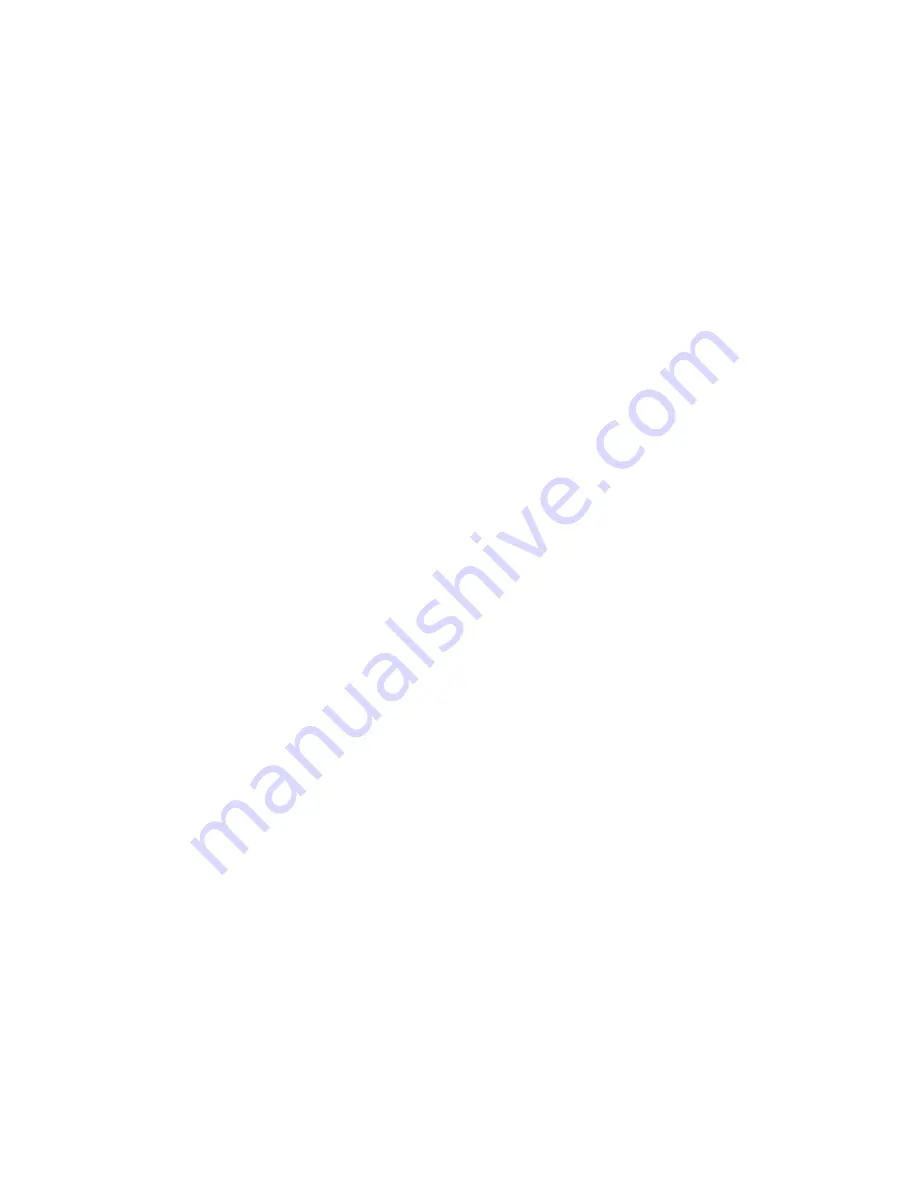
HCD710A, HMD710A
15
Error faults:
The Horizon PC board monitors various operating parameters including high pressure, auger gearmotor amperage
limits, clogged drain, and low water alarm conditions. There are three types of errors namely “soft” (time delay)
"hard" (reset), and “run”.
§
Soft errors will automatically reset after the 1 hour time delay or can be reset by cycling power.
§
Hard errors must be reset on the control board.
