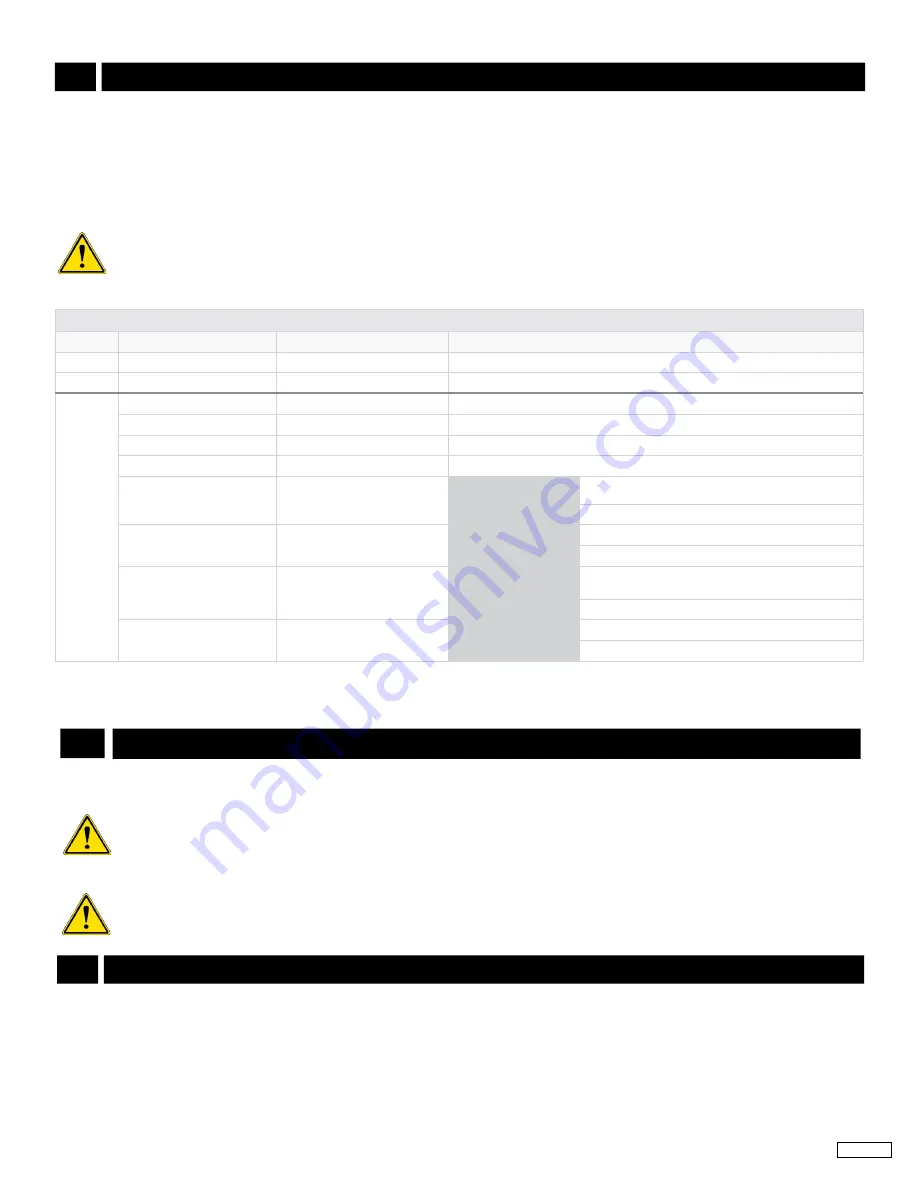
4
ESD5300 Speed Control Unit
09-2020-H
PIB1041
Governors America Corp. © 2020 Copyright All Rights Reserved
PRE-START SETUP
5
Before starting the engine, preset at minimum the following adjustments.
1. Set GAIN, STABIlITY, and external Frequency Trim (if used) are set to their mid point (50) positions.
2. Set STARTING FUel is set to 100 initially.
3. ensure Dip Switches SW2-5, SW2-6, and SW2-7 are set in their normal positions before starting the engine as shown in the DIP
SWITCHeS table below.
4. Set all other Dip SW2 switches (1 - 4) for optimum engine performance per the DIP SWITCHeS table. Take into account the factory
speed setting for the controller is 1400 Hz, or approximately set to idle speed. The crank termination is set very low initially.
*
When switch C2 is ON, the Soft Coupling feature is enabled.
**
SW2 Switches 5-8 must be set to match the actuator being used in the application. Contact GAC for questions.
DIP SWITcHeS
roW
SWITcH
fUncTIon
normaL PoSITIon
SW1
1
lead lag Circuit
OFF
2
Soft Coupling
OFF
SW2
1
DTC 8X
OFF
2*
DTC 4X
OFF
3
DTC 2X
OFF
4
DTC 1X
OFF
5**
(adjust with engine
stopped)
Speed loop Gain 4X
for actuator
Series
120, 225, 175, 275 = ON
335, 2001 = OFF
6**
Act loop Gain
(7 A MAX) (15 A Peak)
for actuator
Series
120, 225, 175, 275 = ON
335, 2001 = OFF
7**
Act loop Gain
(7 A MAX) (15 A Peak)
for actuator
Series
120, 225, 175, 275 = OFF
335, 2001 = ON
8**
Added DTC 11 ms
65 ms
for actuator
Series
120, 225, 175, 275 = OFF
335, 2001 = ON
6
START ThE ENgINE
If crank termination occurs too quickly preventing the engine from starting, turn the crank termination adjustment clockwise (CW). The
actuator should snap to full fuel until the engine starts and run at a low idle setting. Adjust the SPeeD setting CW for the desired oper-
ating speed. If the engine is still unstable, turn the GAIN and STABIlITY adjustments CCW until the engine is stable.
If the IDle speed adjustment is set too low, the engine may never exceed the crank termination point, possibly causing starter
damage.
If the system remains unstable or not operating properly, see SeCTION 10, System Troubleshooting.
Read this entire document before starting your engine.
7
gOVERNOR SPEED SETTINg
The governed speed set point is increased by clockwise rotation of the SPeeD adjustment pot. Remote speed adjustment can be ob-
tained with an optional 5K Frequency Trim Control. See Section 4, WIRING for more information.
Failure to set these dip switches may cause startup engine trouble. See Section 10, System Troubleshooting, SW2
SWITCH SeTTINGS FOR INSTABIlITY table for additional information.