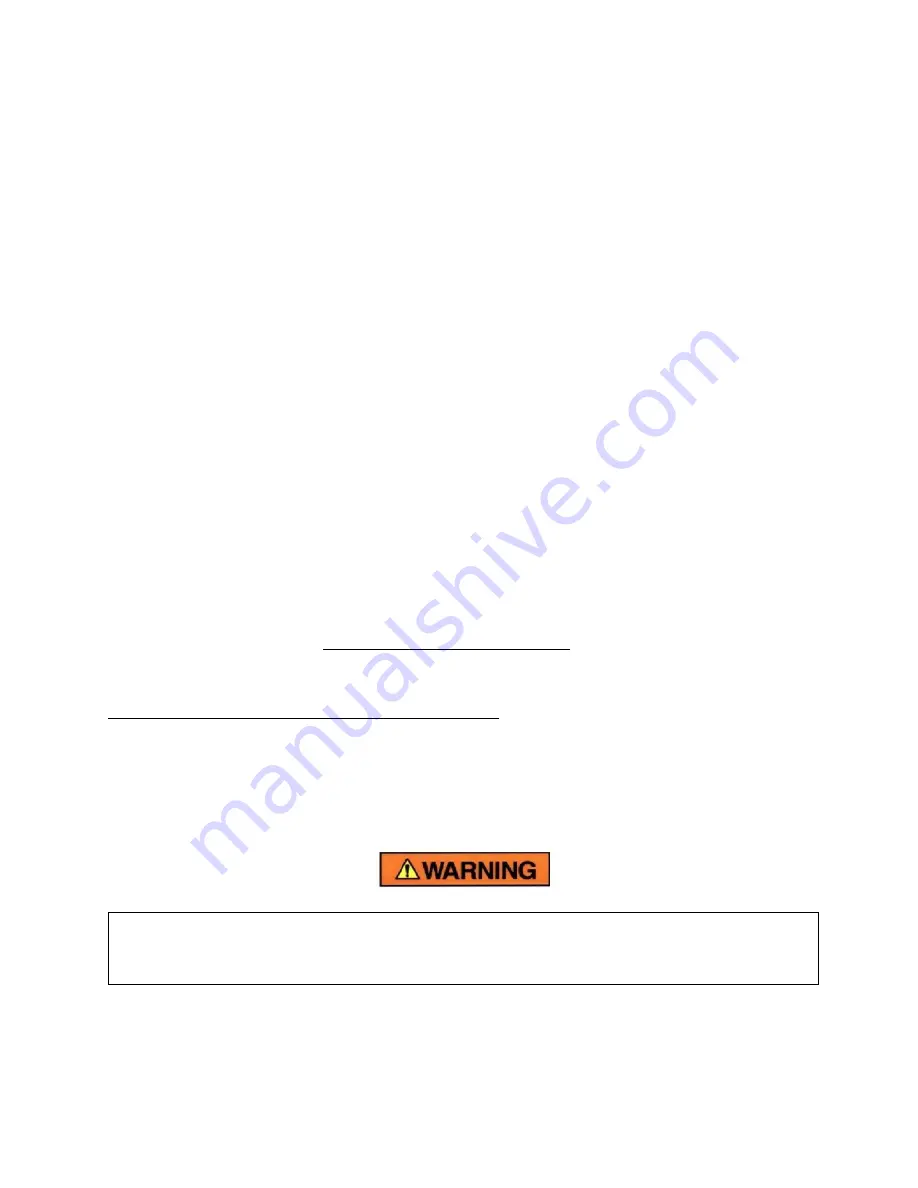
13-25-629 v03 Page 14
INSTALLATION FOR COLD WEATHER OPERATION
Figure 2-3, It is recommended that the unit be installed inside a shelter that will be heated to
temperatures above freezing (32°F, 0°C). This will eliminate many of the problems associated with
operating units in cold climates, such as freezing in control lines and downstream of the cooler.
Refer to Engineering Data Sheet 13-9-411 for the advantages of using the heat recovered from rotary
compressors. This heat recovery could easily pay for an adequate shelter for the unit.
When the unit must be installed in an outdoors installation and/or exposed to ambient temperatures below
freezing (32°F, 0°C), contact Gardner Denver for recommendations.
When using a Total System with a compressed air dryer option, refer to Section 10 for details.
Remember unsheltered (outside) installations should be avoided whenever possible. Installation next to
a heated building, where enough heat can be used to keep the compressor room above freezing, will
save many complications in the operation and installation of the unit.
