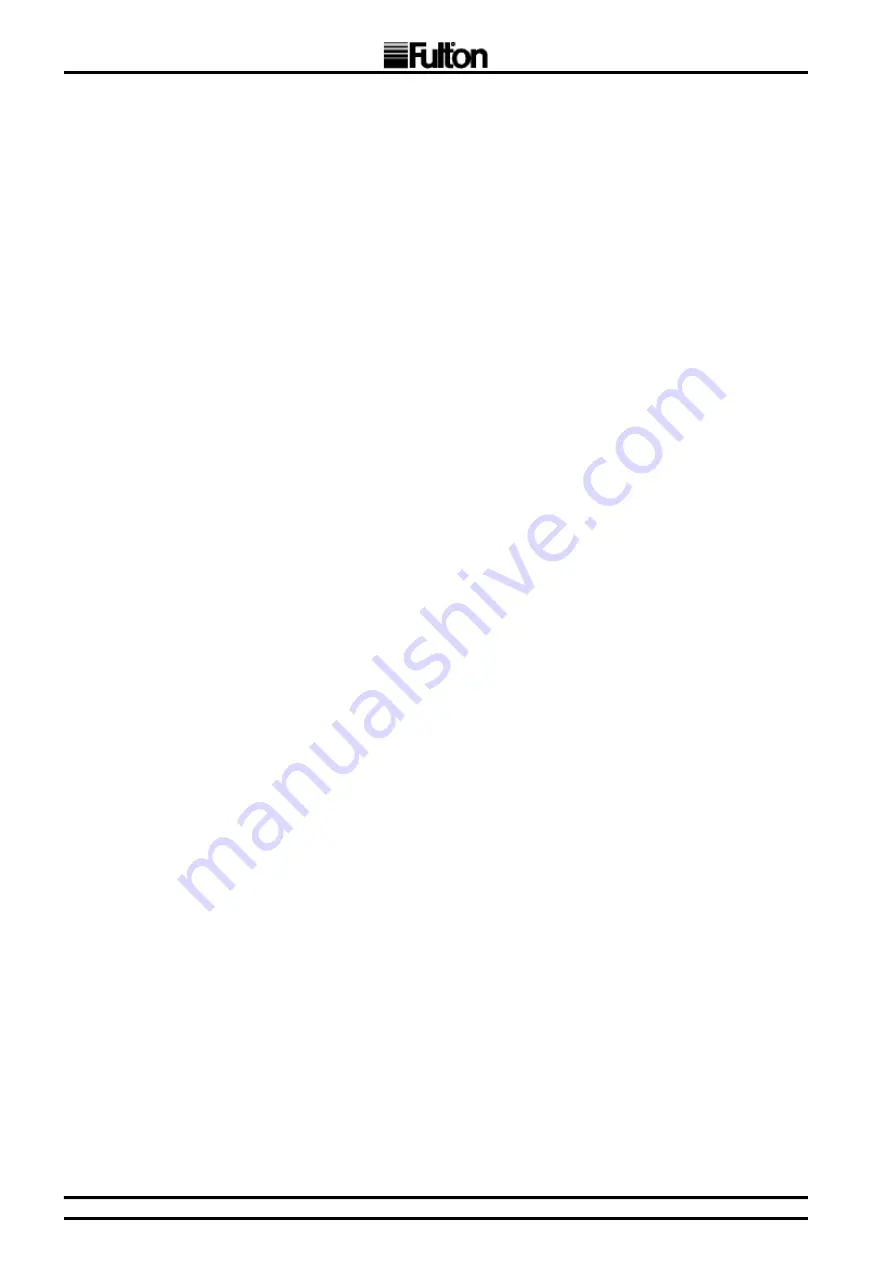
FT-C Vertical Electric Thermal Fluid Heater Manual 12 2013 ISSUE 1
Page 42
3
Oil Fired Burner
The following refers to the design and operation of the on/off burner utilising fuel oil which requires
no preheating. This burner is of high pressure, mechanical atomisation design.
The sequence of operation is as follows:
1) An oil pump is used to obtain necessary atomising pressure before the fuel oil reaches the
nozzle. The fuel oil is divided into fine particles in the nozzle and imparted with a rotating motion
before escaping from the nozzle as a cone of finely atomised oil.
2) Combustion air is supplied by a centrifugal fan. A damper provides throttling of the inlet
opening. The air from the fan reaches the burner head after going through a turbulator,
accomplishing correct distribution and mixture of air and atomised fuel oil.
3) An electric spark between two electrodes provides ignition of the atomised mixture, except
where code requires a gas pilot. This spark is produced by a high voltage transformer.
4) The flame programmer circuit controls normal operation of the burner. The sequence includes
purging of the combustion area for a set period, ignition and opening of magnetic valves on the
oil circuit; post-purge of combustion area and return to re-start position.
5) A scanner mounted on the burner casing and facing the light of the flame monitors the flame.
6) Safety lock out occurs within a preset minimum time in the event of insufficient, unstable or non-
existent flame. After fault has been corrected, reset programmer by depressing the reset button
on the casing of the burner control box.
7) Proper fuel pressure at the burner nozzle is essential. The correct firing rate is obtained by
setting the fuel oil pump to give the design pressure for each unit. This is done at the factory.
Pressure is measured by connecting a 0-25 bar (0-400 PSI) test pressure gauge to the gauge
connection on the fuel pump. The fuel pressure gauge indicates the pressure of the fuel at the
burner nozzle.
8) Typical pressures range between 12-22 bar (160-350 PSI). Note the correct setting upon
commissioning. Modulating units should have a second pressure gauge monitoring the
pressure in the return pipe from the burner. This gauge will indicate the variation of oil flow
caused by modulation of the burner. Gauge readings should be recorded at start-up and
checked periodically.
Содержание FT-0080C
Страница 38: ...FT C Vertical Electric Thermal Fluid Heater Manual 12 2013 ISSUE 1 Page 30...
Страница 80: ...FT C Vertical Electric Thermal Fluid Heater Manual 12 2013 ISSUE 1 Page 72...
Страница 85: ...FT C Vertical Electric Thermal Fluid Heater Manual 12 2013 ISSUE 1 Page 77 5...
Страница 86: ...FT C Vertical Electric Thermal Fluid Heater Manual 12 2013 ISSUE 1 Page 78 5...
Страница 87: ...FT C Vertical Electric Thermal Fluid Heater Manual 12 2013 ISSUE 1 Page 79 5...
Страница 88: ...FT C Vertical Electric Thermal Fluid Heater Manual 12 2013 ISSUE 1 Page 80 5...
Страница 90: ...FT C Vertical Electric Thermal Fluid Heater Manual 12 2013 ISSUE 1...