§
Run errors will give an indication of a problem, but will allow continuous normal operation.
Soft errors:
HI AMPS: The PC board monitors the amperage of the auger motor. Should the gear motor experience current
draw above the allowable limit, the machine will shut down and the TIME DELAY and HI AMP will be illuminated.
After the time delay the machine will restart and the TIME DELAY and HI AMP will clear.
LO WATER: During operation, the water level cycles between the normal low and normal high sensors. Should the
water be shut off to a running machine, a soft error will occur. The error sequence is as follows: During operation,
the water level falls to the normal low sensor, and when it does the water feed solenoid is energized. If water is not
detected at the normal low sensor within 10 seconds, a soft error will occur. The machine will shut down, but the
water feed solenoid will remain energized. Should water return, it will fill to the normal low sensor and the machine
will resume normal operation. The error will clear automatically.
Water feed error: While in making ice mode, if the water level does not fall below the low probes for 9 minutes, the
machine will enter a 1-hour time delay soft error with the LOW WATER light flashing. After the time delay expires,
the machine will try to make ice.
HI PRESSURE: Should the refrigeration pressure rise above 425 psi, the machine will shut down and the TIME
DELAY and HIGH PRESSURE will be illuminated. After the time delay, and if the pressure has fallen back below
the reset point of 295 psi, the machine will restart and the TIME DELAY and HIGH PRESSURE will clear.
Hard error:
DRAIN CLOG: The drain clog sensor, located in the chassis will detect the presence of water just below the top
edge of the chassis. After the sensors are dried off, the machine must be reset on the control board to resume
operation.
Run errors:
DRAIN CLOG: When the machine shuts down on a full bin and there has been 30 minutes of cumulative
compressor run time, the machine will purge before starting. During this purge, if water does not get below the low
probe in the reservoir within 20 seconds, the Drain Clog LED will light. The machine will continue to run but this is
an indication of a poorly draining machine and must be addressed.
Relay output indication:
Each relay on the board has an indicator light associated with its output. For example, when the relay for the water
feed solenoid is energized, the adjacent indicator light glows green.
Evaporator flushing sequence:
During operation, the purge solenoid will open in order to drain water. There are two drain settings to choose from:
High TDS or Low TDS. (There is a rocker switch behind the front cover of the machine.) The intent is to drain the
Total Dissolved Solids from the machine while it makes ice.
While ice is being made, the TDS of the water in the evaporator increases in TDS concentration. Without periodic
draining, the TDS levels will climb to very detrimental levels, levels that will cause scale to form and cause poor
machine operation. The Low TDS setting will allow the machine to operate for one hour before going through the
flushing sequence; the High TDS setting will allow the machine to run for 11 minutes before going through the
flushing sequence.
The flushing sequence toggles the purge and fill solenoids three times. That is, the purge solenoid will energize
until the water level drops below the low probe. The fill solenoid then energizes until water reaches the high probe,
and so on for 3 cycles.
Typically, High TDS might be considered levels above 200 PPM, but local experience and varying water chemistry
may compel a High TDS setting for best performance in even lower TDS levels.
Off cycle: At the completion of off-cycle time delay, the machine checks for a cumulative 30 minutes of ice making
time since the last
off-cycle flush. If the cumulative ice making time exceeds 30 minutes, the machine will open
the drain valve for 60 seconds to drain the evaporator in its entirety. It will then refill with water and begin making
ice. If the ice making time is less than 30 minutes, the machine will start and begin making ice without draining the
evaporator.
Содержание HCD710ABS
Страница 16: ...16 HCD710A HMD710A Wiring diagram...
Страница 32: ...32 HCD710A HMD710A 9 1 8 7 6 4 5 3 2 Air cooled assembly...
Страница 34: ...34 HCD710A HMD710A Electrical box 1 4 3 2 7 5 6 8...
Страница 38: ...38 HCD710A HMD710A Skins assembly 9 8 10 2 1 11 7 5 4 3 6...