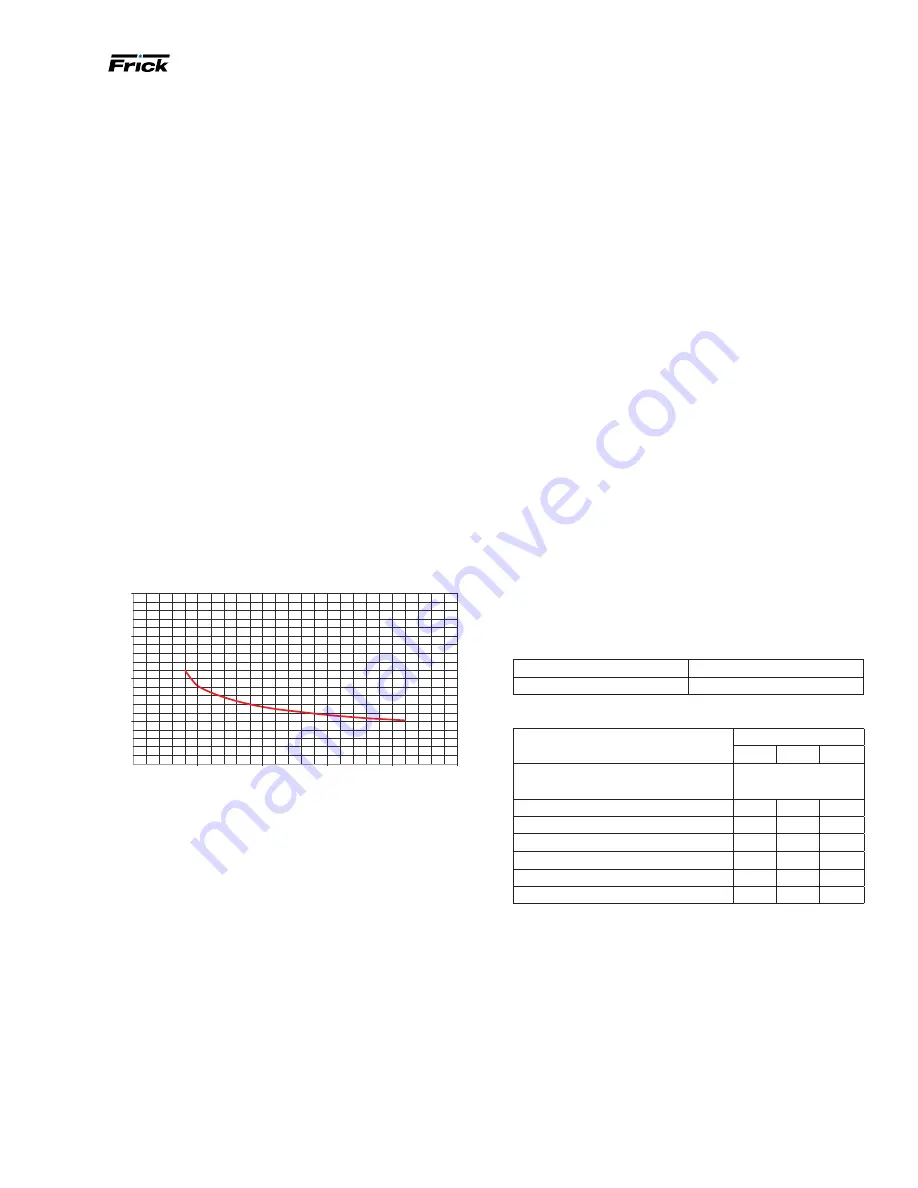
070.750-IOM2 (JAN 21)
Page 7
HPS 273 ROTARY SCREW COMPRESSOR
INSTALLATION - OPERATION - MAINTENANCE
Balance piston
The high pressure compressors are equipped with balance
piston assemblies to reduce load on the axial bearings. Oil
pressure is regulated by a modulating pressure regulating
valve and provides the force, and as a result, must remain
as specified by CoolWare for specific operating conditions.
Shaft seal
The compressor shaft seal is a single-face balanced type
with a spring-loaded, silicon carbide stationary hardened
surface riding against a rotating seat. Carbon and graph-
ite are added to both surfaces to provide self-lubrication.
During operation it is vented to low pressure to provide
extended life.
Motor mount
The HPS 273 series compressor is a foot mounted, open
drive model that can pair with an electric, engine, or
turbine drive.
Design limits
Use CoolWare to determine the limits for a specific ap
-
plication.
Notes for design limits:
1. CR = Compression Ratio. Absolute discharge pressure
divided by absolute suction pressure.
Figure 4: HPS 273 viscosity requirement as function
of speed
2. Maximum discharge temperature depends on oil type
used - normally 150°C (300°F). Refer to
160.802-SPC,
Compressor Oil Specifications
for more detail.
3.
If oil flow is more than 1.5% of swept volume and the
turndown is more than 3, regulate the main oil flow.
Turndown is the actual maximum speed/minimum
speed. CoolWare calculates the oil flow in
Lpm. See
4. The UNISAB and Quantum panels have several lay-
ers of control functions to secure reliable operation.
Depending on many operating conditions, they unload
the slide valve and reduce or increase speed to keep
the compressor running in a safe way. Only as a last
resort do they initiate an alarm and ultimately stop the
compressor.
This is particularly true for the HPS 273 compressor
models on applications with high suction pressure, like
fuel gas boosting. The concern is that the high internal
thread pressure may lead to excessive rotor deflection
and unwanted contact with the rotor housing. For this
reason, proper calibration of the slide valve and slide
stop is essential.
Note:
For 1.3 to 1.96 and 1.7 to 3.0 Vi range machines, the
main oil injection occurs at lower Vi port locations
than compressors operating with the 2.2 to 5.0 Vi
range. This means the UNISAB and Quantum use
lower values for the safeties.
5. In CO
2
applications using miscible oil types POE and
PAG, it is extremely critical to keep water content to
the lowest possible - down to 10 ppm is the goal. The
installation must have large filter dryers with replace
-
able elements that you can effectively service and
vacuum dry before putting back into service.
6. If the temperature difference becomes greater than or
equal to 180°F (355 K) between suction and discharge,
unload the slide valve immediately.
7. The minimum discharge temperature must be a mini-
mum 30°F difference above the maximum dewpoint of
the discharge gases. This applies to part load
conditions and full load operation.
Vibration and sound data
The rotors balance grade is G 2.5 according to
ISO 1940
.
The male rotor drive end of the HPS 273 compressor is
keyless.
Effective vibration velocity must not exceed 8 mm/s RMS
(0.32 in./s) anywhere on the compressor. Alarm level is 12
mm/s RMS (0.47 in./s).
Table 3: Number of rotor lobes
Male rotor lobes
Female rotor lobes
6
8
Table 4: Critical frequencies
Driver speed, rpm
3000 3600 4200
Exiting member/event
Main exciting fre-
quencies (Hz)
Male rotor, rotational, first order
50
60
72
Male rotor, rotational, second order 100
120
144
Female rotor, rotational, first
37.5
45
54
Female rotor, rotational, second
75
90
108
Discharge gas pulsation, first
300
360
432
Discharge gas pulsation, second
600
720
864
Vibration level on the package can be higher, especially
on piping elements, and when the natural frequency of an
element falls together with one of the exciting frequen-
cies. If the vibration level gets too high, a skip frequency
function in the control system activates. After activating,
the motor runs through the critical speed very fast, not
causing any continuously high vibration.
Shaft speed, rpm
1000
20
15
10
5
0
0
2000
3000
4000
5000
Vis
cosity Min., cst