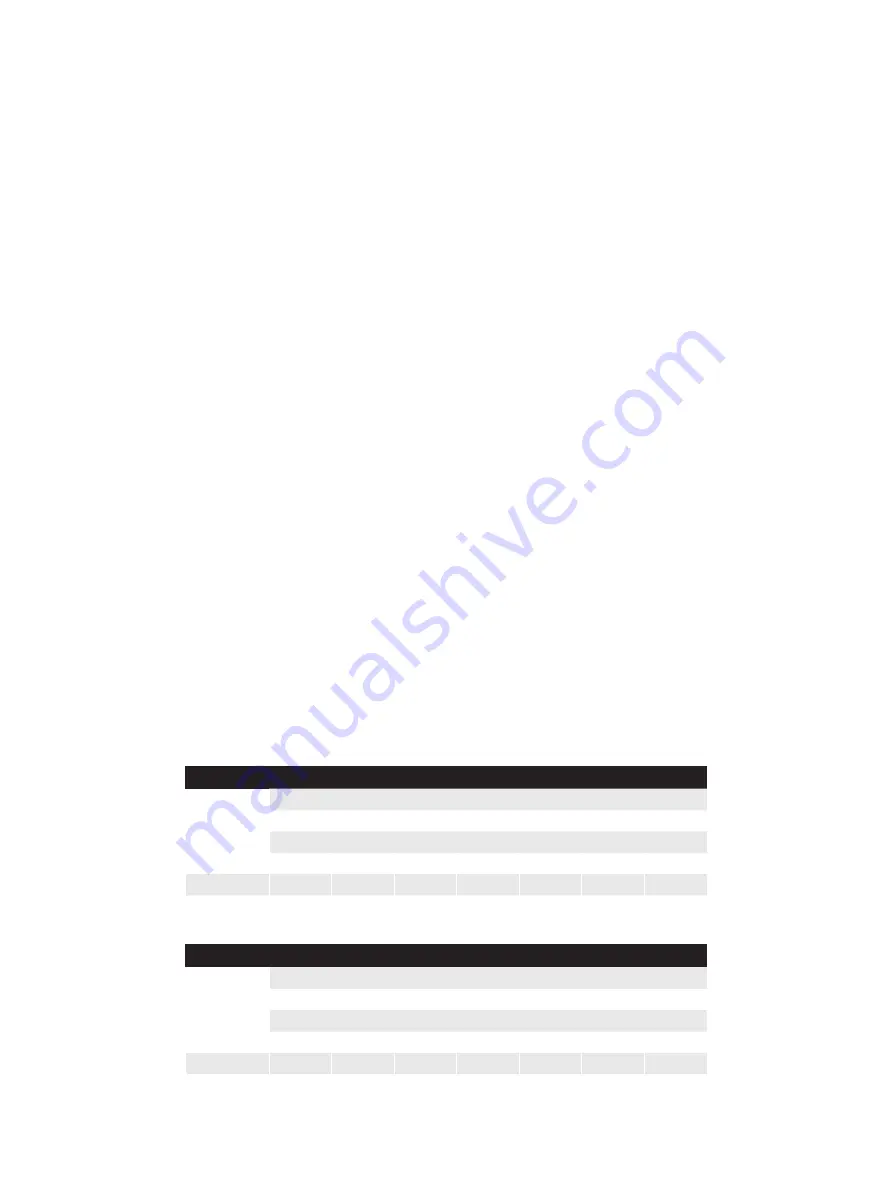
Becker VRP-B-CH Series Valve Regulator Pilot Instruction Manual | 6
© 2016 General Electric Company. All rights reserved.
Adjustment Procedures
Your VRP-B-CH pilot will come factory adjusted for your
particular application. The use of the adjustment procedures will
be necessary upon installation of a rubber goods replacement
kit or any other disassembly or reassembly of the pilot.
The sensitivity adjustment drum in the center of the pilot
determines the sensitivity of the unit.
The setpoint adjustment screw determines the setpoint at which
the pilot operates. The variable orifices determine the response
speed of the pilot.
Initial Adjustment
1. Adjust the supply regulator
Adjust the supply regulator to the desired power gas pressure.
Refer to the original invoice paperwork supplied with the
product for the appropriate power gas pressure setting. It is
imperative that adequate supply gas pressure be supplied
to the VRP-B-CH in order to ensure proper operation of the
system and all accessories.
2. Adjust the adjustable orifices
The adjustable orifices are used to control the volume of gas
that is supplied to the VRP-B-CH. The stroking speed of the
system is proportional to the numerical value of the adjustable
orifice. Adjustable orifice settings are typically equal for both
orifices. However, a few applications may require unequal
settings for each adjustable orifice. Set both orifices according
to the table A below if pilot bleeds to atmosphere and table B
if pilot bleeds to pressure system.
Notes:
• To determine the cylinder bore, look at the model number
stamped on the stainless steel tag on the top of the cylinder.
The cylinder bore will be the first number following the first
capital letter “H”. This one or two digit number following the
first “H” will be the diameter in inches and will be followed
by another letter (for example, a unit with the model number
6H8F6FG-PCH has an 8-in. bore).
• If equipped with a DPS sensor and/or AB-control, see page 20.
3. Disable DPS-2 series non bleed sensor (if equipped):
The DPS-2 non bleed sensor should be disabled prior to
commencing initial adjustment procedures. Failure to disable
the DPS non bleed sensor may prevent initial adjustments
from being completed properly. To disable the DPS-2 series
non bleed sensor(s) rotate the adjustment screw of the DPS-2
until it extends approximately 1.75-in from the top surface of
the DPS-2 spring cartridge.
4. Disable AB series atmospheric bleed control (if equipped):
The AB series atmospheric bleed control should be disabled
prior to commencing initial adjustment procedures. Failure to
disable the AB control may prevent initial adjustments from
being completed properly. To disable the AB control rotate the
adjustment screw of the AB control until it disengages. Then,
tighten the nut on the AB sensor adjustment screw to seal
threads on the cap
5. Close cylinder block valves:
Closing the cylinder block valves will isolate the VRP-B-CH
from the control valve actuator. This prevents unintended
stroking of the control valve and simplifies setting the
VRP-B-CH.
6. Close the valve on the sensing line:
It is imperative that a full-sealing valve be installed as close to
the sensing port of the VRP-B-CH as possible. The volume of
gas between the VRP-B-CH sensing port and the block valve
on the sensing line should be minimized. It is also imperative
that the fittings between the VRP-B-CH sensing port and the
sensing line block valve be bubble tight in order to facilitate
adjustment. It is recommended that a quarter-turn (locking)
ball valve be utilized to isolate the VRP-B-CH sensing line.
Confirm that the VRP-B-CH exhaust (discharge) line is open.
The discharge line is connected to the port marked “EX”.
Should flow from the exhaust port be blocked, adjustment
of the VRP-B-CH will not be possible.
Table A – Exhaust Vented to Atmosphere
Supply
Pressure
(psig)
Cylinder Bore (In.)
4
5
6
8
10
12
14
Variable Orifice Number
Up to 50
3
3
3
4
4
5
6
51-200
2
2
3
3
4
5
5
201-600
2
2
2
3
3
4
5
Table B – Exhaust Vented to Pressure System
Supply
Pressure
(psig)
Cylinder Bore (In.)
4
5
6
8
10
12
14
Variable Orifice Number
Up to 50
3
3
3
4
4
5
6
51-200
4
4
4
5
5
6
6
201-600
2
2
2
3
3
4
5