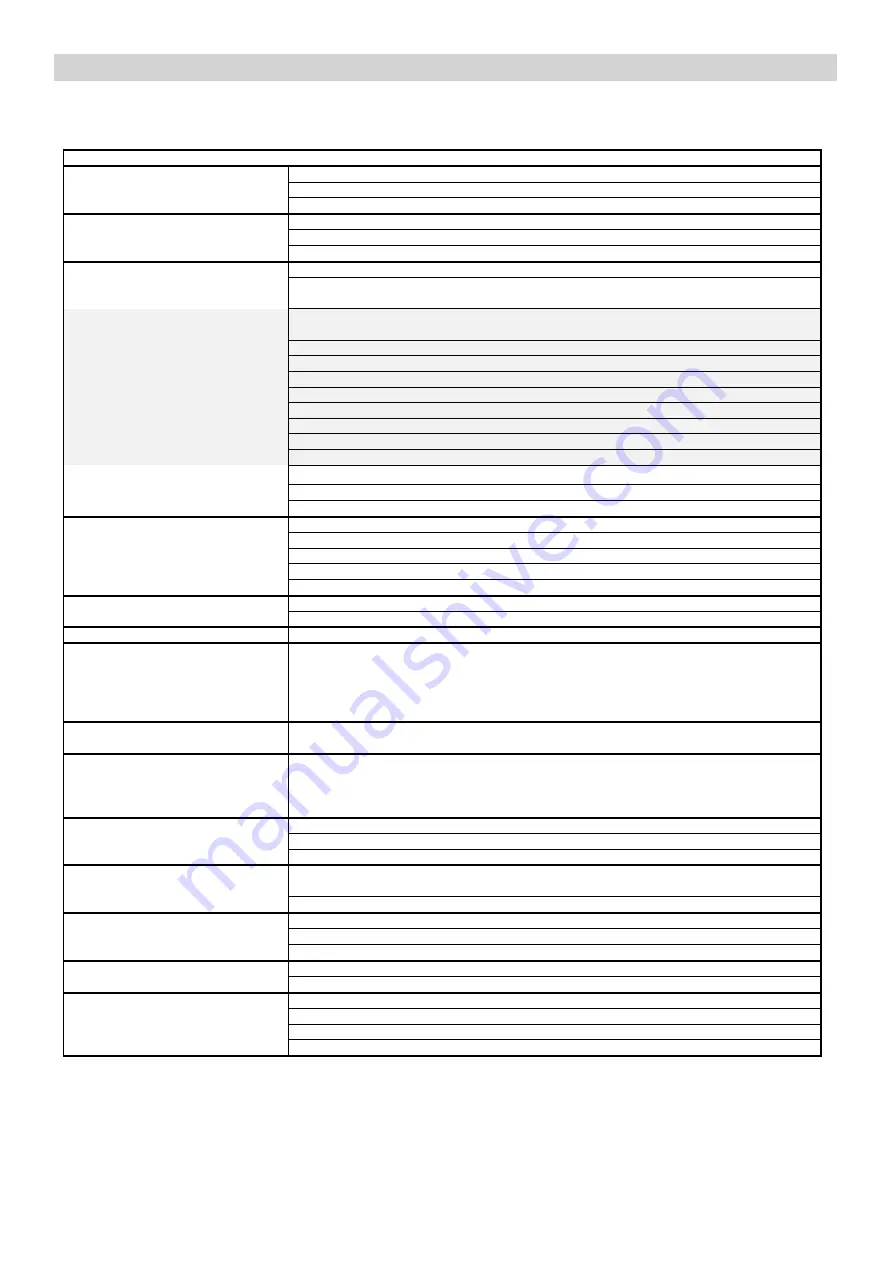
GAGGIA CADORNA 06 MACHINE REPAIR FLOW
1/1
6.1. Repair Flow
Proces stap
Saeco no.
