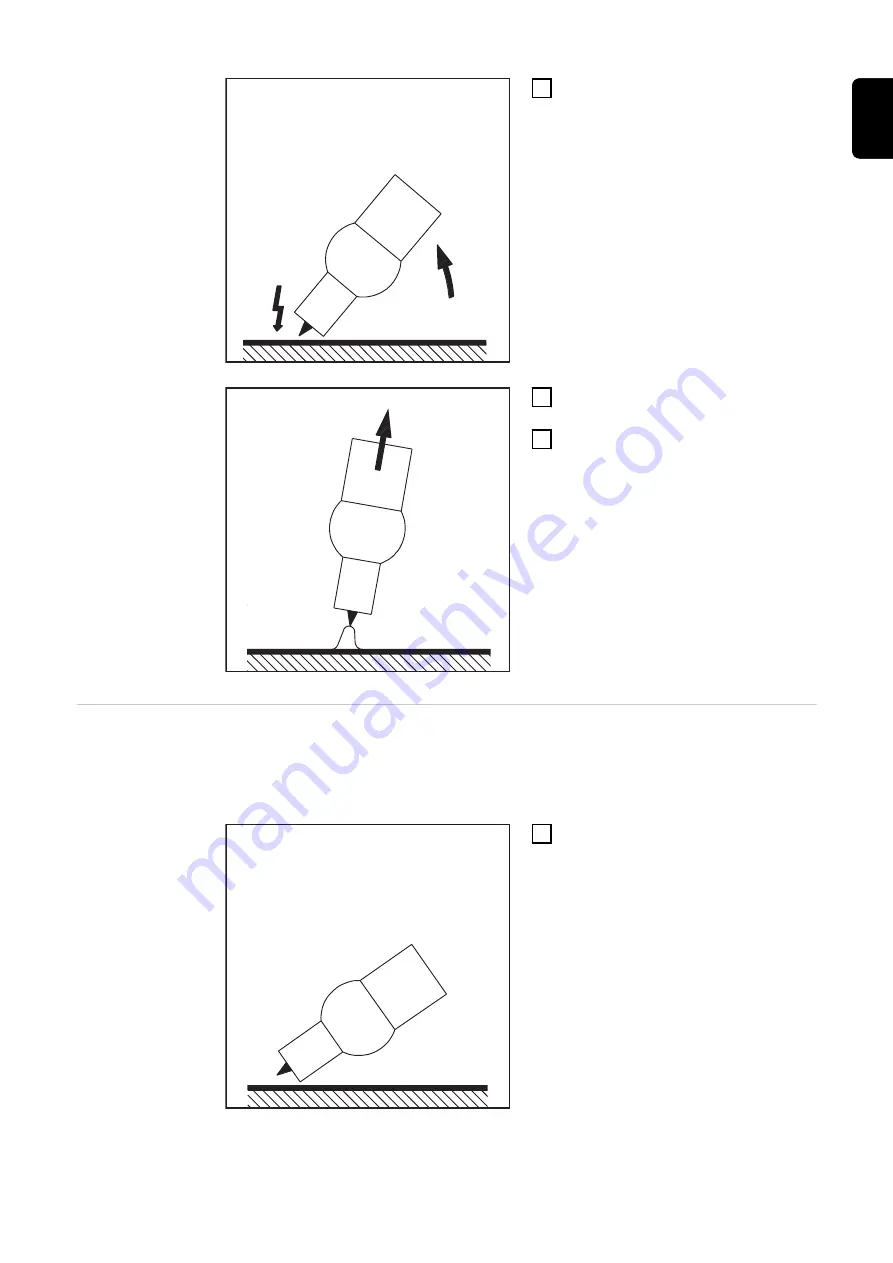
2
Increase the tilt angle of the torch
and actuate the torch trigger ac-
cording to the mode you have se-
lected
The arc ignites without the electrode
touching down on the workpiece.
3
Tilt the torch back into the normal
position
4
Carry out welding
Touchdown igni-
tion
If the HFt setup parameter is set to OFF, HF ignition is deactivated. The welding
arc is ignited by touching the workpiece with the tungsten electrode.
Procedure for igniting the arc using touchdown ignition:
1
Place the gas nozzle down on the
ignition location so that there is a
gap of approx. 2 to 3 mm (5/64 to
1/8 in.) between the tungsten elec-
trode and the workpiece
65
EN
Содержание TransTig 1700
Страница 2: ......
Страница 19: ...General information 19...
Страница 20: ...20...
Страница 25: ...Control elements and connections 25...
Страница 26: ...26...
Страница 45: ...Installation and commissioning 45...
Страница 46: ...46...
Страница 55: ...Welding 55...
Страница 56: ...56...
Страница 72: ...72...
Страница 73: ...Setup settings 73...
Страница 74: ...74...
Страница 87: ...Troubleshooting and maintenance 87...
Страница 88: ...88...
Страница 96: ...96...
Страница 97: ...Appendix 97...
Страница 98: ...98...
Страница 124: ......