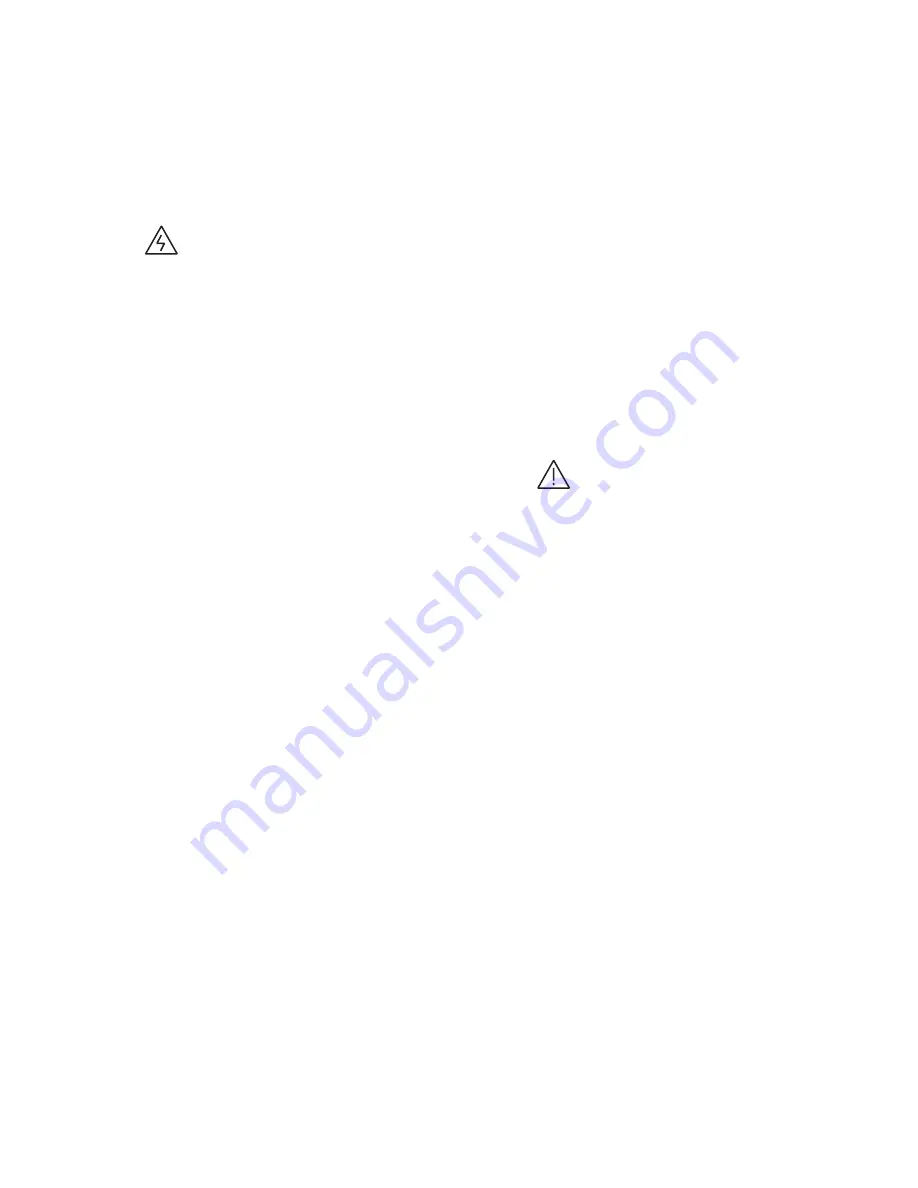
I N S TA L L AT I O N , O P ER AT I O N S A N D M A I N T EN A N C E M A N UA L
33
Maintenance
De-energize all equipment before performing any
maintenance operation. There may be voltage
present within the equipment from remote
sources, even though all main- and branch-circuit
disconnects have been opened at the equipment.
Failure to observe this precaution can result in
serious injury or death.
The customer should prepare a maintenance
program consisting of a schedule and checklist
matrix listing items to be periodically examined on
the installed equipment. The frequency and extent
of the maintenance activities will vary depending
on such factors as equipment usage and
environmental conditions. In any maintenance
program the following actions should be included:
1. Remove accumulated dust and dirt with a soft
cloth, brush or vacuum cleaner.
2. Wipe clean all main bus insulators and vertical
bus barriers.
3. Inspect main and vertical bus joints and main bus
supports and tighten, if necessary. Refer to Table
1 for torque specifications.
4. Inspect all wiring from units for deterioration of
insulation.
5. Remove draw-out units and check stabs and all
unit wiring. Remove accumulated dust from
horizontal shelves and the areas around stabs.
6. Check all starter contacts. They need only be
replaced when nearly all the silver tip is gone and
the contact tip support is exposed. Do not file
the contacts. Filing or otherwise dressing the
contacts only results in lost tip material and
reduces starter life. See publication GET-6915A
for questionable contact appearance.
7. Check all unit wiring for deterioration of
insulation and tighten all connections.
8. Visually check meters and instruments.
Check critical instrument calibrations.
9. Check all unit door interlocks for
proper operation.
10. Check all indicating lights and replace,
as required.
11. If fuse replacement is necessary, always install
the same type and rating as the fuses furnished
with the motor control center. Fuse designs may
be mechanically equivalent but not electrically
equivalent. They may not have the same short-
circuit withstand and current-limiting ability.
Inlet filter maintenance
Filter inspection and cleaning must be carried out
every six months or more frequently as per your
established maintenance plan. The frequency of
filter maintenance or replacements should be
determined individually, depending on dust
accumulation and operating period.
Equipment maintenance
Note:
A soiled filter mat will cause the
temperature to rise inside the enclosure.
The filter mat can be regenerated by
washing or blowing out.
Arc-resistant maintenance
If a unit is removed from an arc-resistant section
for maintenance, a solid blank door should be used
to cover the opening in order to maintain arc
resistance.
Control power
The option to have control power or test power
during service is a functionality that has been
provided with the arc-resistant introduction of the
LV MCC. This is a necessary requirement in order to
check functions during service such as pilot lights
and devices. This is intended to standardize the
offerings when a customer orders common control
power on the MCC. The two options we provide
allow for 1) customer supplied 120VAC power or 2)
self-contained control power within the MCC.
The key switch is utilized to operate the control
power when the stabs are disengaged. The key
switch is turned “On” allowing the secondary
control power to be utilized. The key switch should
be “Off” during normal operation of the MCC.
Содержание Evolution Series E9000
Страница 1: ...INSTALLATION OPER ATIONS AND MAINTENANCE MANUAL Evolution series E9000 Motor control center ...
Страница 2: ......
Страница 50: ...50 EVOLUTION SERIES E9000 MOTOR CONTROL CENTER ...
Страница 51: ......