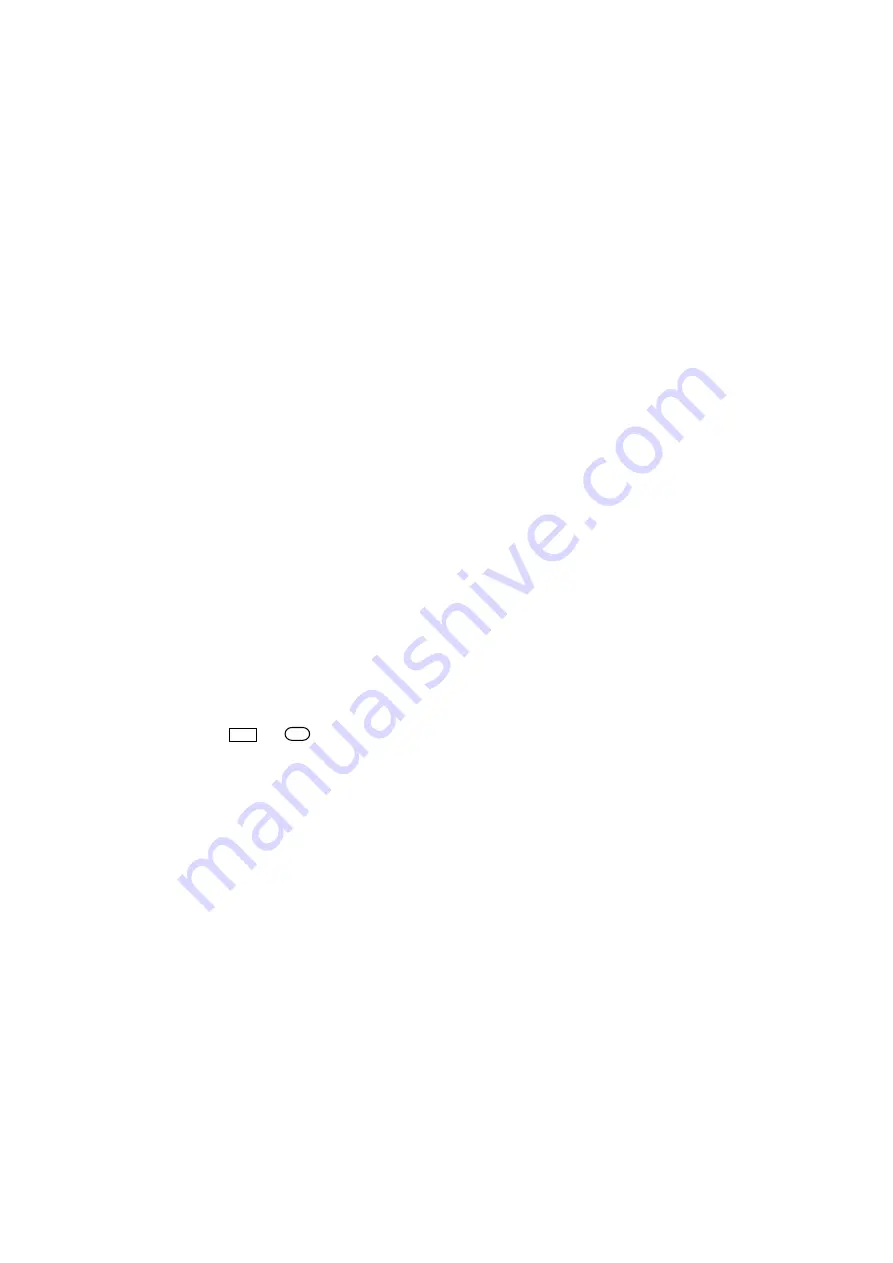
2-15
(*1) Install a recommended molded case circuit breaker (MCCB) or residual-current-operated protective device
(RCD)/earth leakage circuit breaker (ELCB) (with over current protection function) in the primary circuit of the
inverter to protect wiring.
(*2) Even if this terminal is not connected, the inverter can be operated with connection of the main circuit (L1/R, L2/S,
L3/T).
Please wire for this terminal to operate the control circuit of the inverter when there is no power supply.
(*3) When connecting an optional DC reactor (DCR), remove the jumper bar from the terminals P1 and P(+). The direct
current reactor (DCR) is a separately installed option.
(*4) Use the inverter connecting the power system which has earthed neutral-point. In case of non-earthed system (ex.
I-T NET), the control interface of the inverter becomes basic insulation, thus do not connect SELV circuit from
external controller directly.
(*5) For the control signal wires, use shielded or twisted wires. Ground shielded wires. To prevent malfunction due to
noise, keep the control circuit wiring away from the main circuit wiring as far as possible (recommended: 10cm or
more), and never lay them in the same wire duct. When crossing the control circuit wiring with the main circuit wiring,
lay them at right angles.
(*6) To bring the inverter into compliance with the European electrical safety standard IEC/EN 61800-5-1 or compliance
with Canadian and U.S. standards (CSA certification), be sure to insert the specified fuse (see Instruction Manual) in
the primary circuit of the inverter.
(*7) Connection terminal depends on SOURCE/SINK setting by slide switch SW1. Connect to (PLC) terminal when
SOURCE is set, and to (CM) terminal when SINK is set.
(*8) When the Enable inputs (EN1, EN2) function is not to be used, keep terminals [EN1]-[PLC] and [EN2]-[PLC] short
circuited using jumper wires. For opening and closing the hardware circuit between terminals [EN1] and [PLC] and
between [EN2] and [PLC], use safe relay device approved according to EN ISO 13849-1 PL-e, IEC/EN 61800-5-2
SIL3 or EN81-1 and EN 81-20.
(*9) Wiring must use shielded lines. Please connect the shield appropriately according to the specification of the encoder
and the connection with the controller. In the above figure, the shield is connected with the earth line of the inverter
side and not connected on the motor. It is likely to be improved by connecting the inverter side with (CM) when
malfunction occurs due to noise etc. When the wiring between the encoder and the inverter is long, the allophone
and the torque ripple might be generated because the signal from the encoder malfunctions by interfering with A
phase and B phase. In this case, please execute measures such as; wiring shorter cable, cable of smaller stray
capacitance, etc.
(*10) The encoder interface is provided by an option card.
(*11)
and are separated and insulated.
(*12) CAN signals are isolated from other internal circuit.
0V
0V
Содержание FRENIC-Lift LM2A Series
Страница 4: ...ii ...
Страница 16: ...xiv Product warranty ...
Страница 19: ...xvii MEMO ...
Страница 48: ...6 2 Terminal blocks Check that the terminal blocks are not damaged Visual inspection No abnormalities ...