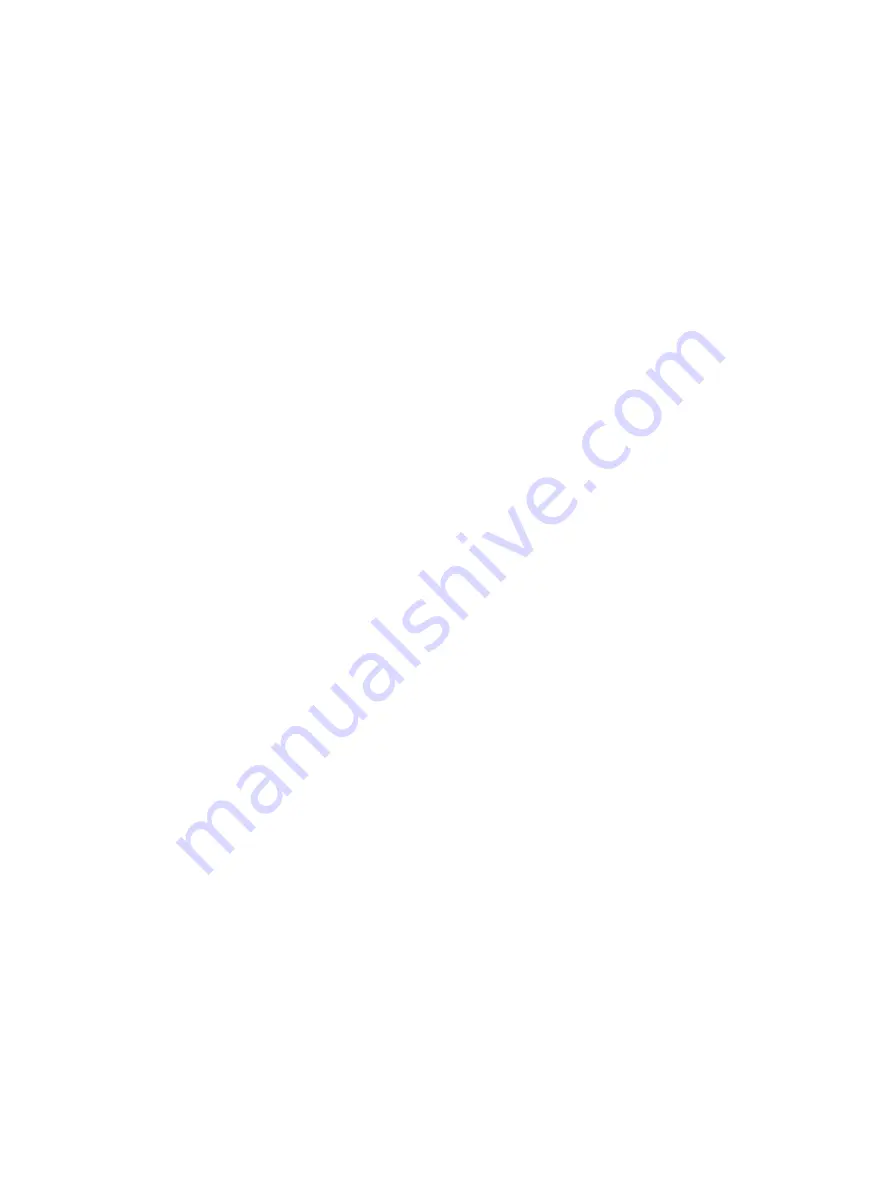
Becker VRP-SB-PID Series Natural Gas Controllers Instruction Manual | 4
© 2016 General Electric Company. All rights reserved.
Principles of Operation
Direct Acting VRP-SB-PID Controller (Figure 2)
When the measured variable pressure (sensing pressure) is
equal to the setpoint, the net force on the sensing diaphragm
is zero. This is the equilibrium or “balanced” condition where the
sensing pressure that pushes down on the sensing diaphragm,
and the spring force that pulls up on the sensing diaphragm are
equal. From this position two possible scenarios can occur, the
sensing pressure can rise above or below the setpoint.
If the sensing pressure rises above the setpoint the net force
on the sensing diaphragm is downward. The bottom balance
valve will close. The top balance valve opens, increasing the
flow of power gas to the output port. The combination of these
actions creates a rise in output pressure. When the sensing
pressure falls below the setpoint the net force on the sensing
diaphragm is upward. Now the top balance valve will close.
The bottom balance valve opens, increasing the flow of
gas to the exhaust port. The combination of these actions
decreases the output pressure.
In order to control how much gas passes through the balance
valve, the output pressure is fed back to the bottom side of a
diaphragm within the feedback module. As the output pressure
increases, this feedback pressure closes the inlet balance valve.
As the output pressure decreases, this feedback pressure
decreases, closing the exhaust balance valve. This feedback
force is such that the output pressure will change proportionally
with the deviation of the sensing pressure from the setpoint,
which gives us a proportional response.
By restricting the flow of the output pressure to the bottom side
of the feedback diaphragm, a derivative function is introduced.
This is accomplished with an adjustable orifice that controls the
flow to the bottom side of the feedback diaphragm. This orifice
delays the feedback force, allowing the output to change quickly
in response to a quick change in the system. Slow changes in
the system; however, are less affected by the derivative orifice
because the output pressure has time to equalize on both sides
of the orifice. The adjustability of the orifice allows us to optimize
the system. If the restriction is too great, the feedback delay will
be too long and the system will become unstable.
It is already established that the change in output pressure
is proportional to the deviance of the sensing pressure.
Because of this, a sensing pressure that is not at the setpoint
is required to maintain a particular change in output pressure.
The difference between the setpoint and the maintained
pressure at a particular output pressure is the “offset”. This
offset can be eliminated over time by allowing the top side
of the feedback diaphragm to slowly equalize with the bottom
side. By using a metering valve to control the flow to the top
side of the feedback diaphragm we introduce our integral
function. This adjustment also allows us to optimize the system.
If the top side of the diaphragm equalizes with the bottom side
too quickly, the feedback function providing proportionality is
cancelled out and control will become unstable.
Reverse Acting VRP-SB-PID Controller (Figure 3)
In this case, the power gas is fed through the bottom balanced
valve instead of the top. The exhaust now vents from the top
balanced valve, and use of the feedback chamber is reversed.
This simply means that the adjustable orifice controls the flow
to the top feedback chamber, and the metering valve controls
the flow to the bottom feedback chamber.
If the sensing pressure rises above the setpoint then the net
force on the sensing diaphragm is down. The bottom balanced
valve will close. The top balanced valve opens, allowing gas
to vent through the exhaust port. The combination of these
actions results in a decrease in output pressure. If the sensing
pressure falls below the setpoint, the net force on the diaphragm
is upward. The bottom balanced valve opens, increasing the
flow of power gas to the output. The top balanced valve will
close. This combination creates a rise in output pressure.
As the name implies, the dynamics are completely “reversed”
from the direct acting configuration. The same can be said about
the feedback chamber dynamics. The output pressure is now fed
into the top side of the feedback diaphragm, while elimination of
the “offset” is accomplished by feeding the output pressure to
the bottom side of the feedback diaphragm.