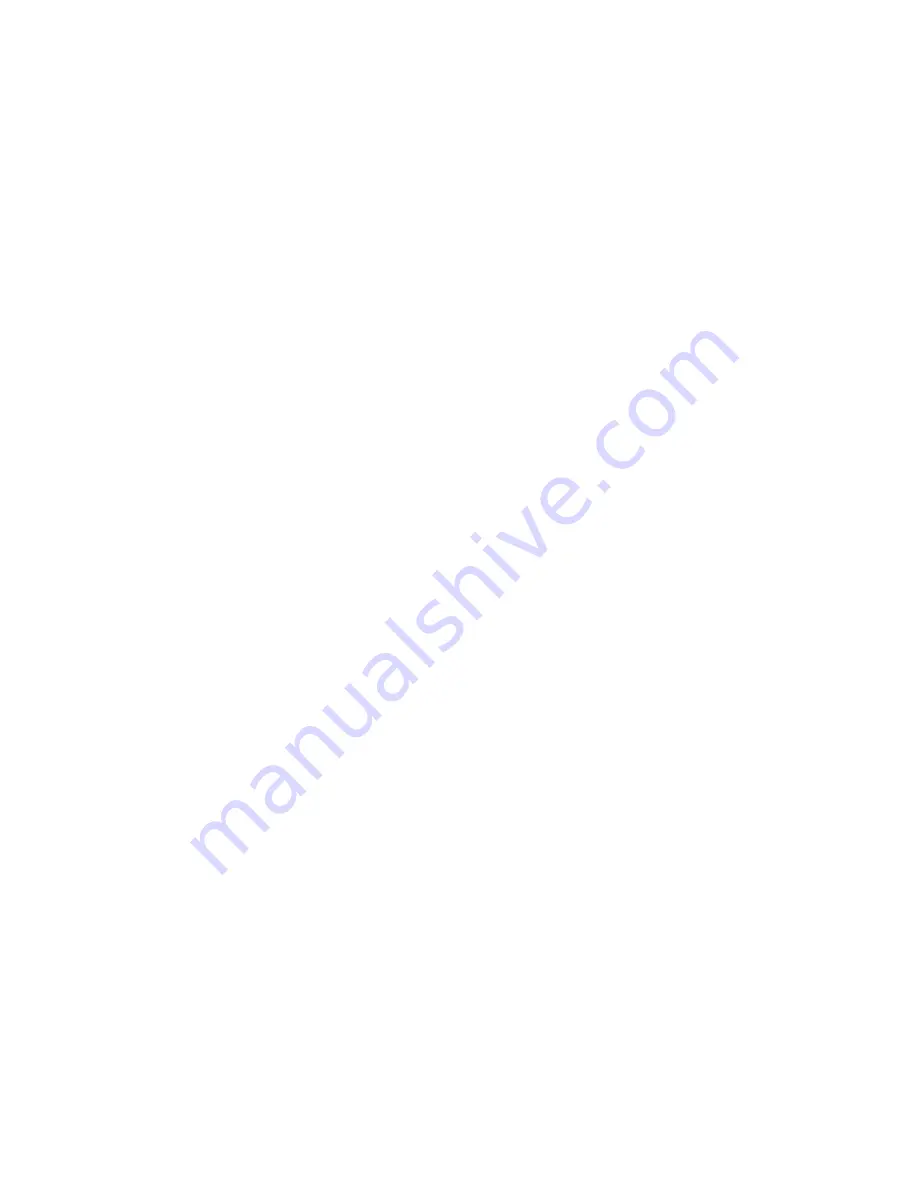
3-1-618 Page iii
TABLE OF CONTENTS
Maintain Pump Reliability and Performance with Genuine Gardner Denver Parts and
Support Services ........................................................................................................... i
Instructions For Ordering Repair Parts .................................................................................. i
Foreword............................................................................................................................... ii
Index..................................................................................................................................... iv
List of Illustrations ................................................................................................................. v
Section 1, Danger Notices..................................................................................................... 1
Section 2, Design, Description and Specifications ................................................................. 9
Section 3, Preparation, Operation and Maintenance.............................................................. 15
Section 4, Service Procedures .............................................................................................. 21
Section 5, Trouble-Shooting .................................................................................................. 28
Section 6, Rebuilding Data, Recommended Running Clearances and Torques ..................... 34
Warranty .......................................................................................................................... Last Page