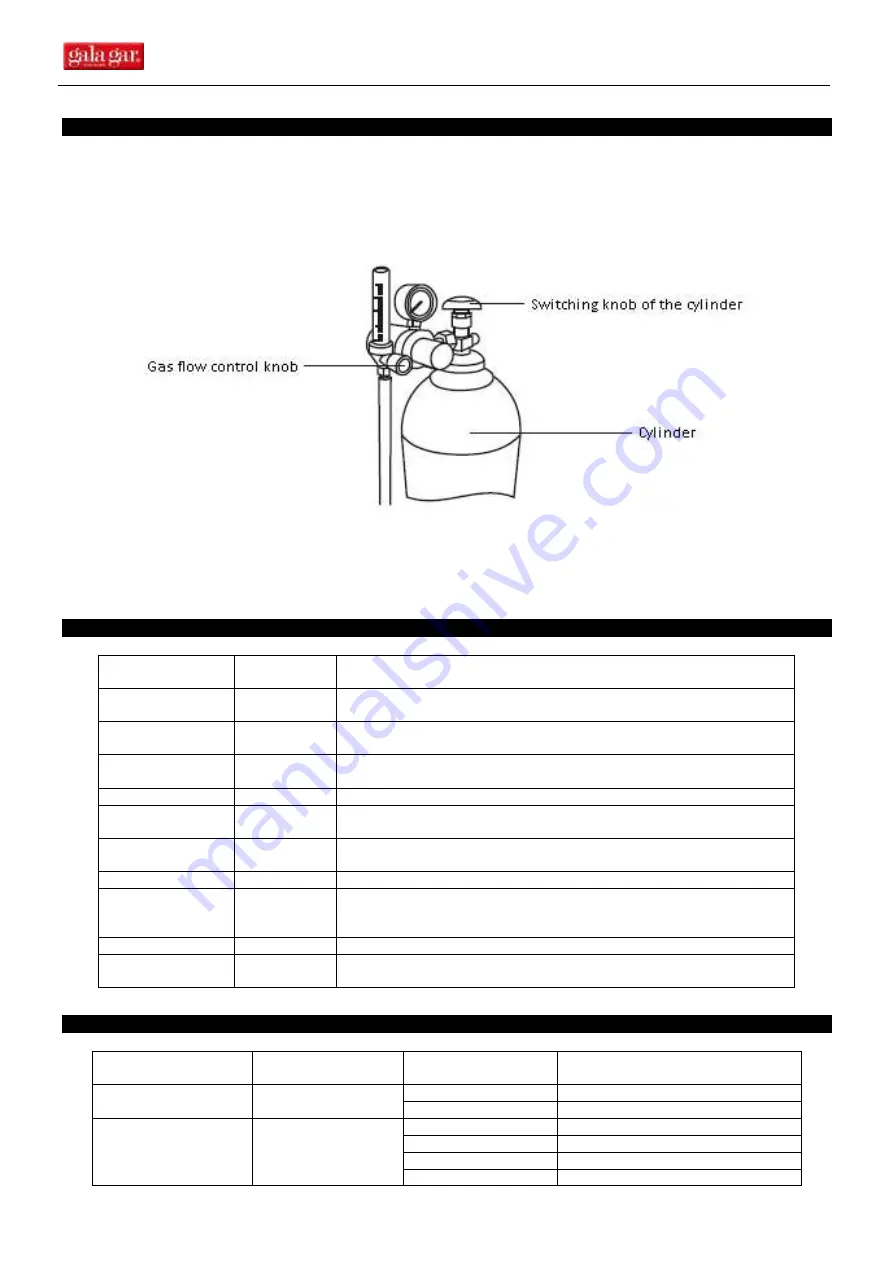
Smart 400 TIG Pulse
28
3.4 TIG OPERATION STEPS
Switch the welding mode switch on the front panel of the welding machine to “TIG” or “Pulse” position.
Turn on the power switch of the welding machine. Then, the cooling fan will work, and the current meter will
display the preset welding current.
Turn the gas-check/welding switch to “gas-check” position, and adjust the gas flow control knob on the gas
regulator to get the desired gas flow. After that, turn the gas-check/welding switch to “welding” position.
Select the proper operation mode via the 2T/repeating/4T switch according to the welding requirements.
Adjust the welding parameters to the appropriate values according to the welding requirements.
After the above steps are finished, welding can be carried out. The current meter will display the practical
welding current.
3.4.1 WELDING PARAMETERS FOR TIG WELDING
Adjustable
parameter
Adjusting
range
Description
Pre-flow time
0~15s
It is suggested to adjust it to 1s or an appropriate value according to
welding requirements.
Post-flow time
0~15s
It is suggested to adjust it to 1s or an appropriate value according to
welding requirements.
Initial current
5~100A
It is suggested to adjust it to a lower value or an appropriate value
according to welding requirements.
Up slope time
0~10s
To adjust the up slope time.
Welding current
5~400A
To adjust the welding current in DC TIG and to adjust the peak current in
pulse TIG.
Pulse duration ratio
10~90%
To adjust the percentage the peak current holding in a period in pulse TIG.
Please set it properly according to practical welding requirements.
Base current
5~400A
To adjust the base current in pulse TIG.
Pulse frequency
0.5~200Hz
To facilitate the users, the first half of the knob is low frequency range
within 0.2~10Hz, and the second half of the knob is high frequency range
within 10~200Hz.
Downslope time
0~10s
To adjust the downslope time.
Pilot arc current
5~400A
It is suggested to adjust it to a lower value or an appropriate value
according to welding requirements.
3.4.2 REFERENCE TABLE FOR WELDING PROCESS IN TIG
Electrode diameter
(mm)
Plate thickness (mm)
Maximum current (A)
Maximum gas flow (L/min)
1~2
1~3
50
5
50~80
6
2~4
3~6
80~120
7
121~160
8
161~200
9
201~300
10