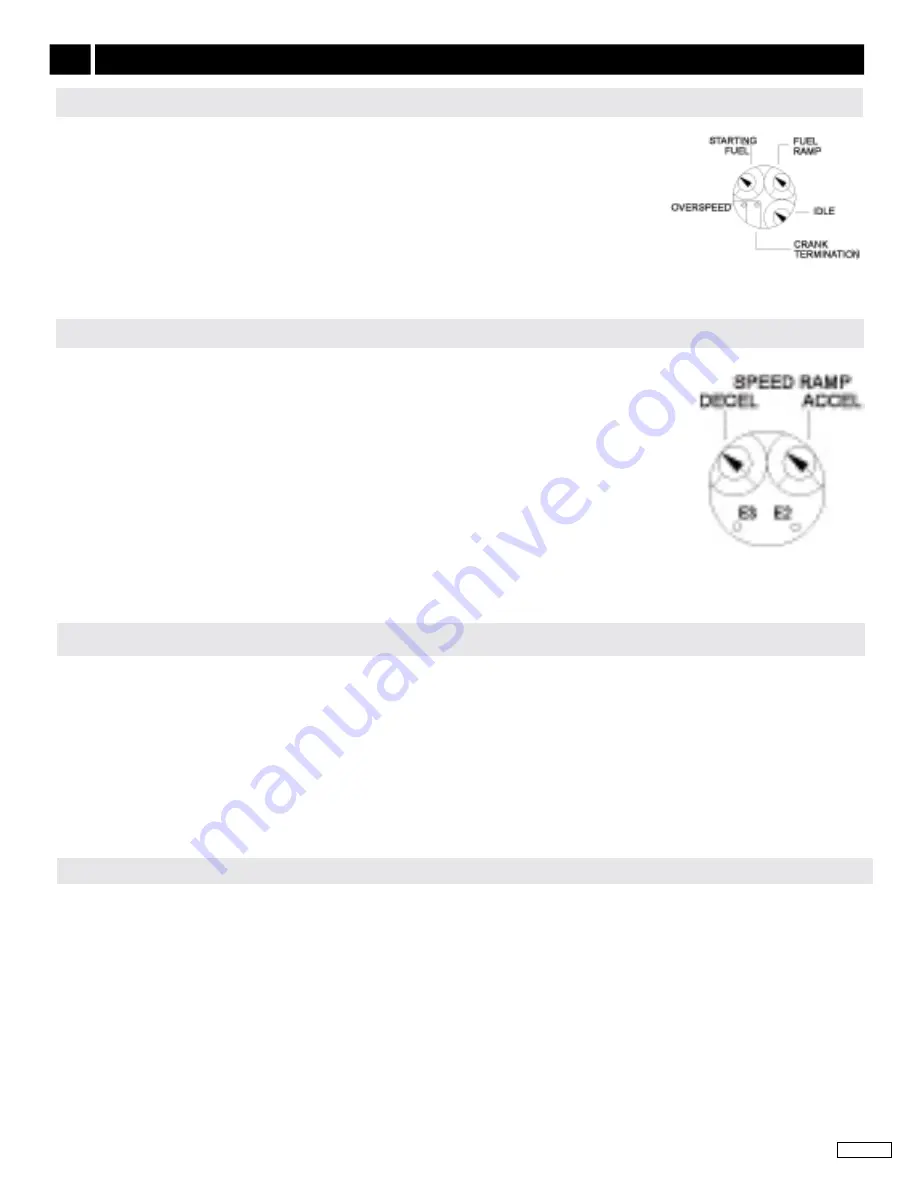
6
ESD5300 Speed Control Unit
09-2020-H
PIB1041
Governors America Corp. © 2020 Copyright All Rights Reserved
Turn the STARTING FUel to minimum CCW position (0).
Crank the engine and quickly rotate the STARTING FUel adjustment CW until the engine starts
without excess smoke. Repeat several times to find the best setting. Some engines require large
amounts of fuel to start but most modern engines respond to limited fuel during cranking.
Once the engine starts repeatedly in a satisfactory manner, adjust the FUel RAMPING adjustment
CW so the engine accelerates to rated speed quickly, without excess smoke. The acceleration
adjustment may be set to the fastest positions if start fuel ramping is not desired.
The eSD5340 has an advanced startup circuit that adjusts cranking fuel for faster startups.
STarTInG fUeL anD fUeL ramPInG aDJUSTmenT
ADDITIONAl FEATURES (CONTINUED)
9
To set idle and ramp speeds:
•
Close the IDle switch connecting Terminals N and P. This will cause the engine to slow to an
idle speed.
•
Adjust the IDle setting for desired idle speed.
•
Open the IDle switch between Terminals N and P. The engine will start accelerating toward
rated speed.
•
Adjust the ACCel control to allow the engine to accelerate with just enough fuel to bring the sys-
tem to operating speed with lowest emissions. The desired acceleration and deceleration rates
can be achieved by manipulating the ACCel and DeCel adjustments.
•
Cycle the IDle switch after each ACCel or DeCel adjustment change until the desired results
are achieved. Use an oil pressure switch to operate these contacts.
•
Open Terminals N and P and the engine speed will decelerate at a rate set by the DeCel control
CW is faster for both ACCel and DeCel functions.
IDLe anD ramP SeTTInG
each time the eSD5300 Series controller is started the speed ramping function operates by taking control of the engine at near idle po-
sition and automatically raises the engine speed until the speed set point is reached. The acceleration time is controlled by the acceler-
ation control. If the idle switch is then closed, the speed will decelerate at the rate set by the deceleration adjustment (DeCel) control.
During these ramping periods, the speed control has a small amount of droop added to attain stability at low engine speeds. The droop
is eliminated once rated speed is reached unless droop is added by closing the switch at Terminals J and K.
The internal ramp generator can also be used for a wide range variable speed applications.
•
To add variable speeds, connecting a 0-10 V DC variable voltage to Terminal N with respect to Terminal G.
•
To calibrate the speed range, either limit the voltage to a level which provides the desired range with an external potentiometer or
add resistance in series with Terminal N as shown in Section 4 Wiring.
InTernaL SPeeD ramPInG fUncTIon
The eSD5300 can operate with two distinct gain settings. The two gain adjustments, Gain 1 and Gain 2 are independent adjustments.
•
With the connection from Terminals R and l set Open, the Gain 1 adjustment is in operation.
•
With a connection from R to l set Closed, Gain 2 is in operation.
•
Switching between the two gain settings should have an imperceptible difference in speed change.
The dual gain function is especially useful for engines which exhibit different characteristics under different situations. An engine may
run very stable at high speeds and less stable at lower speeds. Setting a single gain control for the lower speeds then yields less than
an optimum setting at the higher speeds.
A simple switch can be toggled for low or high speed operation. Additionally in gaseous fuel engine applications where the quality or type
of gas is changed, the two gain settings can be used to idealize the governor for each type of fuel.
For cold engine instability, a temperature-sensing switch can reset the speed control gain once the engine has reached a normal operat-
ing temperature.
DUaL GaIn