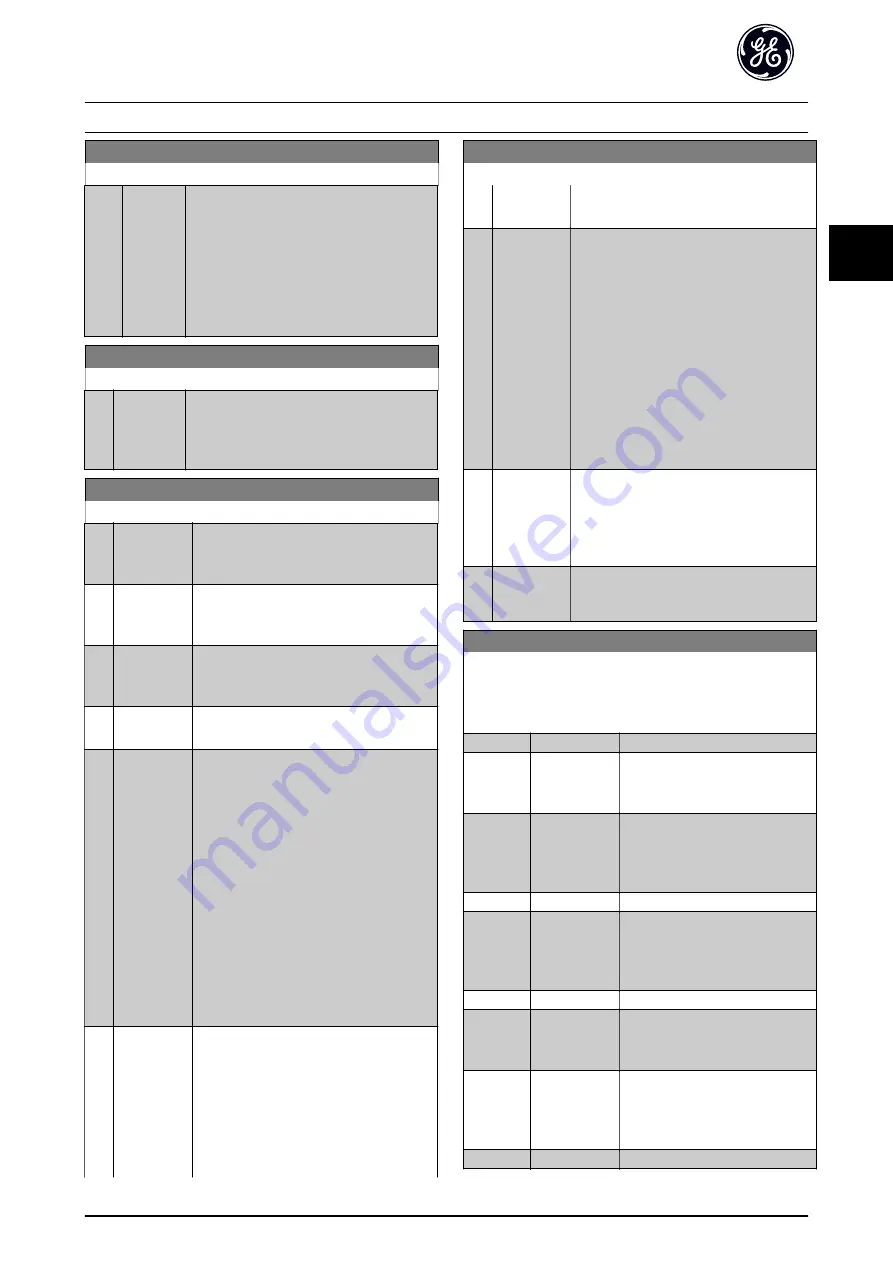
F-23 Start Speed [Hz]
Range:
Function:
0 Hz
*
[0 -
500.0 Hz]
This parameter can be used for hoist
applications (cone rotor). Set a motor start
speed. After the start signal, the output speed
leaps to set value. Set the start function in
to
[3] Start speed cw
,
[4]
Horizontal operation
or
[5] Adv. Vector Control/
Flux Clockwise
, and set a start delay time in
F-24 Holding Time
Range:
Function:
0 s
*
[0 - 25.5 s] This parameter refers to the start function
Enter the time delay required before
commencing acceleration.
F-25 Start Function
Option:
Function:
Select the start function during start delay.
This parameter is linked to
.
[0]
DC Hold/
delay time
Energizes motor with a DC holding current
(
) during the start delay
time.
[1]
DC Brake/
delay time
Energizes motor with a DC braking current
(
) during the start delay
time.
[2]
*
Coast/delay
time
Motor coasted during the start delay time
(inverter off).
[3]
Start speed
cw
Only possible with Advanced Vector Control.
Connect the function described in
and
in the
start delay time.
Regardless of the value applied by the
reference signal, the output speed applies
the setting of the start speed in
or
and the
output current corresponds to the setting of
the start current in
. This
function is typically used in hoisting
applications without counterweight and
especially in applications with a Cone-motor,
where the start is clockwise, followed by
rotation in the reference direction.
[4]
Horizontal
operation
Only possible with Advanced Vector Control.
For obtaining the function described in
and
during the start delay time. The motor
rotates in the reference direction. If the
reference signal equals zero (0),
is ignored and the output speed
equals zero (0). The output current
F-25 Start Function
Option:
Function:
corresponds to the setting of the start
current in
.
[5]
Adv. Vector
Control/Flux
Clockwise
For the function described in
only. The start current is calculated
automatically. This function uses the start
speed in the start delay time only. Regardless
of the value set by the reference signal, the
output speed equals the setting of the start
speed in
[3] Start
speed/current clockwise
and
[5] Advanced
Vector Control/Flux clockwise
are typically
used in hoisting applications.
[4] Start speed/
current in reference direction
is particularly
used in applications with counterweight and
horizontal movement.
[6]
Hoist Mech.
Brake Rel
For utilizing mechanical brake control
functions,
. This parameter is only active when
is set to [3]
Flux
w/ motor feedback
.
[7]
Adv. Vector
Control/Flux
Counter-cw
F-26 Motor Noise (Carrier Freq)
Select the carrier frequency. Changing the switching frequency
can help to reduce acoustic noise from the motor. Default
depends on power size.
Option:
Function:
[0]
1.0 kHz
[1]
1.5 kHz
Default switching frequency for
355-1200 kW / 500-1600 HP at 690
V
[2]
2.0 kHz
Default switching frequency for
250-800 kW / 350-1200 HP at
400/460 V and 37-315 kW / 50-450
HP at 690 V
[3]
2.5 kHz
[4]
3.0 kHz
Default switching frequency for
18.5-37 kW / 25-50 HP at 240 V and
37-200 kW / 50-300 HP at 400/460
V
[5]
3.5 kHz
[6]
4.0 kHz
Default switching frequency for
5.5-15 kW / 7.5-20 HP at 240 V and
11-30 kW / 15- 40 HP at 400/460 V
[7]
*
5.0 kHz
Default switching frequency for
0.25-3.7 kW / 0.33-5 HP at 200 V
and 0.37-7.5 kW / 0.5-10 HP at
400/460 V
[8]
6.0 kHz
Parameter Descriptions
AF-650 GP Programming Guide
DET-618C
37
3
3