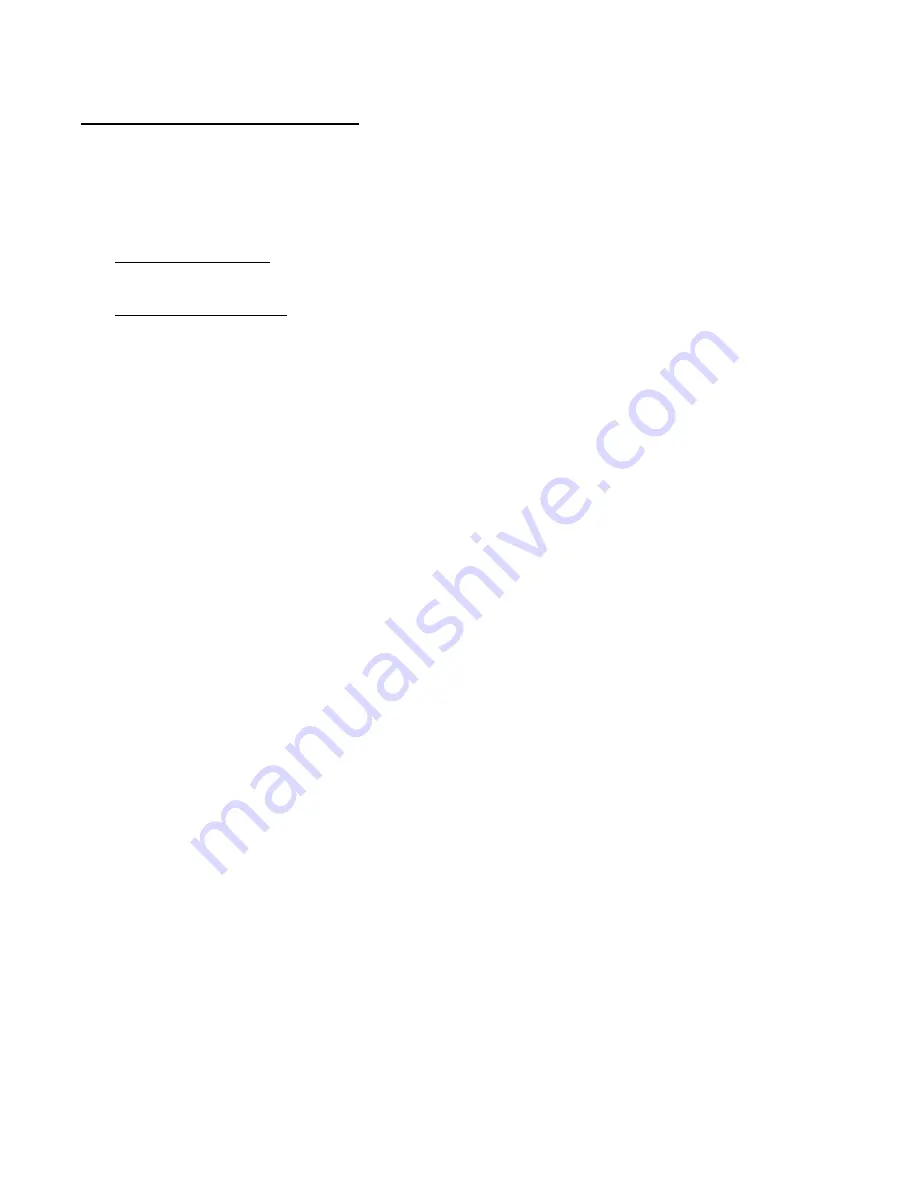
13-25-629 v03 Page 37
MISCELLANEOUS CONTROL DEVICES
- Refer to Figure 4-15 for the schematic diagram of the control system.
Intake [Air] Filter (1) -
Captures solid impurities in the air stream entering compressor inlet. It also attenuates
noise emitted by the compressor inlet.
Inlet-Valve Assembly (2) -
This device controls the intake of atmospheric air entering the compressor during the
Load/Unload phases of operation.
During the loaded state: The
inlet poppet (2.2)
remains open and enables atmospheric air to enter the
compressor inlet.
During the unloaded state: The
2-way solenoid valve (Y
) feeds pressurized air underneath the
piston
(2.1)
, forcing it and
the inlet poppet (2.2)
upward and blocking-off the compressor intake. A
small purge
orifice (18)
, located below the poppet, allows a stream of air to reach (e.g., purge) the rotors and keep them
from unstable, noisy operation and producing sufficient pressure to maintain cooling/lubricating oil flow. See
Section 9 for maintenance information.
Electric Motor (3)
–
Drives the
compressor (4)
via a
belt drive assembly (5),
and drives the package
ventilation fan from a secondary rear shaft.