Action
Intake
1 Visual inspection (transport damage)
take care for pictures
2 Check Type/serialnumber
3 Log all available accessory, counter check with info from consumer
Diagnosis
4
Check product for consumer complaint and main function
(NFF contact consumer)
5
Run Diagnostic to get error codes and relevant set statistics (EPSC) refer SDA_114585
6 Opening machine
Repair
7 Repairing the fault
(s)
encountered (view S
ervice information in EPSC)
8 Checking any modifications (view S
ervice information
, new software, etc.)
Refer
EPSC
9
Basic Functional test while the appliance is open
(linked to consumer complaint or what you may have
detected)
Coffee
Make e 2 cups at the same time. Are the volumes equal
- Crema
Blow on the coffee. Does the crema come back together
Is the crema colour correct (Hazelnut)
- Temperature
Is the coffee temperature within spec refer
chapter 2.1 of service manual
Steam
Does the steam work
Hot Water
Does the hot water work
Milk
(if applicable)
- Cappuccino
Does the cappuccinatore produce good froth
10 check water circuit for any leakage, such as Oetiker clamps, boiler and valve connection and hoses
11 Check mechanism for good movement and unexpected noise
12 Assembly
Inspection
13 Do cabinet parts fit well together
- visual
14 Check for damages
- Power check
15 Will the set switch on
- Accessories
16 Do the accessories match with the intake
- Consumer complaint
17 Check the product for the consumer complaint
Quick Functional test
18 Make 2 cups at the same time. Are the volumes equal
Coffee
19 Is the sound normal ?
Leakage
20 Did the product leak during the testing
Steam Out
21
Steam out
before shipping out, if temperature is below 0° to prevent any damaged due to frozen water.
No need for those families
:
Gaggia Velasca (Only 230V) and Babila (120-230V)
Please also check for GDA_113455
Reset Error code
22
New devices have the possibility to reset the error code, once captured it need to be reset to see if it
appear afterwards again
Claim Administration
23
Provide precise IRIS code, according dedicated code table for Garment Care products. The location code
from the part you have worked on MUST be completed always with the part reference from exploded
view !
Primary fault and corresponding IRIS code should be claimed first.
Cleaning
25 Clean water reservoir, bean reservoir, brew chamber and conveyor
26 Clean and dry brew unit, coffee bin and drip tray
27 External cleaning (housing surface)
Safety check
28 Earth leakage, Isolation test, resistor of earth wire grounding, as requested in certain country's (VDE, ISO)
or H-POT TEST
Visual
29 Check the mains cord for damages
Packing
30 Packing
31 Check completeness (accessories) according income log refer #3
32 Neatly pack the product
Documentation
33 Info for Consumer by packed ? e.g. service brochure, FAQ, NFF letter, s/c etc.…
34 Descaling instruction with changed procedure (S/C) if available
Repair report
35 Is there an answer to
ALL
consumer questions/complaints (see complaint)
36 add set statistic and give, if needed clear instruction towards consumer
37 Is it indicated which documents are added
38 Are there tips how to prevent issues
Coffee Service checklist UJ v34.xlsx
Repair Flow - Coffee
01.08.18
Содержание SUP 049
Страница 4: ...GAGGIA CADORNA CHAPTER 1 INTRODUCTION ...
Страница 7: ...GAGGIA CADORNA 01 INTRODUCTION 3 6 1 5 Electrical diagram ...
Страница 11: ...GAGGIA CADORNA CHAPTER 2 TECHNICAL SPECIFICATIONS ...
Страница 16: ...GAGGIA CADORNA CHAPTER 3 OPERATING LOGIC ...
Страница 23: ...GAGGIA CADORNA CHAPTER 4 TEST MODE AND STEAM OUT ...
Страница 29: ...GAGGIA CADORNA CHAPTER 5 ESPRESSO PHILIPS SERVICE CENTER ...
Страница 31: ...GAGGIA CADORNA CHAPTER 6 MACHINE REPAIR FLOW ...
Страница 33: ...GAGGIA CADORNA CHAPTER 7 DISASSEMBLY ...