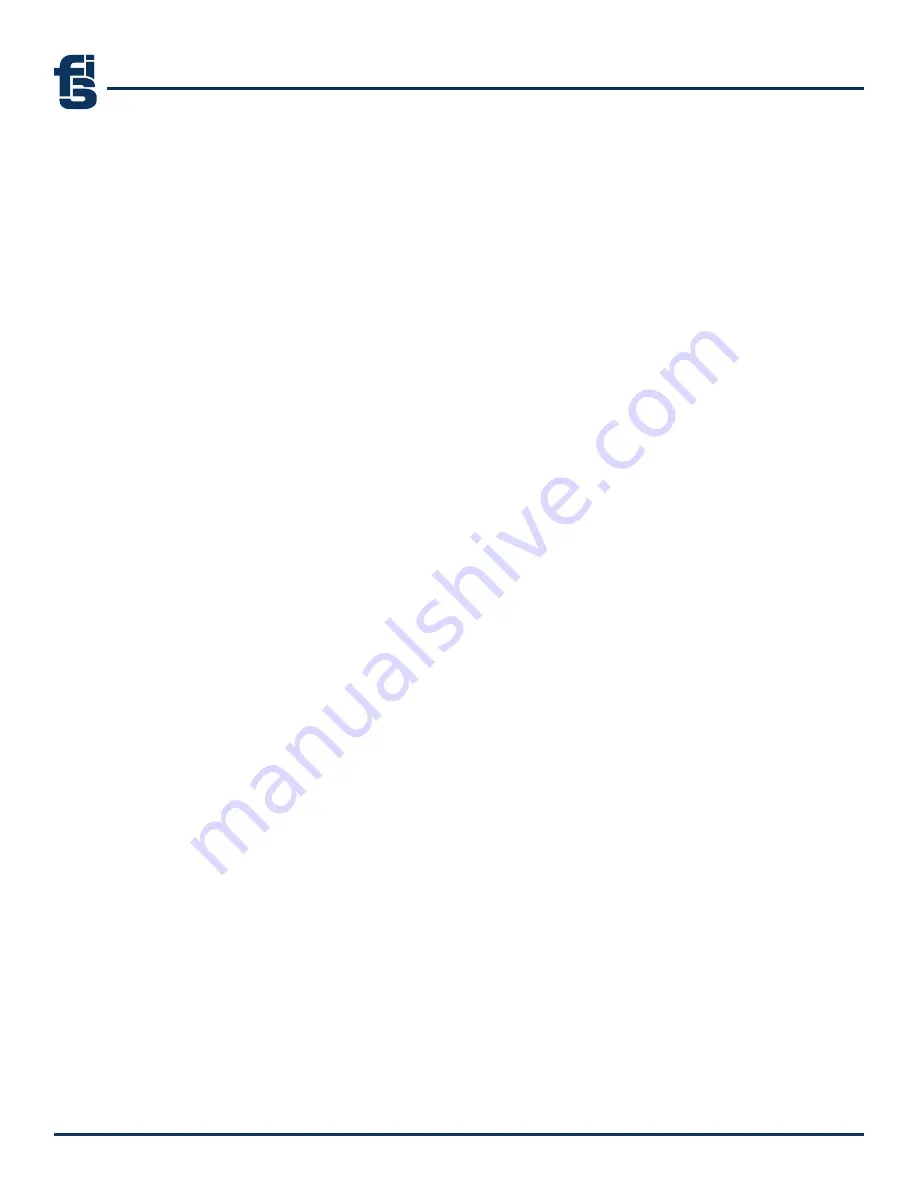
3
Rigid polyurethane foams are formed by the reaction of certain isocyanate compounds with hydroxyl
bearing polyols. Isocyanate (ISO) and polyol (Resin) chemically react to form multi-branched polymer
chains when mixed together in the presence of catalysts and other additives. The generic chemical
name for these compounds is polyurethane.
FSI produces polyurethane chemical systems for use in the manufacturing of cellular plastics
(polyurethane foams). These are two-component systems normally designated “A” and “B”. The “A”
component (ISO) is an MDI polymeric isocyanate. The “B” component (Resin) consists primarily of
polyol, necessary additives, catalysts and a blowing agent.
THE PROCESS AND THE REACTION
In the FSI foam process, the two basic components (the A-SIDE and the B-SIDE) are pressurized in
separate vessels. The chemical systems have blowing agents blended into one or both components.
The two chemicals are then fed through a dispensing tube in a controlled ratio and dispensed. Once
dispensed, the exotherm and sudden decrease in pressure initiate the formation of polyurethane foam.
The foam continues to expand as heat is generated from the chemical reaction of the isocyanate and
polyol. The foam expands until the polymer has obtained sufficient strength to withstand the pressures
of the expanding gases. The final product is a homogeneous cellular product composed of many tiny
closed cells. The percent of closed cells, usually 90 to 96%, determines the efficiency of the foam.
THE TEMPERATURE
Temperature is of utmost importance in processing urethane chemicals. It is essential to control the
reaction by controlling chemical temperatures because this assists in maintaining productivity and
efficiency. Lack of control over chemical temperature results in loss of time, lower productivity, higher
cost, and in some cases, loss of product.
Generally the chemical should be maintained at 80°F (±5°F) throughout the year, unless otherwise
specified by FSI. All SLUG PRO guns must have heated hoses. Hoses should be kept off cold floors.
Whenever possible, heated fixtures should be utilized. If heated fixtures are impractical, the creation
of a heated area of at least 80°F is beneficial. Refer to Product Data Sheet (PDS) for specific operating
chemical temperatures for your system.
PROCESS DESCRIPTION
www.foamsupplies.com
|
www.ecomatetechnology.com
|
1.800.325.4875
Содержание PROFESSIONAL Series
Страница 2: ...www foamsupplies com www ecomatetechnology com 1 800 325 4875 ...
Страница 7: ...PROCESS DESCRIPTION ...
Страница 10: ...5 www foamsupplies com www ecomatetechnology com 1 800 325 4875 ...
Страница 11: ...EQUIPMENT DESCRIPTION ...
Страница 15: ...EQUIPMENT DESCRIPTION 10 STANDARD UNIT www foamsupplies com www ecomatetechnology com 1 800 325 4875 ...
Страница 16: ...11 www foamsupplies com www ecomatetechnology com 1 800 325 4875 ...
Страница 17: ...CHEMICAL PREPARATION STORAGE HANDLING ...
Страница 21: ...INSTALLATION ASSEMBLY ...
Страница 24: ...19 www foamsupplies com www ecomatetechnology com 1 800 325 4875 ...
Страница 25: ...PRODUCTION AND QUALITY CONTROL ...
Страница 32: ...27 www foamsupplies com www ecomatetechnology com 1 800 325 4875 ...
Страница 34: ...29 www foamsupplies com www ecomatetechnology com 1 800 325 4875 ...
Страница 35: ...CHANGING CHEMICAL CYLINDERS ...
Страница 40: ...35 www foamsupplies com www ecomatetechnology com 1 800 325 4875 ...
Страница 41: ...MAINTENANCE ...
Страница 49: ...TROUBLESHOOTING ...
Страница 57: ...SAFETY HANDLING ...
Страница 62: ...57 www foamsupplies com www ecomatetechnology com 1 800 325 4875 ...
Страница 63: ...EQUIPMENT DRAWINGS PARTS ...
Страница 64: ...59 www foamsupplies com www ecomatetechnology com 1 800 325 4875 ...