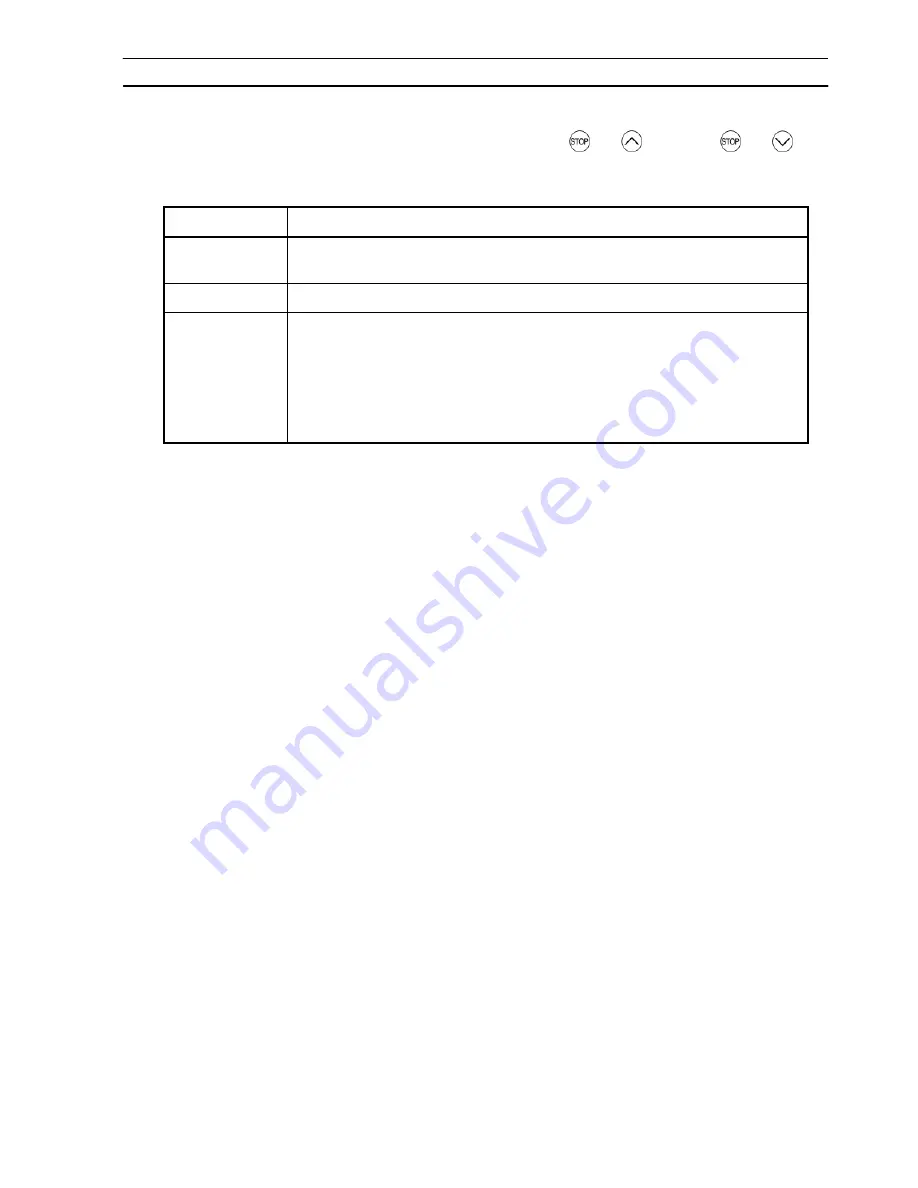
H03
Data Initialization
H03 initializes the current function code data to the factory defaults or initializes the motor
parameters.
To change the H03 data, it is necessary to press the
+
keys or
+
keys(simultaneous keying).
Data for H03
Function
0
Disable initialization
(Settings manually made by the user will be retained.)
1
Initialize all function code data to the factory defaults
2
Initialize motor 1 parameters in accordance with P02 (Rated capacity) and
P99 (Motor 1 selection)
Function codes subject to initialization: P03, P06 to P12 and constants for
internal control
(These function codes will be initialized to the values listed in tables on the
following pages.)
• To initialize the motor parameters, set the related function codes using the following steps.
1)
P02
Set the rated capacity of the motor to be used in kW.
Motor (Rated capacity)
2)
P99 Select the characteristics of the motor
Motor Selection
3)
H03 Data Initialization Initialize the motor parameters. (H03 = 2)
4)
P03 Set the rated current on the nameplate if the already set data
Motor (Rated current) differs from the rated current printed on the nameplate of the
motor.
• Upon completion of the initialization, the H03 data reverts to "0" (factory default).
• If the P02 data is set to a value other than the nominal applied motor rating, data
initialization with H03 internally converts the specified value forcedly to the equivalent
nominal applied motor rating (see the tables on the next page).
5-60