It is energized by the full voltage-type starter (variable speed drive in
1 phase models), which in turn is controlled by the GD Pilot controller.
Oil Sump (6)
–
Separates by inertial effects the bulk of the compressed air and injection oil streams and serves
as a sump for the latter.
Air/oil separator (7) -
Intercepts and coalesces the aerosol oil stream in the compressed air exiting the inertial
separation process within the oil sump.
Oil Filler Cap (8)
–
Oil fill port on the oil sump.
Oil drain (9, 28)
– Ball valve (9) drains the oil from the sump and cap (28) drains the oil trapped in the oil cooler
and associated hoses.
Oil Level Indicator (10) -
This gauge is located on the oil sump and indicates the oil level. See “Oil Level Gauge”
on Section 5 for more details.
Oil Filter (11) -
Captures solid impurities in the oil entering the compressor injection port.
Oil Cooler (12)
–
The air-cooled heat exchanger removes heat from the oil stream prior to injection.
Pressure Relief Valve
(13)
– This device protects the pressure containing components of the compressor
package against high pressure exceeding 217 psig. See Section 9 for maintenance information.
Minimum Discharge Pressure/Check Valve (14) -
This device maintains minimum pressure (70 psig) within the
air/oil sump, thus ensuring adequate lubricating oil injection flow to the compressor even when no air delivery into
the system is taking place. It also functions as a check valve to prevent reversed air flow from the system line
during compressor stoppage. See Section 9 for maintenance information.
Air cooler (15)
–
The air-cooled heat exchanger removes heat from the air stream prior to exit from the package.
Scavenge line orifice and orifice (16)
–
This annular orifice, built into the air/oil separator element adaptor pipe,
controls the amount of oil and compressed air that is returned from the air/oil separator back into the compressor.
A separate check valve (19) prevents the backflow of oil into the air/oil separator element upon unit stoppage.
Содержание L4-5C
Страница 24: ...13 25 629 v03 Page 24 FIGURE 4 2 WIRING DIAGRAM 208 230 460V 60 Hz 306ECA546 B Ref Drawing Page 1 of 3...
Страница 25: ...13 25 629 v03 Page 25 FIGURE 4 3 WIRING DIAGRAM 208 230 460V 60 Hz 306ECA546 B Ref Drawing Page 2 of 3...
Страница 26: ...13 25 629 v03 Page 26 FIGURE 4 4 WIRING DIAGRAM 208 230 460V 60 Hz 306ECA546 B Ref Drawing Page 3 of 3...
Страница 27: ...13 25 629 v03 Page 27 FIGURE 4 5 WIRING DIAGRAM 380V 60 Hz 303ECA546 B Ref Drawing Page 1 of 3...
Страница 28: ...13 25 629 v03 Page 28 FIGURE 4 6 WIRING DIAGRAM 380V 60 Hz 303ECA546 B Ref Drawing Page 2 of 3...
Страница 29: ...13 25 629 v03 Page 29 FIGURE 4 7 WIRING DIAGRAM 380V 60 Hz 303ECA546 B Ref Drawing Page 3 of 3...
Страница 30: ...13 25 629 v03 Page 30 FIGURE 4 8 WIRING DIAGRAM 575V 305ECA546 A Ref Drawing Page 1 of 3...
Страница 31: ...13 25 629 v03 Page 31 FIGURE 4 9 WIRING DIAGRAM 575V 305ECA546 A Ref Drawing Page 2 of 3...
Страница 32: ...13 25 629 v03 Page 32 FIGURE 4 10 WIRING DIAGRAM 575V 305ECA546 A Ref Drawing Page 3 of 3...
Страница 33: ...13 25 629 v03 Page 33 Figure 4 11 WIRING DIAGRAM 230V 1 Phase 307ECA546 D Ref Drawing Page 1 of 4...
Страница 34: ...13 25 629 v03 Page 34 Figure 4 12 WIRING DIAGRAM 230V 1 Phase 307ECA546 D Ref Drawing Page 2 of 4...
Страница 35: ...13 25 629 v03 Page 35 Figure 4 13 WIRING DIAGRAM 230V 1 Phase 307ECA546 D Ref Drawing Page 3 of 4...
Страница 36: ...13 25 629 v03 Page 36 Figure 4 14 WIRING DIAGRAM 230V 1 Phase 307ECA546 D Ref Drawing Page 4 of 4...
Страница 39: ...13 25 629 v03 Page 39 Figure 4 15 PIPING AND INSTRUMENTATION ILLUSTRATION 301ECA797 01 Ref Drawing Page 1 of 1...
Страница 61: ...13 25 629 v03 Page 61 Figure 9 5 Compressor Module Hardware...