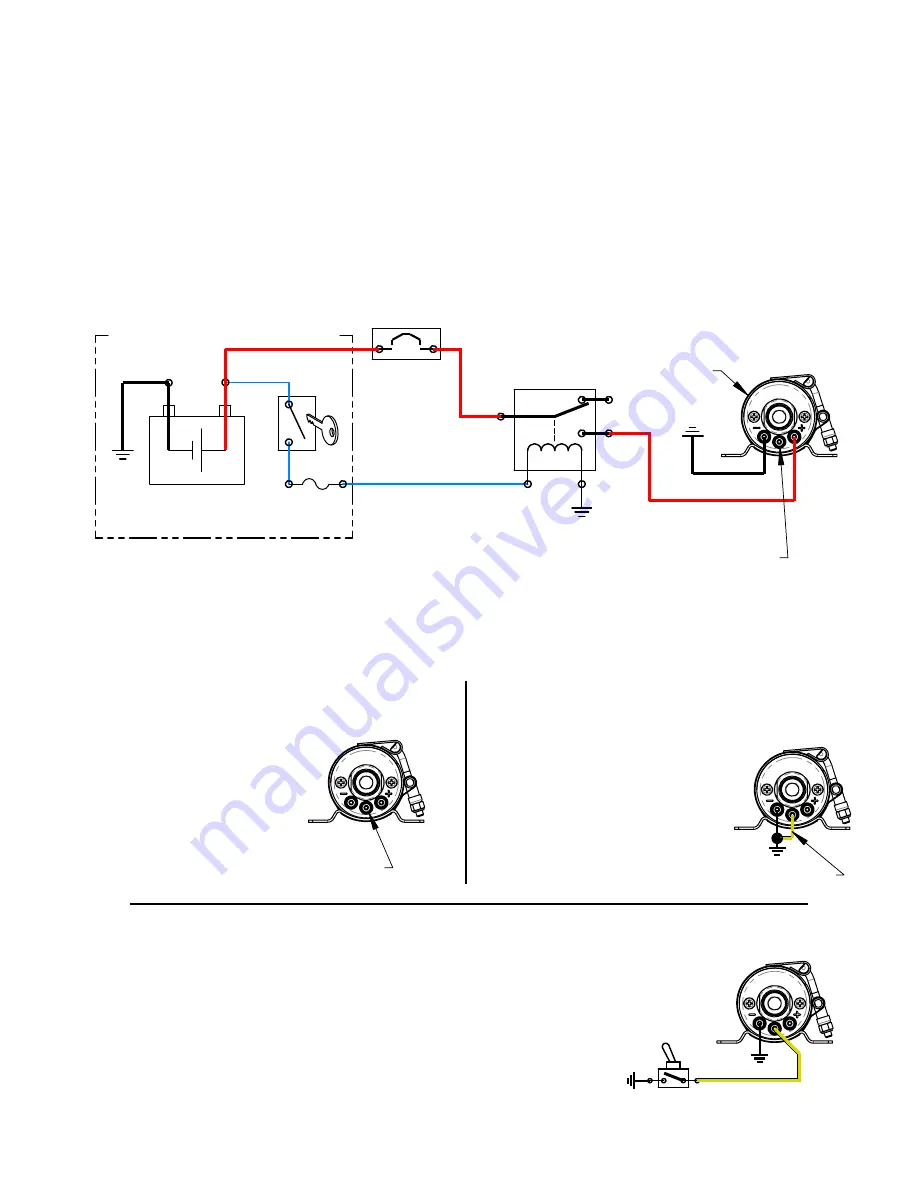
Electrical Planning Notes:
Reference Sheet 3 and 4 for schematic wiring diagram examples. Use electrical components as described
including electrical connectors that are appropriate for the operating environment of the fuel system, whether its use
in street, racing, or marine applications. Electrical connectors for the power leads must be capable of high current
draw, note all connections, wire, and component rating requirements herein. Solder and use shrink wrap for wire
splices for extra reliability (unless high quality crimping is performed). Use of a check valve in fuel system as
shown in plumbing diagram will maintain fuel pressure at normal levels during engine starting and may be required
depending on the wiring of main relay control circuit. (OEM and some aftermarket ECMs have fuel pump relay
control outputs that will turn off fuel pump during engine starting, requiring check valve use.) If the fuel pressure
does not maintain during engine starting, ensure fuel pump is energized while starting. Main wiring schematic
diagram below shows the control of relay by ignition switch. This source can be changed as described, or by a
toggle switch. Some forms of racing have specific rules regarding electrical switching of fuel pump. Consult
appropriate racing guidelines, rules, and regulations.
MAIN WIRING SCHEMATIC DIAGRAM:
(Some electrical components shown are not supplied with kit)
PUMP OPERATES
AT MAXIMUM SPEED
WITH SWITCH POSITION
SHOWN (OPEN).
NO JUMPER WIRE
OR DEVICE
NO
FUSED
NC
+
C
(1-5A)
SWITCH
or ECM
CIRCUIT
(8-10ga)
(16-20ga)
(12-24 Volt System)
-
IGNITION
VEHICLE BATTERY
VEHICLE ELECTRICAL SYSTEM
FUEL PUMP
POWER RELAY
(40+A Rating)
CIRCUIT
BREAKER
or FUSE
(40A)
(16-20ga) Device or Circuit can be used as shown below,
for proper operation.See Speed Control Schematic Diagrams
for wiring of speed control (Yellow Lug).
Fuelab Model:
42402-c
FUEL PUMP
JUMPER WIRE
SPEED CONTROL SCHEMATIC DIAGRAMS:
shown on the pump certification.
Attach no wiring to speed control terminal, to operate
interval use. Use in continuous
specific applications, or short
pump at continuous maximum speed. The performance
See schematic, attach wire between
speed control terminal has greater than 1.65V (Approx), the mode of operation is in continuous maximum speed. A
operating with low engine
maximum speed only while
flow rate at reduced speed is
adequate for application. Using
this mode of operation is
considered continuous duty.
See Examples 3 and 4 for
switching between maximum
Example 3: Switch to Ground Speed Changing
Example 1: Continuous Maximum Speed
Speed”. Use Example 1 for racing
pulsed signal may also be used to control pump speed. See examples below for a method suitable for your application.
terminal has less than 0.25V (Approx) applied to it, the mode of operation is in continuous reduced speed. When the
Example 2: Continuous Reduced Speed
demand for extended periods.
Yellow Lug. Use Example 2 if the
negative terminal (Black Lug) and
The speed control terminal (Yellow Center Lug) can have voltage or a signal applied to it. When the speed control
curve was recorded as shown on the
Pump Certification as “Maximum
and reduced speed.
cooling may be required using
damage fuel pump. Additional
heating and therefore may
maximum speed may cause over-
Attach a jumper wire as shown below, to operate
pump at continuous reduced speed. The reduced
speed is preset, with the performance curve
Attach switch and wiring as shown to the right, to operate pump at
continuous maximum speed while switch is in the open position
(position as shown in diagram). When the switch is in the closed position
(on), the pump will operate in reduced speed mode. To reverse the
desired switch action, refer to Example 4. Switch type can be a relay or
switching based on pressure or other means. Current draw through this
circuit is extremely low (much less than 1 amp), so a very low current rating
for this switch can be used. Use the diagram to the right as a guide to
properly wire this example. Reduced speed is recommended during long
periods of low engine fuel demand conditions to avoid fuel system heat
build-up.
110020274-1, Rev E Sheet 3 of 6