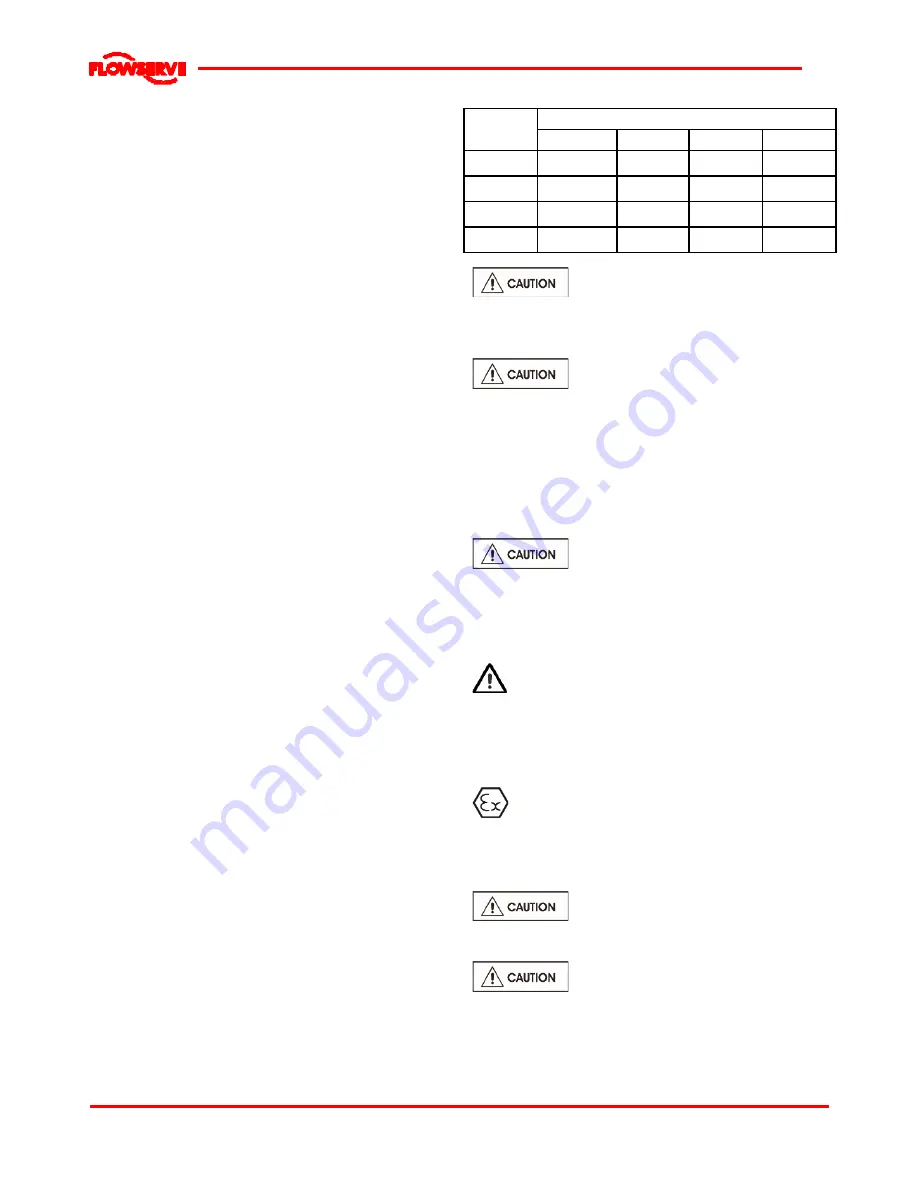
WDX USER INSTRUCTIONS ENGLISH 71576322 06-05
Page 24 of 46
®
5.2.4 Lubrication schedule
5.2.4.1 Oil lubricated bearings
Operating conditions and severity of service will
determine the intervals between oil changes. In
general higher oil temperatures will require more
frequent oil changes.
For pumps on hot service or in severely damp or
corrosive atmosphere, the oil will require changing
more frequently. If the bearings maintain a stable
temperature and if there has been no contamination
of the oil, the interval between changes may be
longer.
Lubricant and bearing temperature analysis can be
useful in optimising lubricant change intervals.
Generally, the oil should be changed every 6 months.
If the bearing temperature increases, check
immediately for improper lubrication or a faulty
bearing.
The lubricating oil should be a high quality mineral oil
having foam inhibitors. Synthetic oils may also be used
if checks show that the rubber oil seals will not be
adversely affected.
The bearing temperature may be allowed to rise to 50
ºC (122 ºF).above ambient, but should not exceed 82
ºC (180 ºF). A continuously rising temperature or an
abrupt rise, indicate a fault.
5.2.4.2 Grease lubricated bearings
The bearings are prelubricated when supplied.
Lubrication frequency is as indicated in the table
below. After a 2 years period the bearing should be
completely cleaned, checked and repacked with new
grease.
The free bearing space should not be filled up more
that 50 % to 60 % of its content see 5.2.3. Care must
be taken to avoid both under and over-lubrication.
Over lubrication will cause the bearings to run hotter
than normal, while under-lubricated bearings could
wear prematurely.
The characteristics of the installation and severity of
service will determine the frequency of lubrication.
Lubricant and bearing temperature analysis can be
useful in optimising lubricant change intervals.
Lubricati on frequenci es in hours of operation
Pump size
1450 RPM
1750 RPM
2950 RPM
3550 RPM
1,5 WDX
3000
2200
1500
1200
2 WDX
3000
2200
1500
1200
3 WDX
2700
2000
1400
1100
4 WDX
2500
1700
1300
1000
Never mix greases containing different
bases, thickeners or additives.
5.3 Direction of rotation
Starting or operating pumps with the
wrong direction of rotation can be harmful to the
pumps.
Ensure that the pump rotation is the same as the
arrow on the pump casing.
It is preferable to check the direction of rotation
before installing the coupling. If not, the pump must
be filled in with the liquid before start-up.
If maintenance work has been carried
out to the site's electricity supply, the direction of
rotation should be re-checked as above in case the
supply phasing has been altered.
5.4 Guarding
Guarding is supplied fitted to the pump set.
If this has been removed or disturbed ensure that all
the protective guards around the pump coupling and
exposed parts of the shaft are securely fixed.
5.5 Priming and auxiliary supplies
Where there is any risk of the pump being run
against a closed valve generating high liquid and
casing external surface temperatures it is
recommended that users fit an external surface
temperature protection device.
Ensure all electrical, hydraulic,
pneumatic, sealant and lubrication systems (as
applicable) are connected and operational.
Ensure the inlet pipe and pump casing
are completely full of liquid before starting continuous
duty operation.
These operations must be carried out by personnel
with approved qualifications.