AUXILIARY AIR RECEIVER
– When using the base compressor package, an auxiliary air receiver is not
required if the piping system is large and provides sufficient storage capacity to prevent rapid cycling.
When used, an air receiver should be of adequate size, provided with a relief valve of proper setting, a
pressure gauge and a means of draining condensate
OPTIONAL MOISTURE
SEPARATOR/TRAP
- The unit can be provided with an optional stand-alone
combination moisture separator and trap that is field-installed downstream of the after cooler.
CONTROL PIPING
- Control piping is not necessary since the rotary screw unit is factory wired and piped
for the control system specified.
INLET LINE
- The filter is close-coupled to the compressor intake flange, thus no inlet line is used or
recommended.
DISCHARGE SERVICE LINE
–
For a stand-alone compressor unit
, the discharge service line
connection is provided at the outlet of the field installed water separator, which in turn is located at the
lower right hand side of the after cooler core.
For a compressor unit integrated into the Total System
, the discharge service line connection is
provided at the outlet of the dryer bypass loop (when dryer options is furnished) or at the outlet of the
receiver vessel.
A hand operated valve, (air service valve) and a separate (swing-type) check valve must be installed
between the unit and the customer’s air system. If a fast operating valve such as a ball valve is used, it
must be closed slowly to give the intake valve time to shut and keep the discharge pressure from spiking.
The controller has an automatic start/stop sequence built in. You do NOT need
to close the air service valve. Closing the air service valve on start-up or prior to
shutdown will cause rapid cycling, and could cause a high pressure shutdown.
When piping two or more rotary screw units on a common discharge line, each unit shall be isolated by
the check valve in the unit discharge line.
If a rotary screw and a reciprocating compressor are piped to a common discharge line, an air receiver
must be located between the two units.
Содержание L4-5C
Страница 24: ...13 25 629 v03 Page 24 FIGURE 4 2 WIRING DIAGRAM 208 230 460V 60 Hz 306ECA546 B Ref Drawing Page 1 of 3...
Страница 25: ...13 25 629 v03 Page 25 FIGURE 4 3 WIRING DIAGRAM 208 230 460V 60 Hz 306ECA546 B Ref Drawing Page 2 of 3...
Страница 26: ...13 25 629 v03 Page 26 FIGURE 4 4 WIRING DIAGRAM 208 230 460V 60 Hz 306ECA546 B Ref Drawing Page 3 of 3...
Страница 27: ...13 25 629 v03 Page 27 FIGURE 4 5 WIRING DIAGRAM 380V 60 Hz 303ECA546 B Ref Drawing Page 1 of 3...
Страница 28: ...13 25 629 v03 Page 28 FIGURE 4 6 WIRING DIAGRAM 380V 60 Hz 303ECA546 B Ref Drawing Page 2 of 3...
Страница 29: ...13 25 629 v03 Page 29 FIGURE 4 7 WIRING DIAGRAM 380V 60 Hz 303ECA546 B Ref Drawing Page 3 of 3...
Страница 30: ...13 25 629 v03 Page 30 FIGURE 4 8 WIRING DIAGRAM 575V 305ECA546 A Ref Drawing Page 1 of 3...
Страница 31: ...13 25 629 v03 Page 31 FIGURE 4 9 WIRING DIAGRAM 575V 305ECA546 A Ref Drawing Page 2 of 3...
Страница 32: ...13 25 629 v03 Page 32 FIGURE 4 10 WIRING DIAGRAM 575V 305ECA546 A Ref Drawing Page 3 of 3...
Страница 33: ...13 25 629 v03 Page 33 Figure 4 11 WIRING DIAGRAM 230V 1 Phase 307ECA546 D Ref Drawing Page 1 of 4...
Страница 34: ...13 25 629 v03 Page 34 Figure 4 12 WIRING DIAGRAM 230V 1 Phase 307ECA546 D Ref Drawing Page 2 of 4...
Страница 35: ...13 25 629 v03 Page 35 Figure 4 13 WIRING DIAGRAM 230V 1 Phase 307ECA546 D Ref Drawing Page 3 of 4...
Страница 36: ...13 25 629 v03 Page 36 Figure 4 14 WIRING DIAGRAM 230V 1 Phase 307ECA546 D Ref Drawing Page 4 of 4...
Страница 39: ...13 25 629 v03 Page 39 Figure 4 15 PIPING AND INSTRUMENTATION ILLUSTRATION 301ECA797 01 Ref Drawing Page 1 of 1...
Страница 61: ...13 25 629 v03 Page 61 Figure 9 5 Compressor Module Hardware...