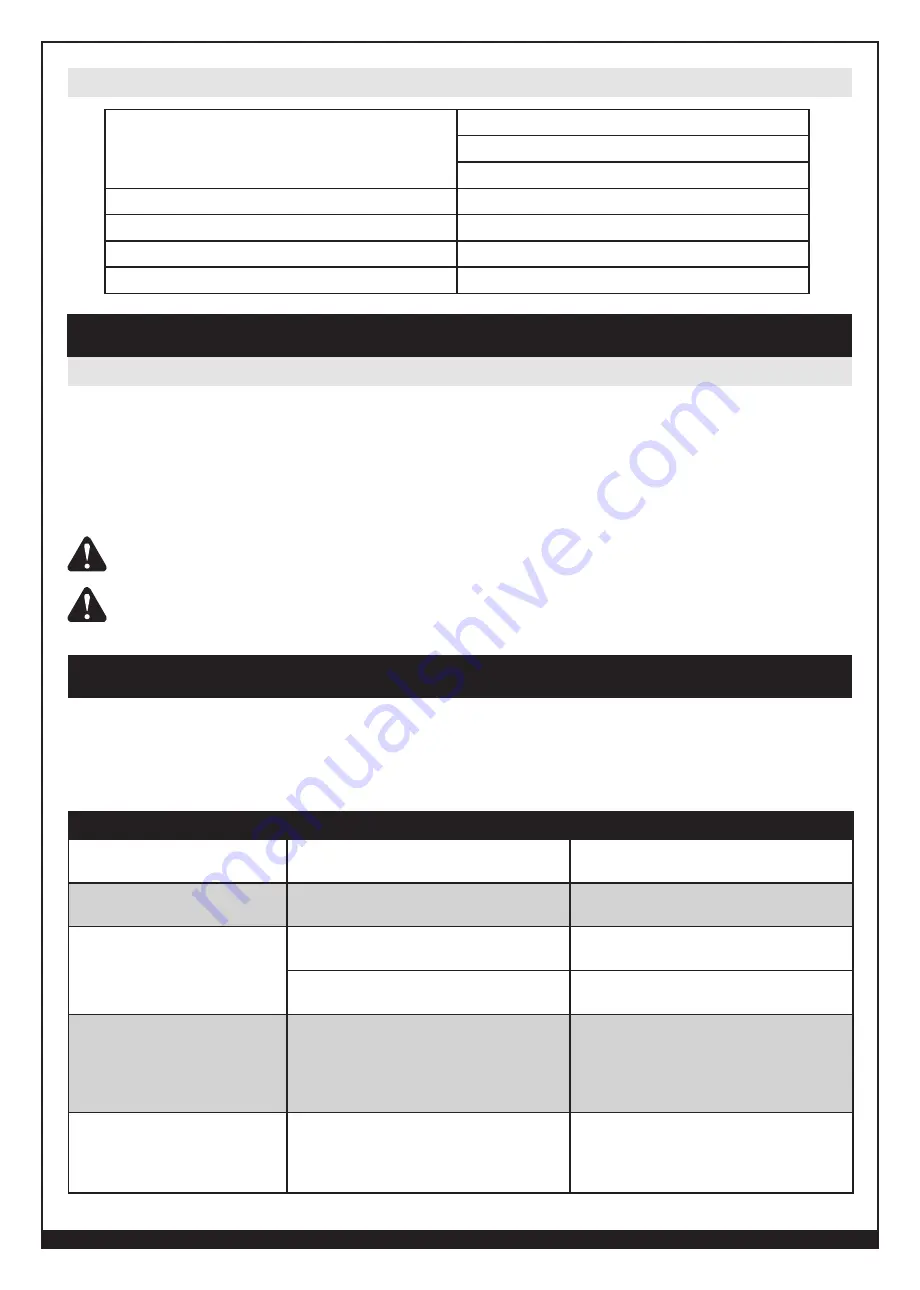
18
WWW.FORNEYIND.COM
A Good Starting Point for Aluminum TIG
Amperage
< 1/8 “ = 140 MAX
1/8 “ – 3 /16” = 170 MAX
1 /4” + = 200 MAX
6a AC Freq
90 HZ
6b AC Balance
70 % EN
6c PULSE (HZ)
1
6d PULSE ( % ON)
50%
General Maintenance
This welder has been engineered to need minimal service providing that a few very simple steps are taken to properly
maintain it.
1. Replace INPUT POWER CABLE, ground cable, ground clamp, or torch/electrode cable when damaged or worn.
2. Avoid directing grinding particles towards the welder. These conductive particles can build up inside the machine and
cause severe damage.
3. Periodically clean dust, dirt, grease, etc. from your welder. Every six months or as necessary, remove the side panels
from the welder and use compressed air to blow out any dust and dirt that may have accumulated inside the welder.
WARNING: DISCONNECT FROM POWER SOURCE WHEN CARRYING OUT THIS OPERATION.
4. Check all cables periodically. They must be in good condition and not cracked.
WARNING: ELECTRIC SHOCK CAN KILL!
Be aware that the POWER SWITCH, when OFF, does not remove
power from all internal circuitry in the welder. To reduce the risk of electric shock, always unplug the welder from its AC
power source and wait several minutes for electrical energy to discharge before removing side panels.
The following is a troubleshooting table provided to help you determine a possible remedy when you are
having a problem with your welder.
This table does not provide all possible solutions, only those possibilities considered likely to be common
faults.
PROBLEM
POSSIBLE CAUSE
POSSIBLE SOLUTION
All LEDs OFF.
No input power.
Connect machine to proper input power
source.
No output power, Fan not
operating.
POWER SWITCH is OFF.
Ensure POWER SWITCH (rear) is in the ON
position.
FAULT CODE F01 DISPLAYED.
Exceeded duty cycle; thermal protector
engaged.
Verify that circuit breaker has not been tripped
in your main power panel. Reset if needed.
POWER SWITCH is OFF.
Ensure POWER SWITCH (rear) is in the ON
position.
FAULT CODE F02 DISPLAYED.
No voltage or incorrect voltage supplied to
welder.
Make sure the machine is plugged in. Check
the status of your INPUT VOLTAGE INDICATOR
LED. It should be illuminated. Check the voltage
of your outlet. If it is 10% more or less than
120V or 230V, call a qualified electrician.
FAULT CODE F05 DISPLAYED.
Torch triggered before machine is ready
Torch triggered or turned on before
machine is powered on will fault. Release
torch trigger and machine will reset within
five seconds
Maintenance & Servicing
Troubleshooting