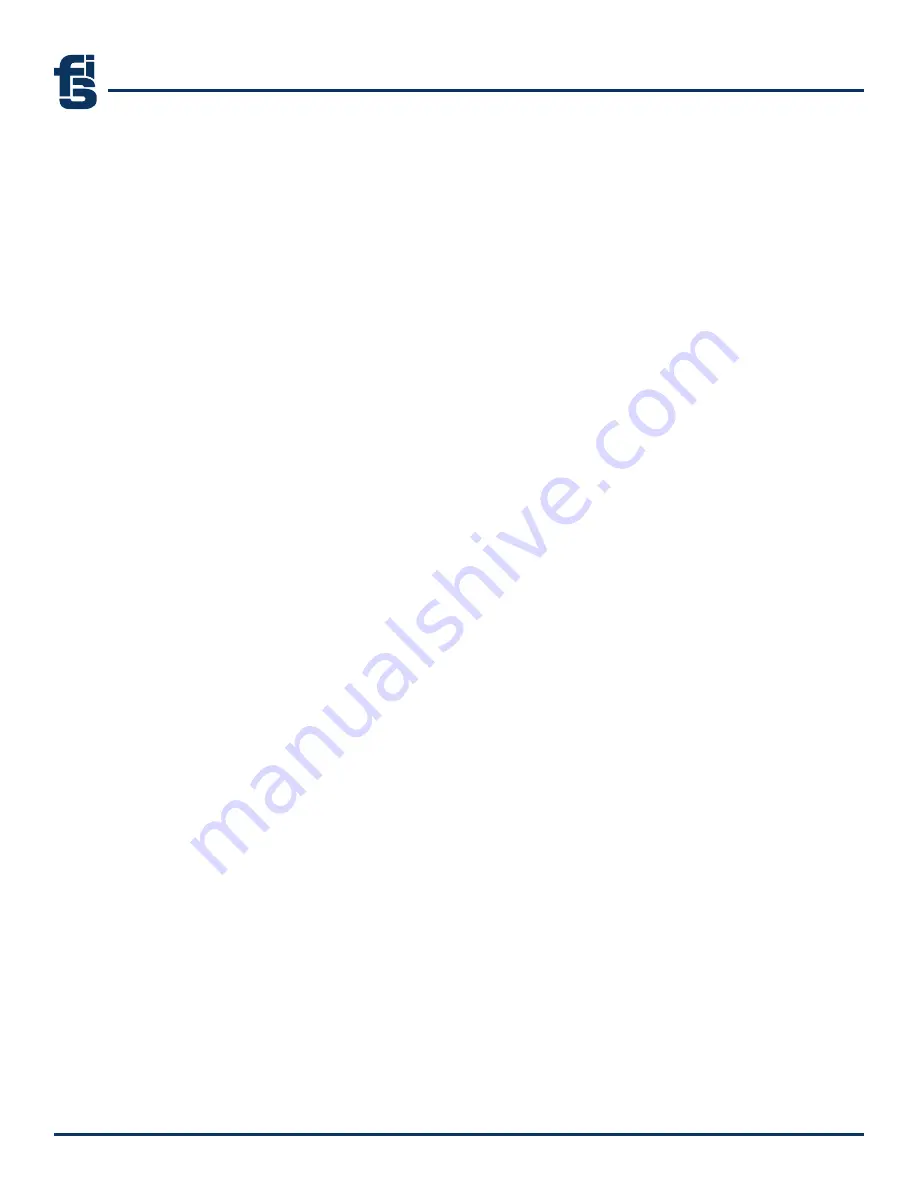
TROUBLESHOOTING
49
Problem: Cured foam is streaked or has excessively coarse or "glassy" cell structure.
Probable causes:
1. A-SIDE and B-SIDE chemicals are too cold for operation.
2. Poor mix.
3. Water or solvent in air purge line or residual solvent in gun head.
Corrective actions:
1. Reduce pressure to 150 PSI in cylinders and bring to proper operating temperature. Chemical
cylinders should be in area where temperature maintained is a minimum of 80°F(±5°F) and
preferably at recommended operating temperature for the specific system. After cylinders
are at operating temperatures, re-pressurize cylinders. (See p. 31)
2. Check and make sure Mix Tube is unclogged. Add a slight amount of air for mixing.
3. Attach water trap to air system. Check airline for dryness and blow out excessive water before
foaming desired part. Verify air dew point is 50°F or less. Verify refrigerant dry is working properly.
Problem: Foam collapses or fails to "cure" or become "Tack-Free."
Probable causes:
1. Chemical flow problem indicating a drastic off-ratio condition.
2. Chemical is too cold.
Corrective actions:
1. See previous problems on restrictions from one side (A or B) at a time. Review and take
corrective actions.
2. Reduce pressure to 150 PSI in cylinders and bring to proper operating temperature. Chemical
cylinders should be in area where temperature maintained is a minimum of 80°F(±5°F) and
preferably at recommended operating temperature for the specific system. After cylinders
are at operating temperatures, re-pressurize cylinders. (See p. 31)
Problem: Foam density is excessively high.
Probable causes:
1. Chemical is too cold.
2. B-SIDE flow restricted from cylinder.
3. Ambient temperature excessively cold.
Corrective actions:
1. Reduce pressure to 150 PSI in cylinders and bring to proper operating temperature. Chemical
cylinders should be in area where temperature maintained is a minimum of 80°F(±5°F) and
preferably at recommended operating temperature for the specific system. After cylinders
are at operating temperatures, re-pressurize cylinders. (See p. 31)
2. Check ratio and examine Mix Cartridge, B-SIDE and A-SIDE check valves, and flow controllers.
3. Warm foaming area with space heater. DO NOT APPLY DIRECT HEAT TO CYLINDERS.
www.foamsupplies.com
|
www.ecomatetechnology.com
|
1.800.325.4875
Содержание PROFESSIONAL Series
Страница 2: ...www foamsupplies com www ecomatetechnology com 1 800 325 4875 ...
Страница 7: ...PROCESS DESCRIPTION ...
Страница 10: ...5 www foamsupplies com www ecomatetechnology com 1 800 325 4875 ...
Страница 11: ...EQUIPMENT DESCRIPTION ...
Страница 15: ...EQUIPMENT DESCRIPTION 10 STANDARD UNIT www foamsupplies com www ecomatetechnology com 1 800 325 4875 ...
Страница 16: ...11 www foamsupplies com www ecomatetechnology com 1 800 325 4875 ...
Страница 17: ...CHEMICAL PREPARATION STORAGE HANDLING ...
Страница 21: ...INSTALLATION ASSEMBLY ...
Страница 24: ...19 www foamsupplies com www ecomatetechnology com 1 800 325 4875 ...
Страница 25: ...PRODUCTION AND QUALITY CONTROL ...
Страница 32: ...27 www foamsupplies com www ecomatetechnology com 1 800 325 4875 ...
Страница 34: ...29 www foamsupplies com www ecomatetechnology com 1 800 325 4875 ...
Страница 35: ...CHANGING CHEMICAL CYLINDERS ...
Страница 40: ...35 www foamsupplies com www ecomatetechnology com 1 800 325 4875 ...
Страница 41: ...MAINTENANCE ...
Страница 49: ...TROUBLESHOOTING ...
Страница 57: ...SAFETY HANDLING ...
Страница 62: ...57 www foamsupplies com www ecomatetechnology com 1 800 325 4875 ...
Страница 63: ...EQUIPMENT DRAWINGS PARTS ...
Страница 64: ...59 www foamsupplies com www ecomatetechnology com 1 800 325 4875 ...