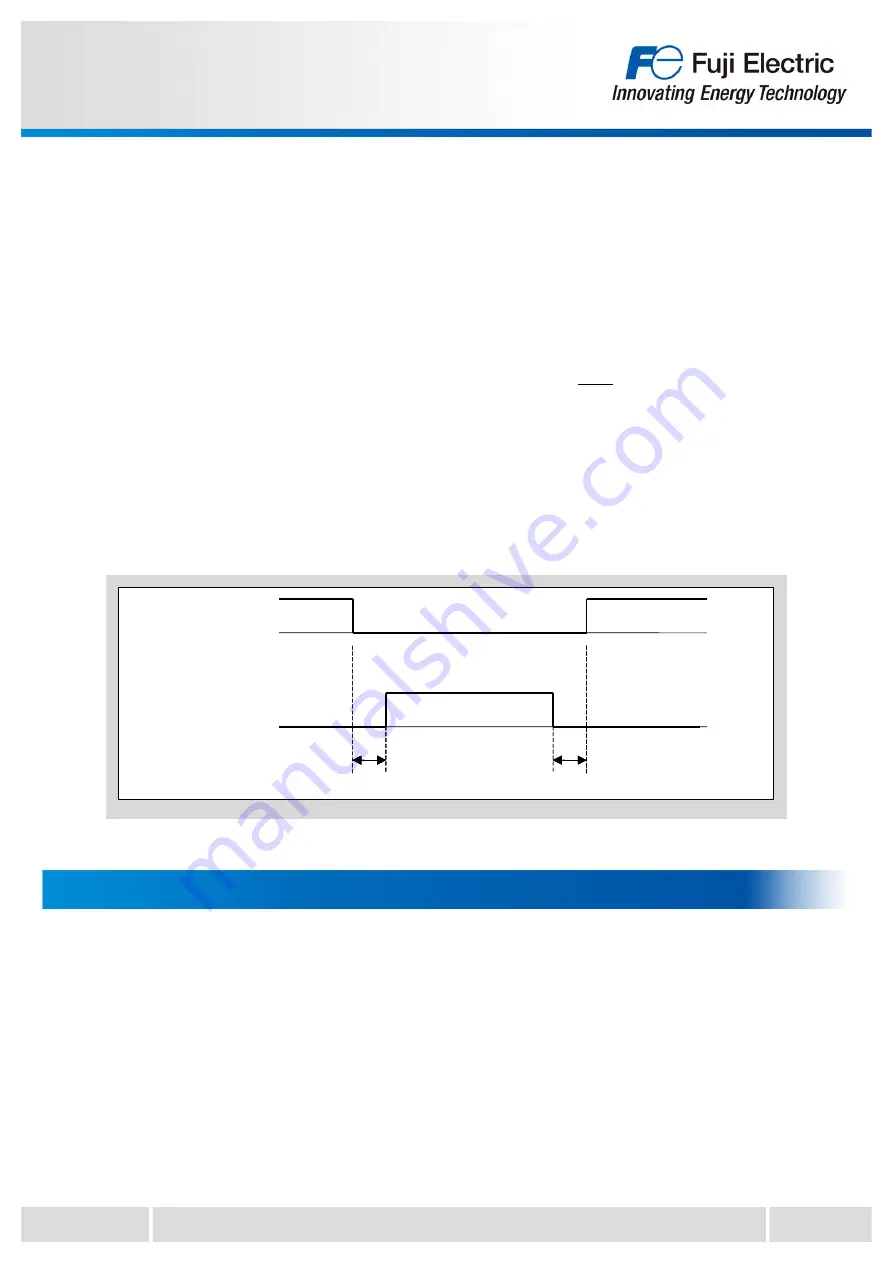
MT5F33743
© Fuji Electric Co., Ltd. All rights reserved.
5-8
So,
V
GE
is generated between gate to emitter. If
V
GE
is excess the sum of reverse biased
voltage and
V
GE(th)
, IGBT
2
is turned on. Once IGBT
2
is turned on, the short-circuit condition is
happened, because both IGBT
1
and IGBT
2
is under turned-on state.
Based on this principle, several measures have been devised as methods for avoiding the
unexpected turn-on for the IGBT. These include adding a capacitance
C
GE
component between the
gate and the emitter, increasing -
V
GE
, and enlarging the gate resistance
R
G
. The effect of these
measures varies depending on the applied gate circuit. Therefore, only apply them after sufficiently
confirming your configuration. In addition, also confirm whether there is any impact on switching loss.
4.4 Dead time setting
For inverter circuits and the like, it is necessary to set an on-off timing delay (dead time) in order to
prevent short circuits. During the dead time, both the upper and lower arms are in the OFF state.
Basically, the dead time (Fig. 5-10) needs to be set longer than the IGBT switching time (
t
off
max.).
For example, when
R
G
is increased, switching time also becomes longer, so it would be necessary to
lengthen dead time as well. Also, it is necessary to consider other drive conditions and the
temperature characteristics.
It is important to be careful with dead times that are too short, because in the event of a short circuit
in the upper or lower arms, the heat generated by the short circuit current may destroy the module.
Therefore, appropriate dead time should be settled by the confirmation of practical machine.
Fig. 5-10 Dead time timing chart
Dead time
Lower arm
Gate signal
Dead time
H
L
H
L
ON
ON
ON
OFF
OFF
OFF
Upper arm
Gate signal
In high capacity inverters and other equipment that needs to control large currents, it may be
necessary to connect IGBT modules in parallel. When connected in parallel, it is important that the
circuit design allows for an equal flow of current to each of the modules. If the current is not balanced
among the IGBTs, a higher current may build up in just one device and destroy it. The electrical
characteristics of the module as well as the wiring design, change the balance of the current between
parallel connected IGBTs. In order to help maintain current balance it may be necessary to match the
V
CE(sat)
values of all devices.
Also, when the IGBT module has the cooler with the water jacket, it is necessary to adhere strictly to
specifications such as water temperature, water flow and pressure within each water jacket.
For more detailed information on parallel connections, refer to Chapter 10 of this manual.
5. Parallel Connections