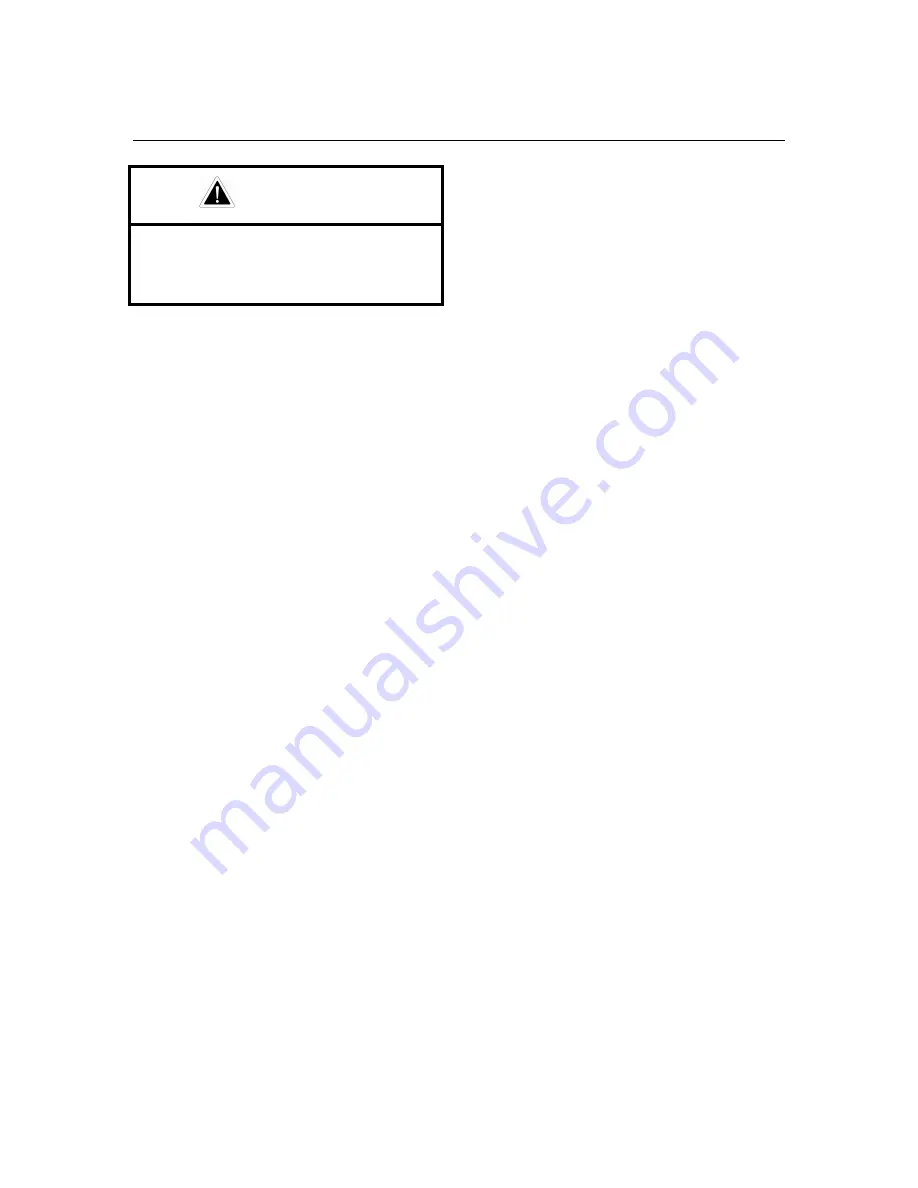
3-1-618 Page 15
SECTION 3
PREPARATION, OPERATION AND MAINTENANCE
DANGER
Read and understand clearly all
safety rules and precautions before
attempting to operate the pump.
This section deals with pump preparation
after shipping and storage of the pump, user
built
lubrication
system
and
its
specifications, pump break in procedures,
recommended oils, allowable crankcase
operating
tempera-tures,
viscosity
conversion tables, and routine maintenance
schedule.
PREPARATION AFTER SHIPPING AND
STORAGE
All pumps are shipped dry and therefore
must be flushed with light weight oil before
operating. The flushing must be performed
regardless of method or duration of the
shipment or type of container the pump was
shipped in.
Pumps are not prepared for storage and
should be put in service as soon as
possible.
If for any reason the pump has to be put into
storage after prior use, the following
procedure should be followed:
1.
Clean and flush the fluid end with a
rust preventative.
2.
Plug
all
discharge
and
suction
openings.
3.
Drain oil from the power end and the
gear reduction unit.
4.
Flush the power end with a rust
preventative (before flushing make
sure that the rust preventative will not
clog the oil passages).
5.
Remove the breather and either plug or
tape the opening.
6.
Coat the gear reducer input shaft and
all extension rods with a heavy rust
preventive.
7.
Plug drain holes at the bottom of the
pump frame, crosshead guide, gear
reducer transition and offset.
8.
Plug the lube inlets.
9.
Store the pump inside in a warm dry
place.
10. If the pump is shipped ocean cargo, it
must be crated in a water-tight contain-
er placed below the deck to prevent
rusting and salt water contamination.
PUMP MOUNTING INSTRUCTIONS
Follow this procedure to shim the feet of the
pump. This will require the use of (8) grade
8, 1”-8 hex head screws with lock washers
and nuts to secure the pump frame, and (4)
grade 8, 3/4”-10 hex head screws with lock
washers and nuts to secure the fluid end
supports.
1.
Set the pump in its location.
2.
Install one bolt in each of the two feet
at the rear corners of the power frame.
Snug but do not tighten these bolts.
3.
The fluid end support brackets should
be in their uppermost position, against
the bottom of the fluid end.
4.
Using a feeler gauge, check under the
two center feet at the rear of the frame
and the four at the front of the frame.
5.
Select
the
proper
number
and
thickness of shims to fill the gap under
the high foot.
6.
With shims in place (if required), install
bolts in the remaining six power frame
mounting feet.
7.
Tighten all eight bolts. Use the appro-
priate torque for the type of bolts.