gradient
contact brush so that one-to-two grams of pressure are required at the contact
order to cause the end of the brush to separate from the inner face of its
brush retainer. Adjust the spiral spring until the moving contact
is in a neutral
position, i.e., with the arm pointing directly forward.
Loosen the locknut which
secures the stationary contact mounting screw to the stationary contact support.
Wind
the mounting screw inward until the stationary and moving contact members just begin to
touch.
Unwind the mounting screw until the stationary contact stop lines up with the
moving contact brush retainer.
Wind the backstop screw inward until the moving and
stationary contact members again just begin to touch.
Loosen the locknut of the
stationary contact stop screw, and advance this screw until it just touches the moving
contact brush retainer. Unwind the screw one and a half turns to provide contact
Tighten the locknut.
Unwind the backstop screw
turn and tighten the locknut which
secures the
backstop screw to its support.
Finally, adjust the tension on the
stationary contact brush such that, when the contacts are made and fully wiped in, ,
there is approximately an equal deflection on each brush.
Bias Torque Adjustment
Connect the current operating and current polarizing coils in series by connecting a
jumper across terminals 5 and 8.
Apply current to terminals 4 and 7 and adjust the
directional unit spiral spring so that the unit picks up at 0.5 ampere with terminals
and 10 jumpered.
The core of the directional unit has a small flat portion, the purpose of which is to
minimize the effect of bias torques produced on the rotor.
Such torques can be
produced by any one of the operating or polarizing quantities acting alone with the
other two circuits de-energized.
The adjustment of the core is made at the factory,
but may be checked by observing that the unit responds as outlined below:
Short out the potential polarizing coil (terminals and
leaving the current
polarizing coil (terminals 7 and unshorted. Supply 30 amperes through the operating
coil (terminals 4 and 5) and check that the unit does not operate.
If the unit does not satisfy the above conditions, rotate the core to a position
which causes it to do so. The core can be turned by loosening the large hexagonal nut
at the bottom of the unit and turning the core by means of the slotted bearing screw.
This screw should be held securely in position when the nut is retightened.
Keep in mind that thirty amperes will cause the current coils to overheat if left on
too long. Therefore, leave the test current on only for short intervals and allow
sufficient time between tests for the coils to cool.
Clutch Adjustment
The connections shown in Fig. 24 for the polarity check can also be used in making
the clutch adjustment. The fixed resistor should be capable of controlling the current
*Indicates Revision
22
Содержание IBCG51M
Страница 24: ...GEK 49822 Fig 1 8043458 Type IBCGHM YlA or the 18CG53M in its Case Front View Indicates Revision 24 YlA Relay...
Страница 36: ...L i i I I I I I i I I I I 0 L...
Страница 37: ...6EK 49822 Fig 14 0376A0934 0 Time Characteristic of Dual Polarized Directional Unit of Type IBCG Relay 37...
Страница 38: ...W 49822 Fig 15 088880269 3 Time current Characteristic of Inverse Time Overcurrent Unit 38...
Страница 45: ...GEK 49822 L I I A Or GLl FR a L Fig 22 D195A9179 0 Test Connections for Checking Pickup of TDC Unit 45...