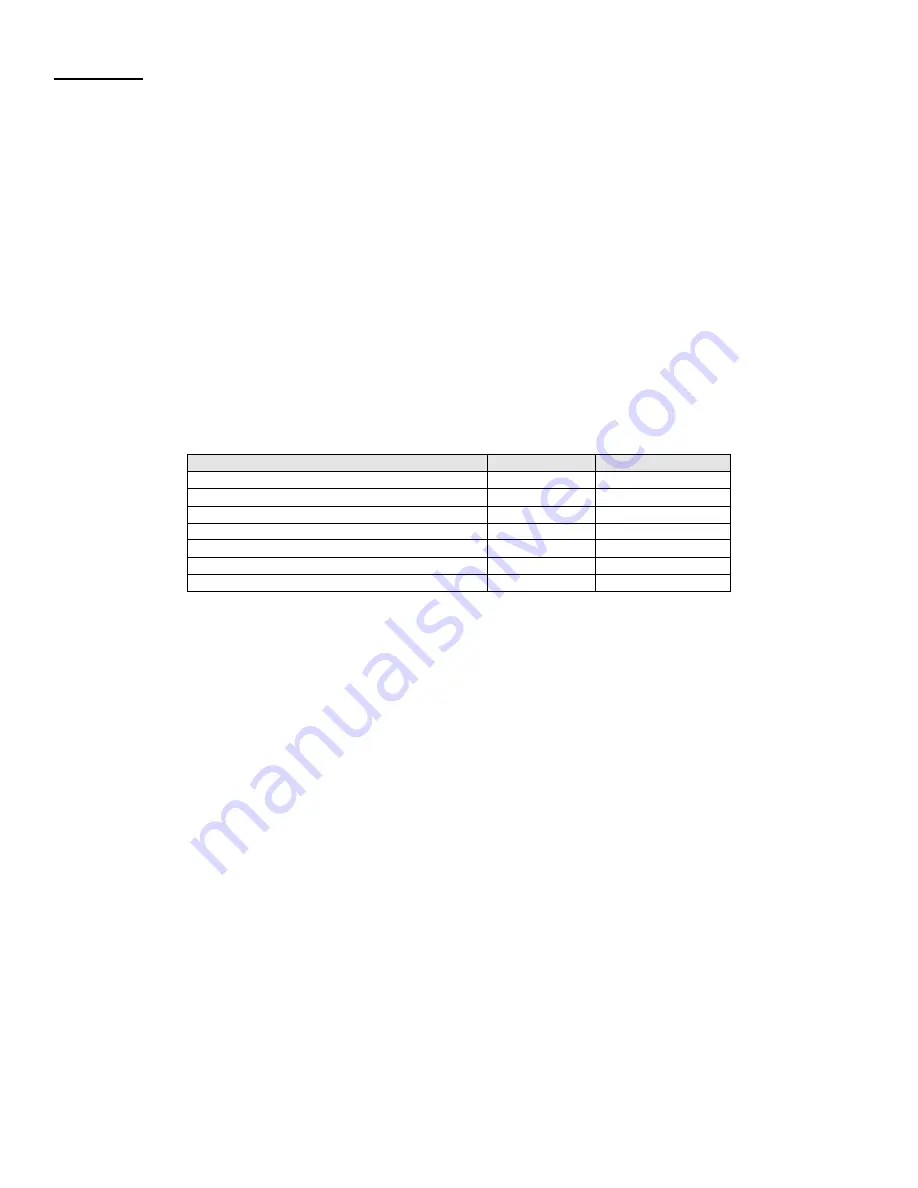
3
Procedure
1.
Disconnect power to the submersible pump at the electrical supply box.
2.
Tag and lock out electrical circuit breakers so they are not turned on accidentally.
Note:
See Figure 1 to identify the particulars of a STP.
3.
Loosen the two junction box mounting bolts, but
don’t
remove them. This will make disconnecting the wire
connector assembly easier.
4.
Carefully disconnect the wire connector assembly, by backing out the hex head bolt and swinging the wire connector
assembly aside (see Figure 1).
5.
Remove the two discharge head mounting bolts, which hold down the discharge head.
6.
Using a hoist, carefully lift the extractable portion of the pump from the tank, being careful not to jam the PMA
against the bottom of the riser on the way out. Lay the assembly down.
7.
Using a 1/4 inch hex key, remove the four cap screws and washers. Using a rocking motion, remove the old PMA
and discard the old flange joint gasket, cap screws, and washers. Inspect flange surface, recess wall, and electrical
connector. Make sure that they are clean and undamaged. DO NOT assemble the new PMA to a damaged flange!
8.
Measure and compare the length of the old PMA with the new PMA. Make certain after installing new PMA there will
be 4 to 5 inches clearance between the bottom of the PMA and the tank for best operation. Figure 1 shows a list of
PMA models with length.
9.
Verify proper capacitor for new PMA from table below. The new PMA may require the installation of a different size
capacitor (3 phase models do not use capacitors).
PMA Model
Capacitor
Voltage Rating
33, 75
15 to 17.5
μ
F
370 V (Minimum)
150, H150
15 to 25
μ
F
370 V (Minimum)
200, H200
40 to 50
μ
F
370 V (Minimum)
VS2, VS4, 75C, 150C, H150C, 200C, H200C
None
None
75B
15 to 17.5
μ
F
440 V (Minimum)
150B, H150B
15 to 25
μ
F
440 V (Minimum)
200B, H200B
40 to 50
μ
F
440 V (Minimum)
* 4 screws, 4 washers, a flange gasket, and a pack of grease are included along with these instructions.
10. Remove the 4 cap screws and washers from the new PMA kit, leaving the new gasket in place on the PMA.
Note:
Be sure the new gasket is used, because the gasket on some competitive PMA’s will block the flow of product
through the motor. This blockage will prevent proper cooling and lubrication of the motor and bearings, and lead
to shorter motor life.
11. Apply grease (from the small grease tube provided) to the mating pieces on the PMA and the motor discharge head
casting, to make assembly easier. If the supplied grease tube isn’t used,
DO NOT use a conductive lubricant
(i.e.
Anti-seize) because this would cause a direct short and motor failure.
12. Align the positioning dowel of the new PMA into the hole in the motor discharge head casting, and make sure that
the metal and gasket surfaces are free of any dirt or foreign particles, carefully push (
using hand force only
) the
new PMA with the new gasket as far as possible against the discharge casting. If hand force will not close the
gasket joint, determine and correct the cause. Do not alter the metal recess or nose diameters, or use screws to pull
into place.
13.
Assemble a new screw with a lockwasher finger-tight in each mounting hole, then gradually tighten all screws in a
cross pattern until all are tightened at 6-7 foot-pounds torque.
Note:
Failure to push the PMA up snug against the discharge casting prior to tightening the cap screws, or failure to use
a cross-pattern while tightening the bolts could break the discharge casting or strip the threads in the PMA.
14. Apply a multi-purpose grease to the three o-rings on the manifold discharge head. Make sure that any sand or
gravel that might have been picked up on the entire unit is cleaned off, and using a hoist, reinstall the extractable
portion of the pump.
15. Replace the hex head cap screws in the discharge head and finger-tighten. Be sure the discharge head is down
flush on the manifold.
16. Reconnect the wire connector assembly and tighten the hex head bolt.
17. Tighten hex head cap screws in the discharge head, and junction box mounting bolts to approximately 30 foot-
pounds.
18. Follow system manufacturer instructions to reassemble the system.