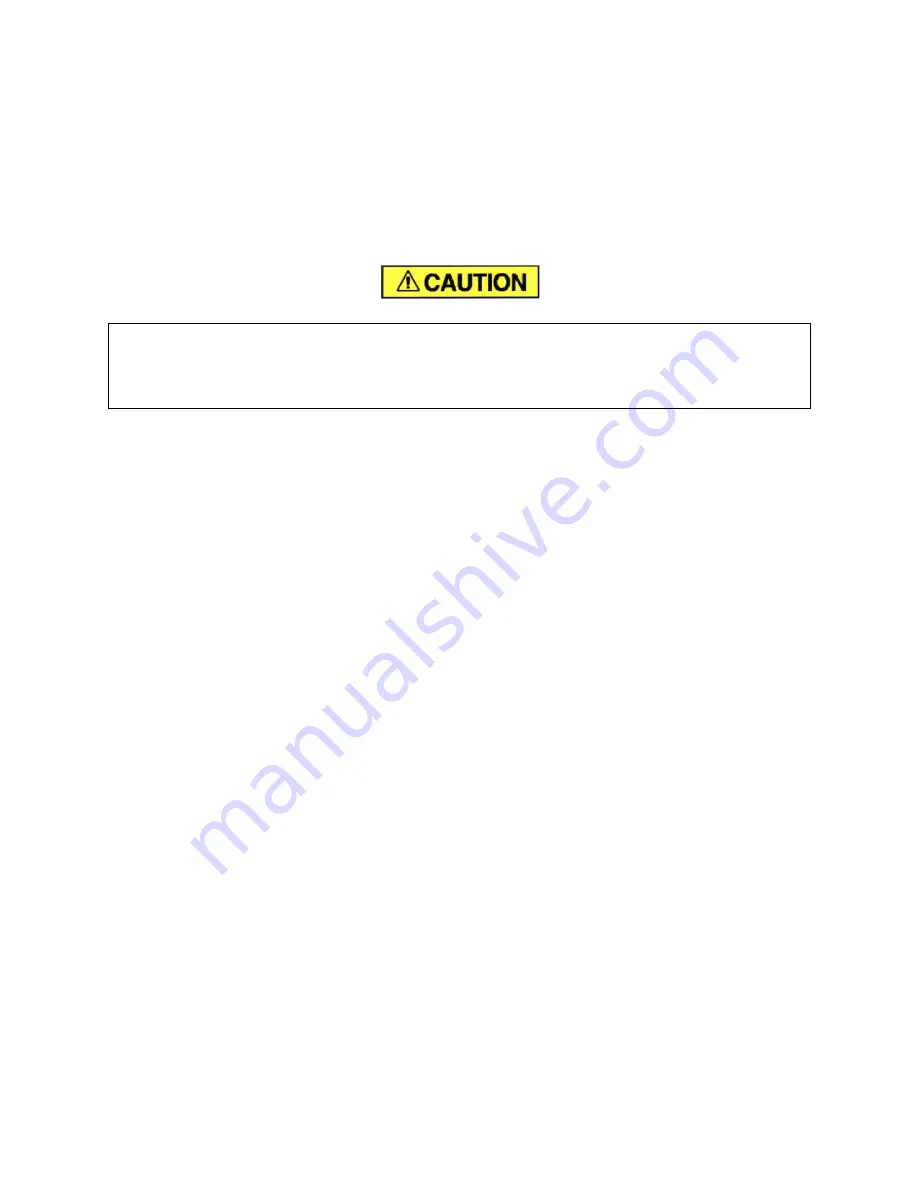
13-18-612 Page 51
5-5
COMPRESSOR OIL FILTER
- The oil filter is a vital part in maintaining a trouble-free compressor, since it
removes dirt and abrasives from the circulated oil. It should be replaced every 1000 hours of operation,
sooner if necessary due to dirty environment and when the oil is changed. (See Figure 1-3, page 10) and
Figure 1-5, page 12) for the location of the oil filter within the package.
A flow bypass valve, mounted inside the filter cartridge, provides uninterrupted oil flow when the filter
element is contaminated and its backpressure exceeds 29-36 psid (at typical operating conditions of
140
F and 100 psi). However, since this condition introduces unfiltered, potentially contaminated oil into
the compressor, it is best avoided by following the recommended filter replacement intervals.
Improper oil filter maintenance will cause damage to equipment. Replace filter element
every 1000 hours of operation. More frequent replacement could be required
depending on operating conditions. A filter element left in service too long may
damage equipment.
The filter media is contained within an easily replaced, spin-on cartridge. Use the following procedure to
replace the filter. Do not disturb the piping:
1. Be sure the unit is completely off and that the oil sump is depressurized.
2. Disconnect, lockout and tagout the power supply to the compressor package.
3. Close (when provided) valve isolating compressor package from air system.
4. Unscrew the cartridge with adequate tool (e.g., strap wrench) and remove.
5. Clean (wipe) and lubricate sealing surface on filter housing with grease.
6. Lubricate o-ring seal on new element with grease.
7. Screw new element onto filter head firmly
– approximately 3/4 turns after cartridge and head make
contact.
8. Open isolation valve (when provided), restore power, then run unit to check for leaks.
THERMOSTATIC OIL MIXING VALVE (FIGURE 5-3) (Electronic)
– This device mixes cold (from oil
cooler) and hot (bypassed) oil in order to achieve a compressor discharge temperature above the
saturation level of the water vapor contained in the compressed air
– thus avoiding water collection in the
oil system.
Содержание AirSmart VS80-110B
Страница 31: ...13 18 612 Page 30 4 5 Figure 4 2 PIPING AND INSTRUMENTATION ILLUSTRATION 300CGE797 A Ref Drawing...
Страница 33: ...13 18 612 Page 32 4 7 300CGE546 04 Ref Drawing Page 2 of 4...
Страница 34: ...13 18 612 Page 33 4 8 300CGE546 04 Ref Drawing Page 3 of 4...
Страница 35: ...13 18 612 Page 34 4 9 300CGE546 04 Ref Drawing Page 4 of 4...
Страница 37: ...13 18 612 Page 36 4 11 301CGE546 B Ref Drawing Page 2 of 4...
Страница 38: ...13 18 612 Page 37 4 12 301CGE546 B Ref Drawing Page 3 of 4...
Страница 39: ...13 18 612 Page 38 4 13 301CGE546 B Ref Drawing Page 4 of 4...
Страница 41: ...13 18 612 Page 40 4 15 302CGE546 05 Ref Drawing Page 2 of 4...
Страница 42: ...13 18 612 Page 41 4 16 302CGE546 05 Ref Drawing Page 3 of 4...
Страница 43: ...13 18 612 Page 42 4 17 302CGE546 05 Ref Drawing Page 4 of 4...
Страница 45: ...13 18 612 Page 44 4 19 303CGE546 B Ref Drawing Page 2 of 4...
Страница 46: ...13 18 612 Page 45 4 20 303CGE546 B Ref Drawing Page 3 of 4...
Страница 47: ...13 18 612 Page 46 4 21 303CGE546 B Ref Drawing Page 4 of 4...
Страница 70: ...13 18 612 Page 69 9 2 Figure 9 1 MINIMUM DISCHARGE PRESSURE CHECK VALVE...
Страница 86: ...NOTES...
Страница 87: ...NOTES...