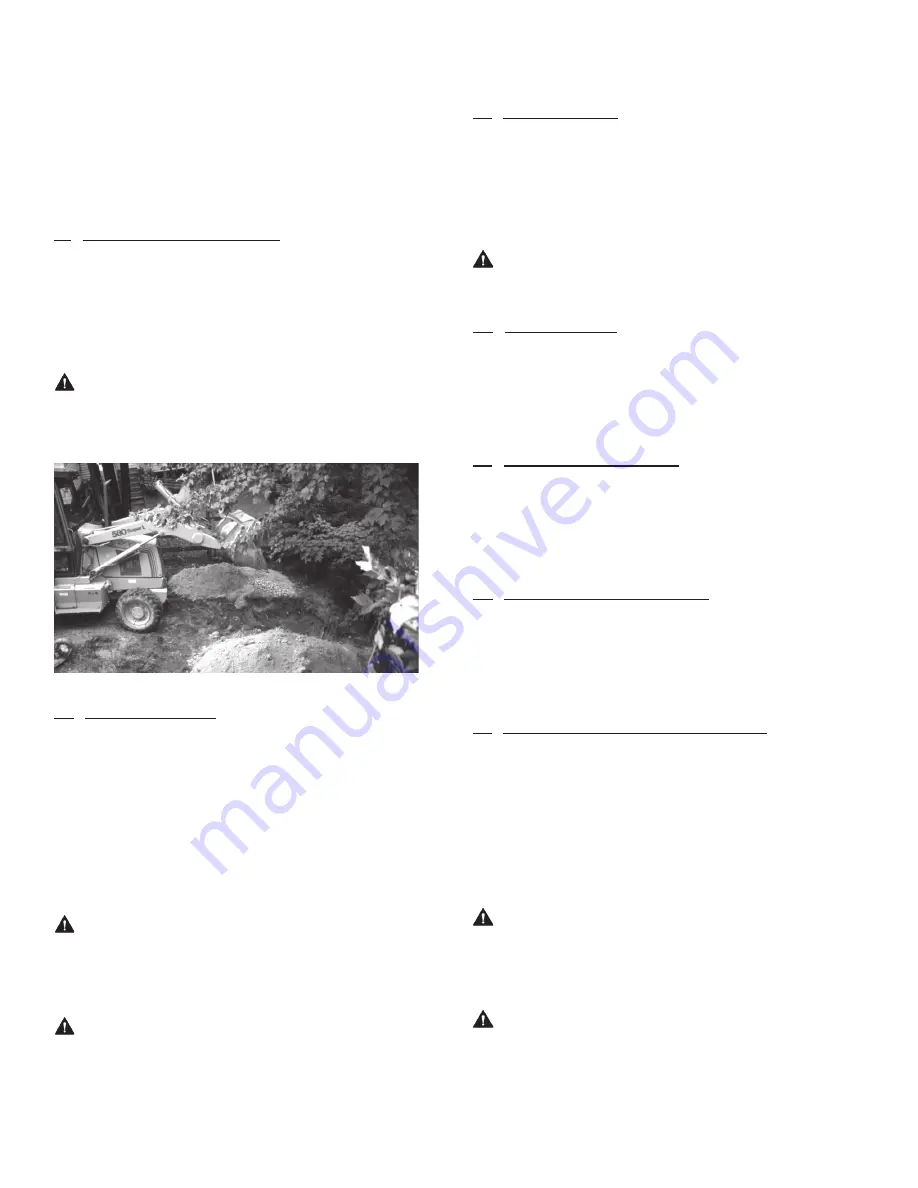
8
3. INSTALLING COLLECTION TANK
Strict adherence to these proven methods and procedures will ensure
the long-term performance of your PowerSewer® system. Studies
by regulatory agencies and trade organizations indicate that the
most significant source of leaks and failures in underground storage
structures is improper handling and installation.
3.1 Excavating for Collection Tank
The excavation should provide adequate space for the collection
tank, piping, other buried equipment, and for the placement and
compaction of backfill materials. The size, shape, and wall slope should
be determined by the site’s soil conditions, depth of excavation,
shoring and sheeting requirements, and safety regulations.
WARNING
Safe excavation procedures are the
responsibility of the installer Work safety requirements are defined
by US Department of Labor 29 CFR part 1926, subpart P, Excavations
3.2 Excavation Location
Excavation for the PowerSewer® collection tank should be made with
due care to avoid undermining foundations of existing structures
and contact with overhead or underground utilities. In the absence
of specific code requirements, maintain a distance of 7' with a slope
of 45° from the collection tank to adjacent structures, foundations,
footings, and property lines. Additional distances may be required
to assure that any loading carried or created by adjacent structures
cannot not be transferred to the PowerSewer® collection tank.
WARNING
Locate all underground and overhead
utilities before excavation Call 888-258-0808 at least two business
days before excavating for a referral to your local “One-Call” utilities
location center
NOTICE
Do not locate the PowerSewer® excavation in
drainage areas or other low points on the building lot Failure to
locate PowerSewer® in proper location will void warranty
3.3 Excavation Depth
Excavate the hole to a depth equal to 4-1/2" plus the collection tank
depth. When finished, the collection tank rim should be at least
1-1/2" above final grade. The final grade should slope away from the
collection tank to avoid surface water from ponding on or around the
collection tank and cover.
NOTICE
Do not install collection tank rim below
final grade Below grade installations void the warranty
3.4 Bedding Material
Place and compact gravel bedding to a minimum depth of 6".
The gravel should be a naturally rounded aggregate, clean and
free-flowing, with a particle size not less than 1/8" or more
than 3/4" in diameter.
3.5 Setting the Collection Tank
Ensure that all packaging materials have been removed from the
PowerSewer® prior to setting the collection tank. Lift and lower the
collection tank using the methods previously outlined in section 1.4,
Transportation and Handling.
3.6 Positioning the Collection Tank
Center and level the collection tank on the compacted gravel bedding.
Fill the collection tank with water to the bottom of the discharge
piping to limit the movement of the collection tank during backfilling
and pouring of the concrete ballast.
3.7 Ballasting Collection Tank with Concrete
A concrete ballast anchor must be poured over the collection tank’s
integral anti-flotation flange to properly secure the collection tank in
the ground. This will prevent the collection tank from floating up out
of the ground due to hydrostatic pressure from high water tables. The
concrete ballast must be a minimum of 8" thick, extending at least 4"
above the integral anti-flotation flange and 12" out from the collection
tank. See the installation drawing on page 28 for details.
CAUTION
Concrete ballast is not optional
Failure to properly ballast the collection tank may result in
collection tank floating up out of the ground, causing damage
to the piping and equipment
NOTICE
This ballast method requires that proper
compacted backfill material be used as described in section 10,
Backfilling Around the Collection Tank This is the only acceptable
method of ballasting the collection tank To receive detailed
anti-flotation calculations or approval of alternative methods,
contact Franklin Electric Technical Services at 866-271-2859
Содержание PowerSewer V4PS
Страница 1: ...V4PS Installation Operation Maintenance Manual...
Страница 31: ...31 NOTES...