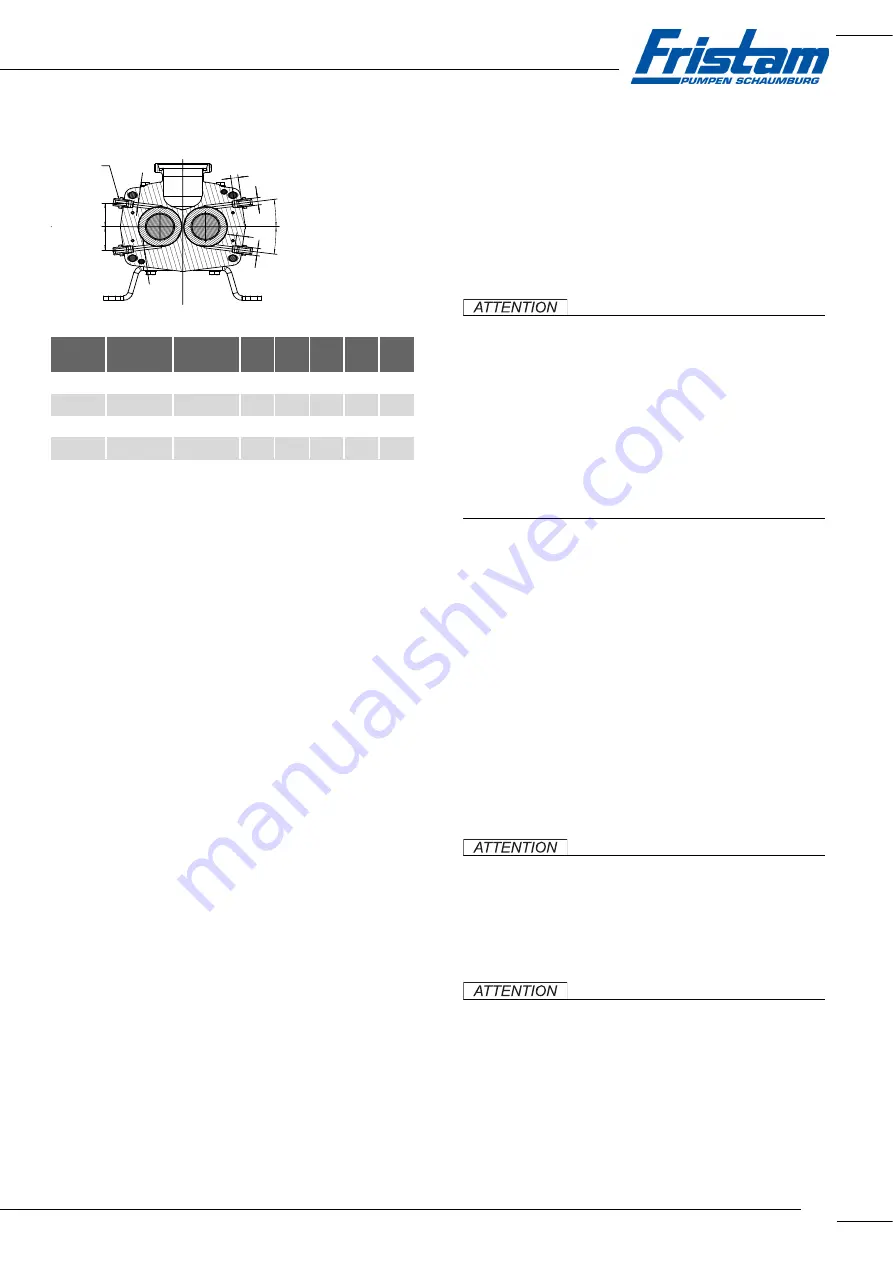
13
1. Fit the feed line
below
the shaft seal.
2. Fit the drain line
above
the shaft seal.
6.9
Cleaning
Only use cleaning agents that meet the technical hygiene stan-
dards for the respective pumped medium.
1. Before closing the pump, make sure that there are no for-
eign substances inside the pump and pipelines.
2. Close the pump.
3. Connect the pipelines.
4. Prior to first use, clean the pump and pipeline system com-
pletely.
7
Operation
7.1
Safety notices
Closed valve in the pressure line
Serious personal injury and property damage caused by a
bursting of the system due to very high pressure build-up.
Both before switching on and during operation, make sure
that all of the pressure line’s valves are open.
Provide a bypass or other approved safety devices for pres-
sure peaks, as this is a positive displacement pump.
Closed valve in the suction line
Damage to the shaft seal due to dry running of the pump.
Both before switching on and during operation, make sure
that all of the suction line’s valves are open.
No pumped medium inside the pump
Dry running of the pump. Damage to the shaft seal.
For single shaft seal pumps, make sure that there is always
pumped medium inside the pump both prior to and during
operation.
7.2
Commence operation
Double shaft seal:
Loss of barrier fluid
Damage to the shaft seal.
During operation, make sure that:
– Barrier fluid with sufficient pressure is flowing through
the double shaft seal (see information on the enclosed
“Data sheet”
),
– The temperature of the barrier fluid is maintained at T <
70°C.
1. Open the valve in the suction line.
2. Open the valve in the pressure line.
3. Fill the pump and suction line with pumped medium to the
upper edge of the pump. Allow any air pockets that may be
present to escape.
4. Only for pumps with barrier or quench fluid:
Verify the necessary barrier pressure. For maximum barrier
pressure, please refer to the
“Data sheet”
in the enclosed do-
cuments.
5. Switch on the motor.
7.3
Observe operation
While the pump is running, observe the following safety notices:
Debris in the pumped medium
Blocking of displacement device and shearing of the shaft.
Eliminate debris in the pumped medium.
– Provide a current limiting device on the gear motor.
Sudden closing of the valves in the pressure line
Damage to the system possible through excess pressure.
During operation do not close the valve in the pressure line
suddenly or for an extended period of time.
Inlet
A
Outlet
B
C
D
E
F
G
FDS 1
FDS 2
G¼" (m/f)
G¼" (m/f)
7.5°
42
12
Ø8
310
FDS 3
G¼" (m/f)
G¼" (m/f)
7.5°
50.5
12
Ø10 375.5
FDS 4
Table 2
A-A
optional (4x)
B
A
C
C
D
D
E
E
F
F