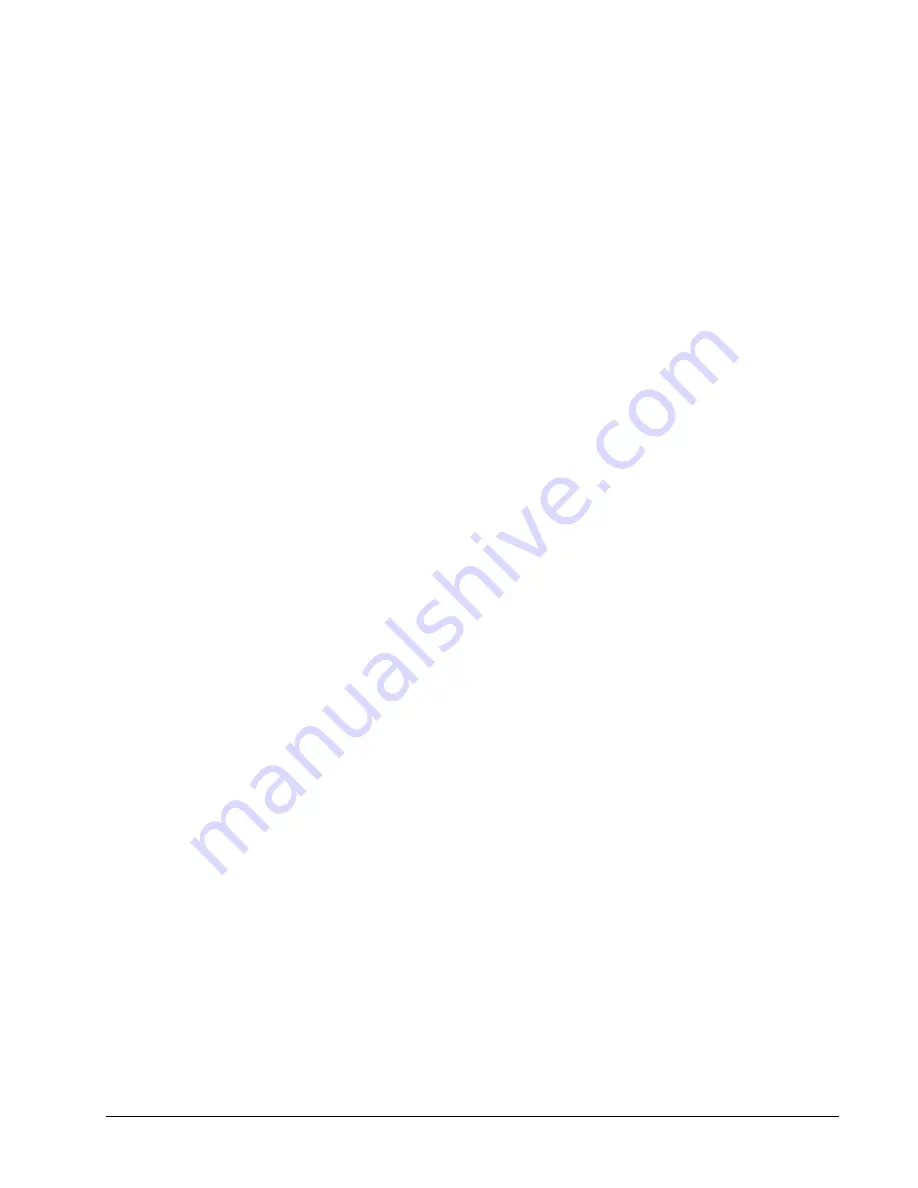
14
●
Chapter 2 Getting Started
DMC-18x2
At this point, if TPX does not vary with encoder rotation, there are three possibilities:
1.
The encoder connections are incorrect - check the wiring as necessary.
2.
The encoder has failed - using an oscilloscope, observe the encoder signals. Verify
that both channels A and B have a peak magnitude between 5 and 12 volts. Note
that if only one encoder channel fails, the position reporting varies by one count
only. If the encoder failed, replace the encoder. If you cannot observe the encoder
signals, try a different encoder.
3.
There is a hardware failure in the controller - connect the same encoder to a different
axis. If the problem disappears, you probably have a hardware failure. Consult the
factory for help.
Step E.
Connect Hall Sensors if available.
Hall sensors are only used with sinusoidal commutation and are not necessary for proper
operation. The use of hall sensors allows the controller to automatically estimate the
commutation phase upon reset and also provides the controller the ability to set a more
precise commutation phase. Without hall sensors, the commutation phase must be
determined manually.
Each set of sensors must use inputs that are in consecutive order. The input lines are
specified with the command, BI. For example, if the Hall sensors of the Z axis are
connected to inputs 6, 7 and 8, use the instruction:
BI ,, 6
or
BIZ
=
6
Step 8a. Connect Standard Servo Motors
The following discussion applies to connecting the DMC-18x2 controller to standard servo motor
amplifiers:
The motor and the amplifier may be configured in the torque or the velocity mode. In the torque
mode, the amplifier gain should be such that a 10 Volt signal generates the maximum required current.
In the velocity mode, a command signal of 10 Volts should run the motor at the maximum required
speed.
Step by step directions on servo system setup are also included on the WSDK (Windows Servo Design
Kit) software offered by Galil. See section on WSDK for more details.
Step A.
Check the Polarity of the Feedback Loop
It is assumed that the motor and amplifier are connected together and that the encoder is
operating correctly (Step B)
. Before connecting the motor amplifiers to the controller,
read the following discussion on setting Error Limits and Torque Limits. Note that this
discussion only uses the X axis as an example.
Step B.
Set the Error Limit as a Safety Precaution
Usually, there is uncertainty about the correct polarity of the feedback. The wrong
polarity causes the motor to run away from the starting position. Using a terminal
program, such as DMCTERM, the following parameters can be given to avoid system
damage:
Input the commands:
ER 2000 <CR> Sets error limit on the X axis to be 2000 encoder counts
OE 1 <CR>
Disables X axis amplifier when excess position error exists
Artisan Technology Group - Quality Instrumentation ... Guaranteed | (888) 88-SOURCE | www.artisantg.com
Содержание DMC-18 2 Series
Страница 3: ...Artisan Technology Group Quality Instrumentation Guaranteed 888 88 SOURCE www artisantg com...
Страница 5: ...Artisan Technology Group Quality Instrumentation Guaranteed 888 88 SOURCE www artisantg com...
Страница 11: ...Artisan Technology Group Quality Instrumentation Guaranteed 888 88 SOURCE www artisantg com...