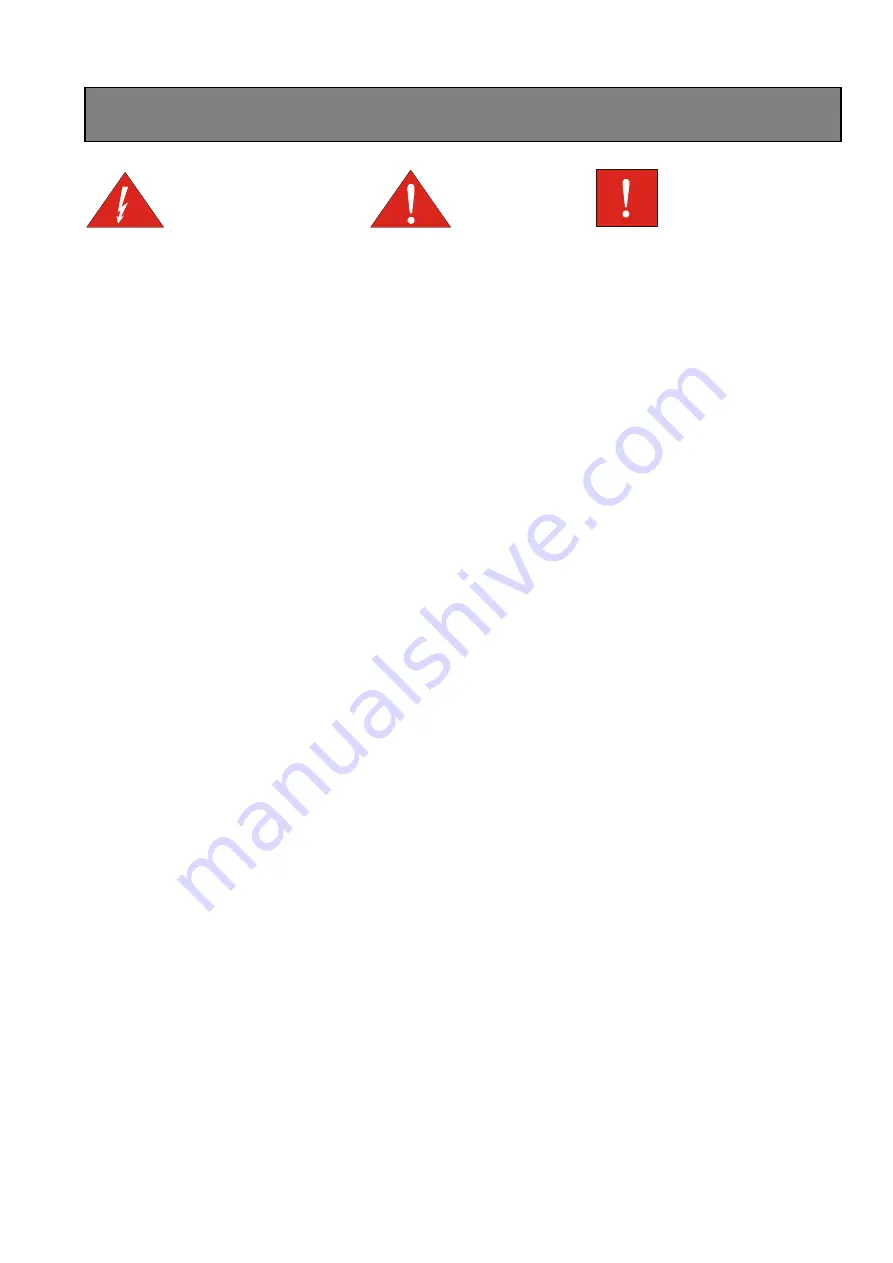
6
DANGER
RISK OF ELECTRIC
SHOCK
DANGER
WARNING
The “
Mains power on”
LED comes on to indicate that the board is working properly.
The motor can be governed directly by the operator with man present
(Manual)
or by remote
signals
(Automatic)
by means of the
“Automatic – Off – Manual”
buttons; (when the
automatic button is pushed the related LED above the button lights and the control panel is
ready to receive remote signals from the sensors and floats).
The motor works in
Automatic
by means of the
G1
command that can be any clean contact
(e.g. float or pressure switch).
The min/max level is controlled by the sensor commands based on how the internal
DIP-SWITCH 1 AND 2
are set:
1=ON 2=OFF
−
› Emptying
1=OFF 2=ON
−
› Filling
ATTENTION: it is dangerous to set both the dip-switches to on or off position: in first
case the motor runs ever without level sensor deactivation; in second case the motor
doesn’t start with any level.
The sensor control input can also be used for the Start/Stop operations, closing the
G1 control with a wire jumper and respectively connecting two controls (e.g. floats)
between “Com-Min (Stop float)” and “Com-Max (Start float)” in place of the 3
sensors.
N.B.: When using this configuration the sensors alarm must be overriden by
SETTING THE DIP-SWITCH 3 TO OFF POSITION, otherwise the “level alarm” LED for
the min/max level will come on (based on the E/F setting) and the alarm output will
be activated.
3=ON
−
› Level sensor alarm enabled
3=OFF
−
› Level sensor alarm disabled
In the event the "Min/Max level" sensors are tripped
, the motor stops, the
“LEVEL ALARM”
light comes on and the Alarm output relay is tripped.
The sensitivity of the level sensors can be adjusted by means of the “SENS. SONDE”
(SENSOR SENSITIVITY) Trimmer, based on the conductibility of the liquid in which
they are immersed. By increasing the sensors sensitivity, correct functioning is also
possible in the presence of liquid with poor conductivity.
The green pilot light “
MOTOR ON
” indicates the functioning of the motor.
If the Overload protection is tripped
, the motor stops and the red
“PROTECTION ON”
and
“LEVEL ALARM”
LED lights on .
Push RESET to reset the alarm;
Check for the cause of the malfunction before restoring the motor to operation
The motor overload protection can be overridden by set the dip-switch 4:
4=ON
−
› Amperometric protection enabled: “PROTECTION ON” and “LEVEL ALARM”
leds li motor stop + alarm output
4=OFF
−
› Amperometric protection disabled: “PROTECTION ON” led lighting
without motor stop and without alarm output . In this manner the “PROTECTION ON”
alarm LED is activated but the motor continues to run and the alarm output does not
activate.
The amperometric protection tripping current can be adjusted by means of the
“CORRENTE MOTORE” (MOTOR CURRENT) Trimmer, based on the rated absorption of
the motor; the adjustment can be made from a minimum of 2A to a maximum of 22A.
(To determine Imax read In writing on chart model of the membrane).
The cut-in delay time is fixed at 5 seconds and can be overridden during setting by
bridging the “ ESC.TIM.TA” Jumper;
GENERAL NOTES :
During the calibration for Over-Load Protection, start the motor 2-3 times to check the
correct operating.
5. STANDARD OPERATION
Содержание Simplex-Up
Страница 17: ...17 CONFIGURATION 1 CONFIGURATION 2 NOT USE WITH DIRTY WATER 17a CONNECTION DIAGRAMS FOR SIMPLEX UP M...
Страница 18: ...18 CONFIGURATION 3 CONFIGURATION 4 17b CONNECTION DIAGRAMS FOR SIMPLEX UP M...
Страница 19: ...19 CONFIGURATION 1 CONFIGURATION 2 NOT USE WITH DIRTY WATER 17c CONNECTION DIAGRAMS FOR SIMPLEX UP T...
Страница 20: ...20 CONFIGURATION 3 CONFIGURATION 4 17d CONNECTION DIAGRAMS FOR SIMPLEX UP T...