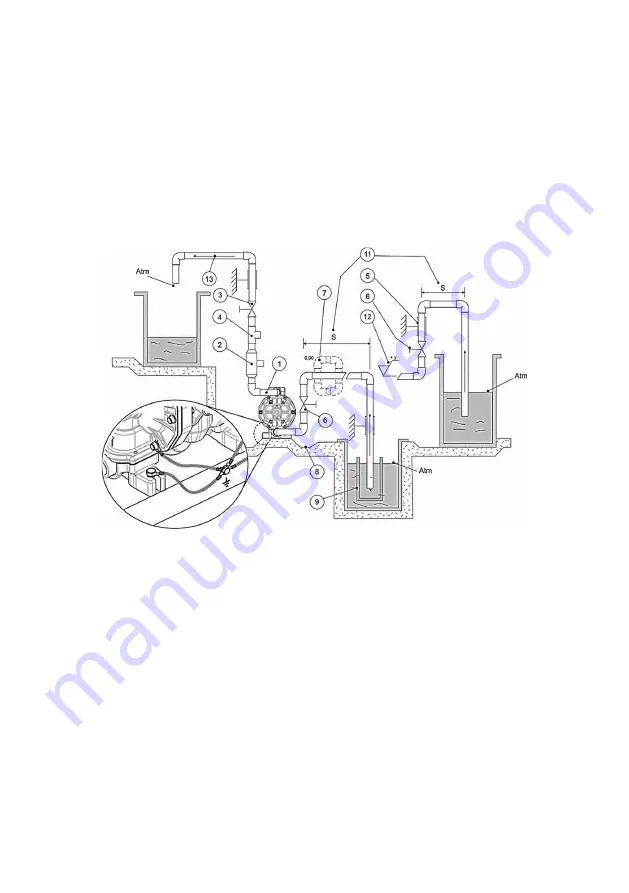
39 Rev. 03
• ensure drainage of fluids which may come out of the pump
• fix the pump using all the available locking holes, the support points must be levelled
• arrange for enough room around the pump for the movements of an operator
• arrange for free space above the pump for lifting it
• inform about the presence of aggressive fluid with suitable colored labels in accordance with the related standard
• do not install the pump (built with thermoplastic material) near heat sources
• do not install the pump in places with risk of fall of solids or fluids
• do not install the pump close to fixed workplaces or visited areas
• install additional protection shield, for the pump or for the persons as appropriate. If the diaphragm breaks the fluid may
enter into the pneumatic circuit and come out from the pump discharge port
• install a spare equivalent pump connected in parallel
• the pump must be always electrically earthed
• if the pump is made from conductive materials and is suitable for flammable products, each pump casing must be equipped
with a suitable ear thing cable: DANGER OF EXPLOSION AND/OR FIRE
• WARNING The pumps must always be grounded irrespective of any organ to which it is connected. Lack of grounding or
incorrect grounding will cancel the requirements for safety and protection against the risk of explosion
• WARNING: the pump during operation is in PRESSURE, check appropriately report the hazardous conditions.
START UP
• check the correct execution of what indicated in the INSTALLATION paragraph
• check that the intake and delivery pipes of the hydraulic circuit are correctly connected
• open the intake and delivery valves of the pump hydraulic circuit
• open the 3-way valve on the air circuit
• set the operation point requested for the pump: properly adjust the air pressure and delivery that supplies the pump.
With pressure values under 2 bar the pump may stall, with pressure values above 7 bar it is possible that breakdowns and/or
yields may
occur with consequent spillage of the pumped fluid
• for pumps with split manifold the two pumped fluids must have the same viscosity value, very different viscosity values may lead
to stall
problems and/or diaphragms breaking
• do not operate at the limits of the operation curves: the maximum head or maximum delivery (total absence of leaks and intake
height in
the delivery circuit)
• check that there are no anomalous vibrations or noise due to the too elastic support structure, unsuitable fastening or cavitation
• after 2 hours of operation stop the pump correctly and check the tightening of all the bolts on the pump
USE
• do not operate valves or shunts during the pump operation
• Risk of harmful water hammers in case of incorrect or sudden operations (valves must be operated only by trained personnel)
• empty and wash accurately inside the pump in case different fluids must be pumped
• insulate or empty the pump if the fluid crystallization temperature is equal to or below the ambient temperature
• stop the pump if the fluid temperature exceeds the maximum allowed temperature indicated in the GENERAL NOTES;
if the exceeding temperature is about 20% it is necessary to inspect the status of the internal parts
• stop the pump and close the valves in case of leaks
• Wash with water only if chemical compatibility allows it ; alternatively use the suitable solvent that does not generate hazardous
exothermic
reactions
• consult the fluid supplier to decide the most suitable fire-prevention method
• Empty the pump in case of long periods of disuse (particularly with fluids which are particularly tending to crystallize)
Содержание P07
Страница 2: ...2 Rev 03...
Страница 34: ...34 Rev 03 PHOENIX 1000...