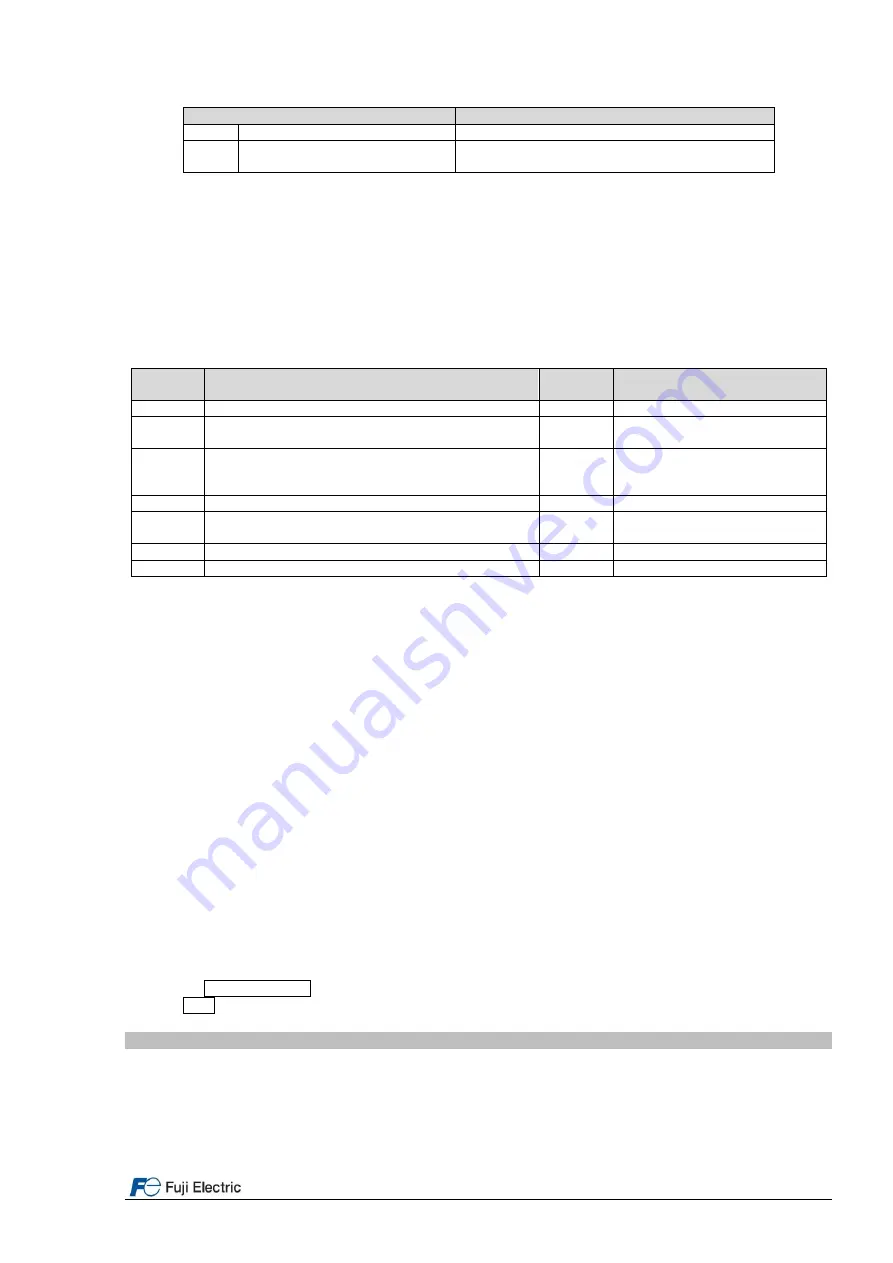
Page
20
of
28
Fuji Electric Europe GmbH
Table 9.1: Initialization types
Initialization type
Function
0
Disable initialization
Does not initialize. Data set by the user is kept.
3
Vector control for IM (open loop)
Initialize all function code data to settings suited
for open loop control for IM.
Default control mode in LM2C is Torque vector control (F42=2). V/f control is available as well when F42=3. In
V/f control slip compensation (P12) is not active, therefore the stopping level of the lift car might be dependent
on the car load.
8.2 Specific setting
Motor parameters, in other words motor name plate, have to be set manually. Table 9.2 shows the basic setting that
needs to be set. Parameters has to be set in the same order shown in the table below, otherwise a malfunction may
occur.
Table 9.2. Basic setting for induction motors (IM).
Function
Meaning
Factory
setting
Comments
P01
Motor poles.
4
Depends on the motor.
F03
Motor’s rated speed.
Normally F03 is motor speed at nominal lift speed.
1450 rpm
F04
Motor’s synchronous speed.
For 4-pole motors (50Hz) is 1500 r/min, for 6-poles
motors (50Hz) is 1000 r/min.
1500 rpm
Depends on the motor.
F05
Motor rated voltage.
V
Depends on the motor.
F11
Overload detection level.
A
Set manually same value than
P03.
P02
Motor rated power (kW).
kW
Depends on the motor.
P03
Motor rated current.
A
Depends on the motor.
8.3 Auto tuning procedure
After inverter initialization and motor parameters setting, an auto tuning has to be performed. Auto tuning will get
special data from the motor like no-load current (P06), stator resistance (P07), stator inductance (P08) and slip
frequency (P12).
In order to perform an auto tuning follows below step by step procedure:
1.
Please set the functions described in the table 9.1 and 9.2.
2. Set function P04 to 3 and press SET.
3. Give RUN command to the inverter from the lift controller (normally INSPECTION mode). Keep the RUN
command until inverter indicates that the procedure has been finished. At this point, the main contactors will be
closed and current will flow through the motor producing some acoustic noise. This procedure will take some
seconds. After this auto tuning procedure is finished.
If during the procedure inverter trips Er7 make sure that setting specified in table 9.1 and 9.2 is correctly set. Make
sure as well of the connection recommended on chapter 5. Connections. If too high no-load current is recognized, try
auto tuning mode 2 (P04=2).
After that, please give RUN command from the lift controller (for example in INSPECTION), and check that motor is
turning without any problem. Check that the output current has reasonable value. By a reasonable value it is
understood below rated current (empty car going down for example).
TP-A1-LM2: PRG > 3 > 2 [6/6]
TP-E1U: 4_17
9. Setting the speed profile
The setting of the speed profile includes:
Travelling speed
Acceleration and deceleration times (s)
S curves (%)
For the rated speed, each intermediate speed and creep speed the acceleration, deceleration times and S curves can
be set independently. Acceleration and deceleration times are referred to maximum speed (F03), in other words, the